Hello world!
2022-07-12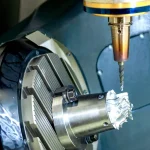
加工中的精度与准确度:主要区别
2024-10-26如何知道加工的零件是否精确和准确?使用不同的检查和测量来确保这一点。然而,首先必须了解准确性和精密度的概念。
它们主要涉及尺寸标注的正确性和重复性,这对于加工 CNC 零件和产品的整体质量至关重要。虽然它们彼此独立,但它们的总体衡量标准决定了零件的精度或功能。本文将讨论准确度和精度之间的差异,并详细说明如何实施这些差异以实现所需的结果。
让我们开始吧!
机械加工的精度是什么?

“精度”一词指的是加工测量结果之间的接近程度。它意味着多次试验中数值的重复性。例如,如果您在三次连续测量中读取轴的直径 6 毫米、6.01 毫米、6 毫米和 6.02 毫米,则可以说它非常精确。然而,精度在加工中有两个重要方面:重复性和再现性。
重复性是指特定加工过程或操作中零件的一致性。例如,铣床设置会创建具有相同特征、尺寸和表面光洁度的多个批次。
可重复性是指由相同设计但不同的机器、设置和工具转换而来的零件的接近度。这意味着即使工具或其他设置发生变化,零件也不会彼此偏离。例如,自定义 CAD 模型可以使用铣削和车削加工转换为尺寸接近的物理零件。
因此,精密加工=重复性+再现性
机械加工中的精度是什么?

测量结果与实际值的接近程度。如果测量结果与理论值(真实值)相同,则测量结果完全准确。
其次,加工精度是指尺寸或其他性能与初始设定值的接近程度 CNC加工设计。它有三个关键组成部分:偏差、稳定性和线性。
方面 | 定义 | 加工精度的重要性 |
偏见 | 测量值与真实值/参考值之间的差异(系统误差)。 | 它通过最小化固定偏差来确保测量的准确性。 |
稳定性 | 随时间推移测量的一致性。 | 它可以防止因环境变化、工具磨损等原因造成的变化。 |
线性度 | 整个操作范围内测量误差的一致性。 | 它可确保不同零件尺寸和规格的结果准确。 |
因此,加工精度不仅在于达到目标值,还在于确保过程在所有操作条件下保持无偏、稳定和线性。
精度和准确度之间的主要区别
接下来,让我们从三个不同方面客观地比较精度和准确度;它们的定义、误差类型和测量。
不同的定义
精度是一组测量数据之间的接近程度。因此,值越接近,精度就越高。而准确度是测量值与真实值或参考值的接近程度。
错误类型分类
系统误差和随机误差是两种误差类型,随机误差与精度有关,系统误差与准确度有关。
随机误差
这些是由于不可预测的原因造成的误差,测量结果只显示波动。这是测量仪器或技术的局限性。例如,CNC技术本身的能力对图纸中提到的尺寸的准确性有一些限制。
系统性错误
系统误差是由温度波动、刀具磨损、错位、G 和 M 代码误差、错误设置和测量仪器缺陷造成的。随着系统误差的增加,加工精度会下降。
测量数量
高精度意味着测量的数据集非常精确(值彼此接近)。因此,标准偏差或方差量化了精度。另一方面,准确度涉及与参考值相比的单次测量或多次测量的平均值。
机械加工的典型精度和准确度示例
虽然准确度和精密度都与测量有关,但它们具有不同的特性。测量可以有任意组合;精确和准确、准确但不精确等。有一个流行的例子,即向目标投掷飞镖,可以说明精密度和准确度之间的区别。
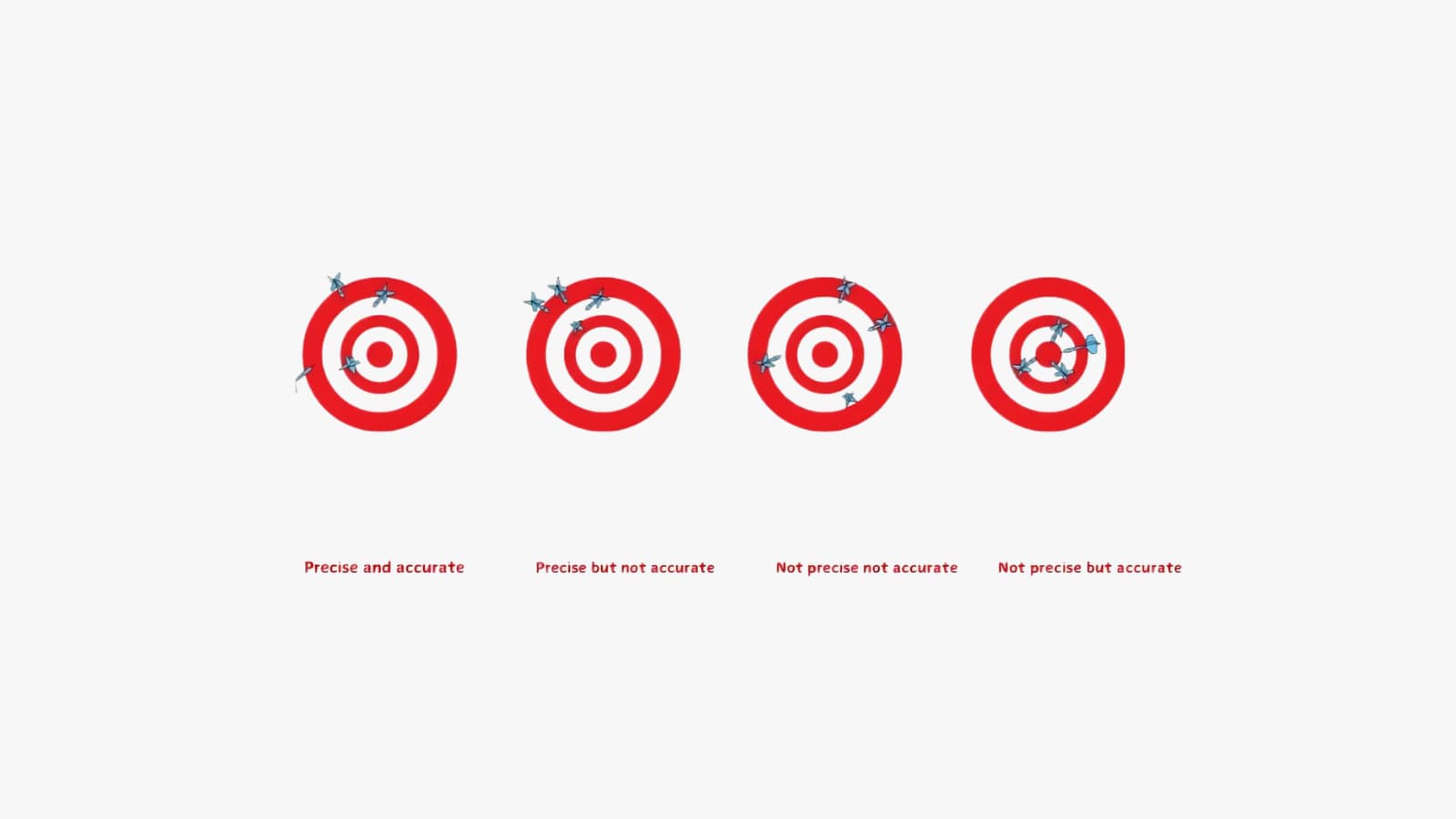
接下来我们举个例子 设计中提到的直径为 10 毫米的加工钢轴 讨论准确度和精确度结合的典型场景;
精确和准确
测量仪分别显示 10.00、10.02、10.01 和 10.00 毫米。直径接近真实值(10 毫米),并且彼此接近,最大方差为 0.02 毫米。
不精确但准确
测量值分别为 10.01、10.02、9.98、10.03、9.99 和 10.01mm。这些值接近参考值(10mm),但彼此并不接近。最大差异为 0.06mm。
精准但不准确
测量值分别为 9.90、9.91、9.90、9.91 和 9.92 毫米。它们是精确的,原因是数据彼此接近但不接近直径的真实值。
不精确也不准确
测量结果显示 9.90、9.86、9.95、9.79 和 9.80 毫米。这里,它们既不接近彼此,也不接近真实值(10 毫米)。这意味着这些值不精确且不准确。
零件生产中精度和准确度的重要性
制造过程中的精度有三个重要方面:功能性、性能和装配时的配合度。同时,精度对于多批次零件的一致性至关重要。
精密加工
它指的是生产具有高精度和重复性的机械零件。因此, 精密数控加工 使用各种仪器并测量准确度和精确度以确保所需的标准。
生产设备校准
制造过程中的任何系统性错误都表明机器、工具或检查精度的仪器存在缺陷。这就像重新校准制造和测量设备的通知。
减少材料浪费并提高可靠性
测量单个加工零件的精度有助于识别有缺陷的零件并立即调整制造流程。早期识别单个有缺陷的零件可以减少浪费。
零件组装
精确的零件对于更顺畅、更快速的装配过程至关重要。精确、准确的组件可以减少停机时间和人工成本。因此,生产线的整体效率会提高。
测量和检测加工零件的精度和准确度
测量系统
通常,加工零件采用两种类型的测量系统:尺寸测量和无尺寸测量。坐标测量机、量块、卡尺和 3D 激光扫描是测量尺寸特征的常用方法。另一方面,粗糙度测试、洛氏硬度测试和无损检测属于无尺寸测量。
关于检验,首件检验 (FAI) 是测量中最重要的因素。它通常涉及遵守标准和法规。例如,一般机械部件符合 ISO 9001 规定,航空航天部件符合 AS9100 规定。
测量系统分析
测量系统分析的目的是确定测量数据中的变化有多少来自系统本身,有多少是由于零件或过程造成的。
一些分析方法是;
- 稳定性: 多次试验的数据是否表明校准正确?
- 偏见:平均测量值与真实值有何区别?
- 线性度:在精确测量范围内,测量精度如何变化?
精密测量
它包括在相同条件下检查同一部件的重复测量,以通过重复性和加工再现性产生类似的结果。
- 重复性研究:同一操作员使用同一工具(千分尺或卡尺)测量同一部件的一致性。最小差异表示高重复性。
- 再现性研究:测试不同的 CNC 机械设置或操作员使用相同仪器是否产生类似的结果。
精度测量
准确度是指测量值与真实值的接近程度,而偏差、稳定性和线性是主要影响因素。精密测量仪器(如坐标测量机和卡尺)会获取数据,这些数据可用于计算。接下来,它通常以准确度的 % 表示;
准确度 = (测量值 – 真实值/真实值) x 100%
如何提高加工过程的精度和准确度?

设计阶段、机器能力、加工变量、设置和工具以及 数控加工 共同决定了整体的精度和准确度。因此,要提高它们,必须考虑很多因素。
减少人力投入、CAM和一致准确的零件。自动化操作,提高测量仪器的可靠性。
融入可制造性设计 (DFM) 原则
可制造性设计是指创建与高精度 CNC 机械能力完美匹配的 3D 模型,选择最佳材料,简化设计并遵循标准要求。例如,保持一致的 GD & T 并减少对工具访问造成挑战的复杂性。只有与现有机器和工具兼容的设计才能制造出精确而准确的零件。
- 选择平衡性能和成本的材料
- 创建与制造流程兼容的设计
- 考虑简化装配过程的因素。
- 标准化
确保设计符合严格的公差限制
在标注尺寸和公差时,请检查特定 CNC 机器的范围,并在加工图中相应地设置公差。在这里,确保标注的公差非常接近可实现的范围。例如,如果 CNC 铣床可以保持低至 ± 0. 13 毫米的公差,您可以在设计中将公差设置为更接近此值,即 ± 0. 125 毫米、± 0. 120 毫米等。同时,整个图纸中的公差也要统一。
优化加工切削参数
加工切削参数应根据工件材料、几何形状复杂程度和刀具类型进行选择。进给率、主轴转速、切削深度和冷却液流量等不同参数对精度和准确度的影响不同。例如,进给率对准确度的影响更大,而主轴转速对精度的影响很大。
CNC 编程是另一个因素。刀具路径和 G 和 M 代码 确定要加工的零件的最终尺寸。因此,在计算机软件中模拟刀具路径并对其进行优化,以实现高精度和准确的功能。
此外,加工工具的精度也会影响结果。任何工具磨损、轻微偏差或过热都可能导致许多缺陷,甚至彻底失败。
实施有效的夹具技术
有效的夹具不仅要固定工件和切削刀具,还要确保机床底座和机架的稳定性和刚性。精密夹具可以紧紧夹住工件,消除刀具移动、振动和错位误差。此外,设置夹具的操作员的经验也会影响精度。因此,夹具应由专业机械师设置。
以下是一些实施技巧;
- 使用定制和硬夹具进行批量生产
- 应用3-2-1工件定位原则
- 模块化夹具适用于原型设计和小批量
利用运动耦合实现一致对准
运动耦合的主要优点是它提供了出色的重复性并减少了互换性误差。此外,最小的接触点为动态加工过程提供了更高的运动自由度。运动耦合的另一个特点是对准与夹紧力无关。即使力发生变化,工件仍与刀具保持对准。此外,运动耦合还有助于精确控制工件上的刀具路径。