The significance of material selection in vacuum casting
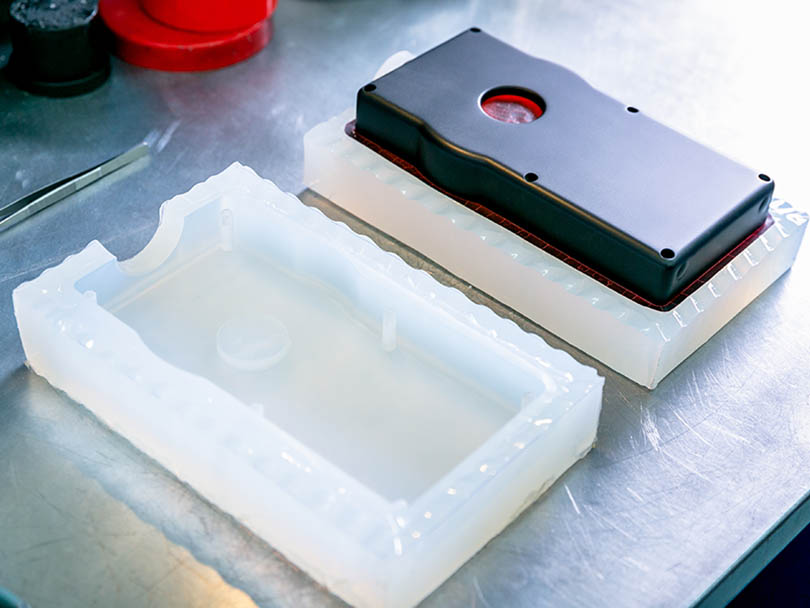
-
Material selection significantly affects the performance and life of vacuum cast parts. For example, materials with high tensile strength and heat resistance are essential for components exposed to stress and high temperatures. Conversely, applications that require flexibility and impact resistance benefit from softer materials.
-
The flow characteristics of the selected material determine the quality of the finished product. If the molten material flows smoothly within the cavity, a fine and excellent surface effect will be produced. This is crucial for prototypes and high-quality parts where visual appeal is as important as functionality, such as consumer electronics and high-end automotive components.
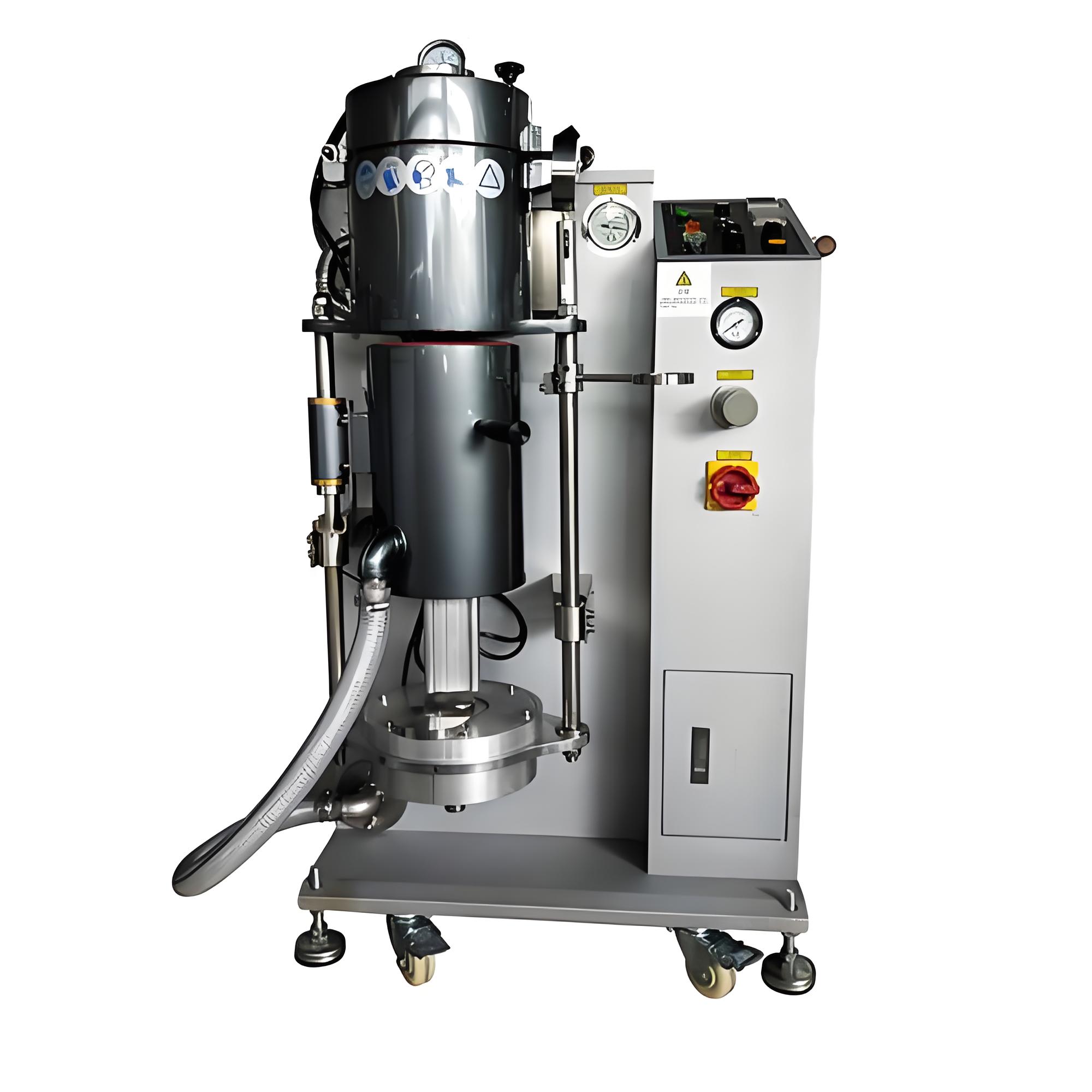
Advantages Of Vacuum Casting
In this section, we will explore the advantages and limitations of the vacuum casting process.
Technology | Type | Materials | Lead Time | |
---|---|---|---|---|
3D PRINTING | Digital Light Synthesis (DLS) | Rigid: CE 221, EPX 82, EPX 86 FR (Flame Retardant), FPU 50, IND 405, MPU 100 (biocompatible), RPU 70, RPU 130, UMA 90 Non-Rigid: EPU 40, EPU 41, IND 147 - HDT 230, SIL 30 | Typically four business days; expedited orders in as few as two business days | |
3D PRINTING | Multi Jet Fusion (MJF) | Standard: Nylon PA-11, Nylon PA-12, PA-12 GF, PP, and TPA Color: CB Nylon PA 12 | Four to five business days depending on material and color | |
3D PRINTING | Fused Deposition Modeling (FDM) | ABS-ESD7, ABS-M30, ABS-M30i, Antero840CN03, ASA, Nylon PA-6, Nylon PA-12, Nylon PA-12 CF (Carbon-Filled), PC-10, PC-ABS, PEKK (Antero 800NA), PPSF, ST-130, Ultem 1010, Ultem 9085, Ultem 9085 CG | As few as three business days | |
3D PRINTING | Stereolithography (SLA) | Accura 25, Black, Color (multiple), Clear, Durable, Elastic, Flexible 80A, High Temp, Surgical Guide (biocompatible), Rigid 4000, Tough 1500, Tough 2000, White | As few as three business days for prototypes; production or high-volume runs are examined on a case-by-case basis | |
3D PRINTING | Direct Metal Laser Sintering (DMLS) / Selective Laser Melting (SLM) | Aluminum (AlSi10), Inconel 625, Inconel 718, Maraging Steel, Titanium (Ti64) | Custom quotes available on a case-by-case basis; lead times vary | |
CNC MACHINING | Most Common: ABS, PC, PE, PP Other Supported Materials: HDPE, LDPE, Nylon (PA 6, PA 11, PA 12, PA 66), PC/ABS, PEEK, PEI, PET, PMMA/Acrylic, POM (Acetal/Delrin), PS, PSU, PU, TPE, TPU, TPV Additives and Fibers: Colorants, flame retardants, glass fibers, plasticizers, UV absorbers | Plastic: ABS, Acetal (Delrin), Nylon 6, Nylon 30%GF, HDPE, PEEK, PC, PTFE (Teflon), PVC, UHMW Metal: Aluminum (2024, 6061, 6082, 7050, 7075), Stainless Steel (303, 304, 316, 17-4, 420), Other Steel (Mild Steel, Alloy Steel, Tool Steel), Other Metals (Brass, Copper, Titanium) T1 Samples: As little as two weeks Post-T1 Approval: As little as one week for orders of <10,000 parts | Eight to 10 business days for orders of <50 parts | |
URETHANE CASTING | Shore D (65 D C85 D) | Standard: ABS-like (80D), PC-like (84D), PE-like (65D), PP-like (70D) High-Performance: 12 Sec Burn (78D), ABS-High Impact (78D), High Impact FR (UL-94V0) (85D), Hi Temp (84D), Nylon/Delrin-like (84D) FDA: ABS-like (80D), ABS-High Strength (85D), Hi Impact Class VI (85D) Clear: Optical Clear (80D, water-clear), PC-like (84D, haze/pale yellow) | First Article (FA): As few as three days, depending on part geometry Post-FA Approval: As little as two weeks | |
URETHANE CASTING | Shore A (15 A C94 A) | Standard Elastomers: 15A C94A High-Performance Elastomers: 15A C90A Water-Clear Elastomers: 45A, 65A, 70A, 90A Silicone: 15A, 25A, 35A, 38A (medical-grade), 40A, 42A, 50A, 53A, 60A, 75A | First Article (FA): As few as three days, depending on part geometry Post-FA Approval: As little as two weeks |
Typical Cast Urethane Uses
Automotive Industry
Prototype parts: dashboard, door handles, functional parts: lamp covers, air vents
Consumer Electronics
Device housings: smartphones, laptops, wearable technology prototypes, buttons and switches
Medical and Healthcare
Medical device prototypes: housings, components, custom orthopedic devices, device housings
Aerospace Industry
Prototype parts: Nacelle interior parts, Ducts and vents, Non-structural parts: Covers, hulls