SURFACE TREATMENT SERVICE
Highlight the surface quality and enhance the core competitiveness.
Diversified surfaces express the uniqueness of the products.
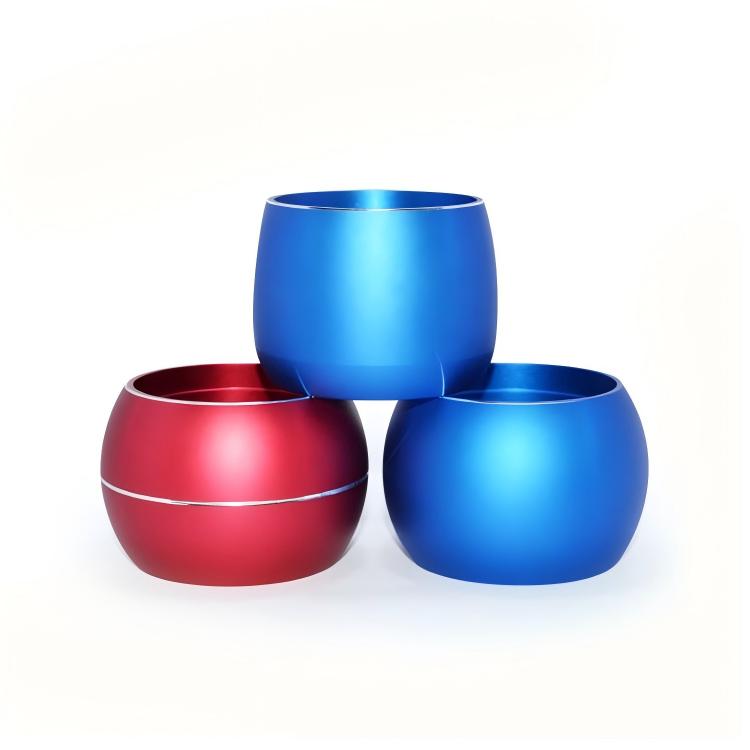
Overview of Surface Treatment
Surface treatment refers to different processes that endow the surface of prototype parts with a specific appearance, giving them a unique or desired look and feel, and achieving the set effects by using various techniques.
HXC provides high-quality surface treatment services for all components and parts produced through different manufacturing methods. We have a team of skilled professionals who carry out their work in a correct and professional manner.
By selecting the appropriate surface treatment process, we help our customers enhance the competitiveness of their products in the market. High-quality die-casting surface treatment can enhance the visual appeal of products and enable them to stand out in the highly competitive market.
OUR PROCESS
Grinding
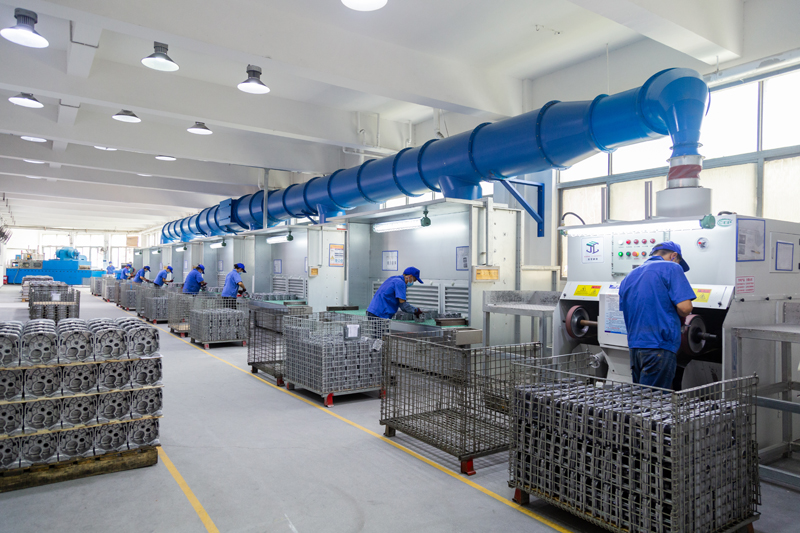
Post-processing
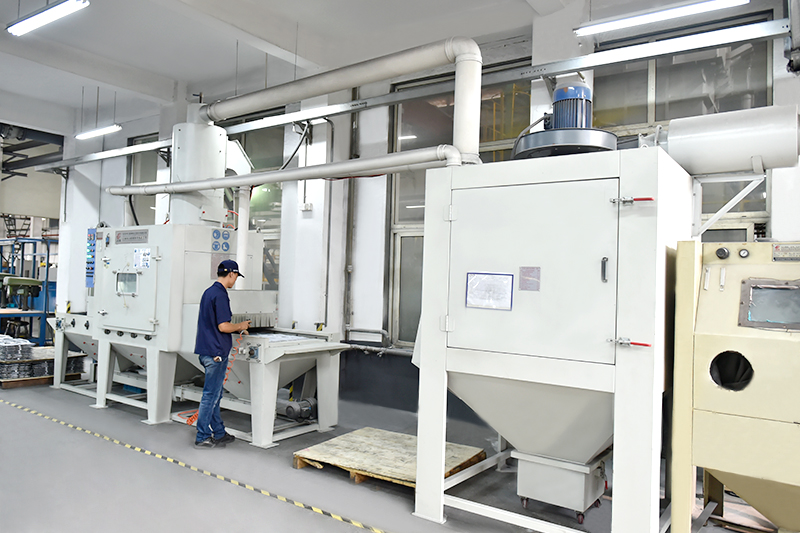
Back-end Processing
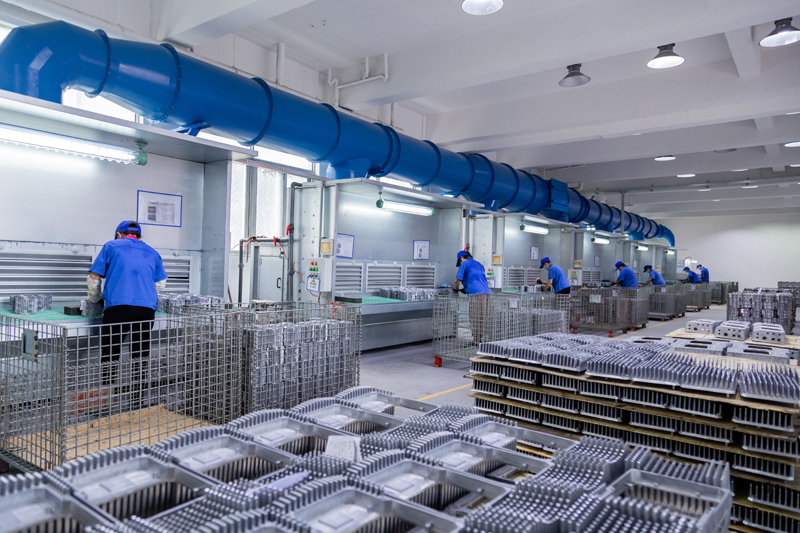
Inspection
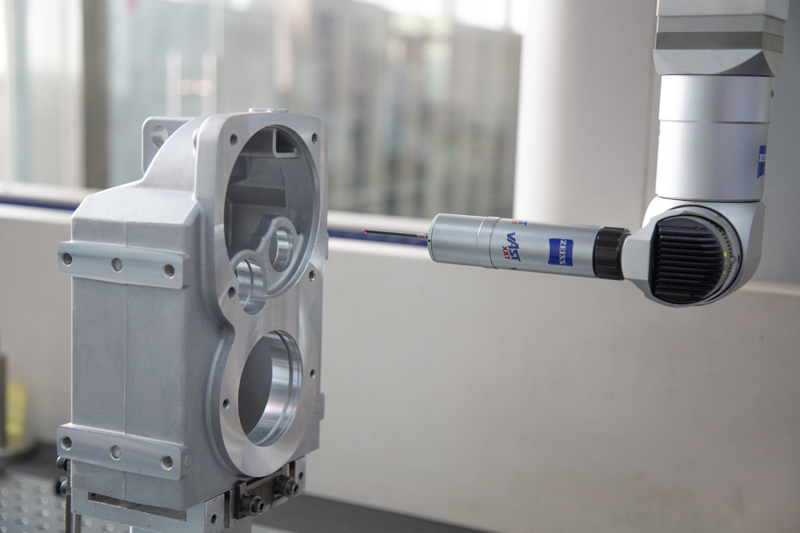
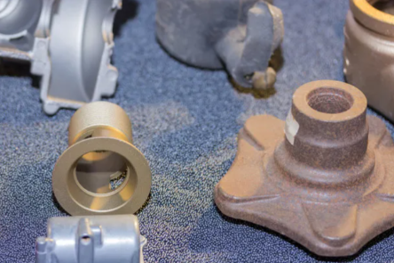
Shot blasting
Its principle is that the impeller body is driven by an electric motor to rotate. Under the action of centrifugal force, pellets with a diameter ranging from 0.2 to 3.0 (cast pellets, cut pellets, stainless steel pellets) are thrown onto the surface of the workpiece. This makes the surface of the workpiece reach a certain degree of roughness, making the workpiece more aesthetically pleasing. Or it can change the welding tensile stress of the workpiece into compressive stress, thereby increasing the service life of the workpiece.
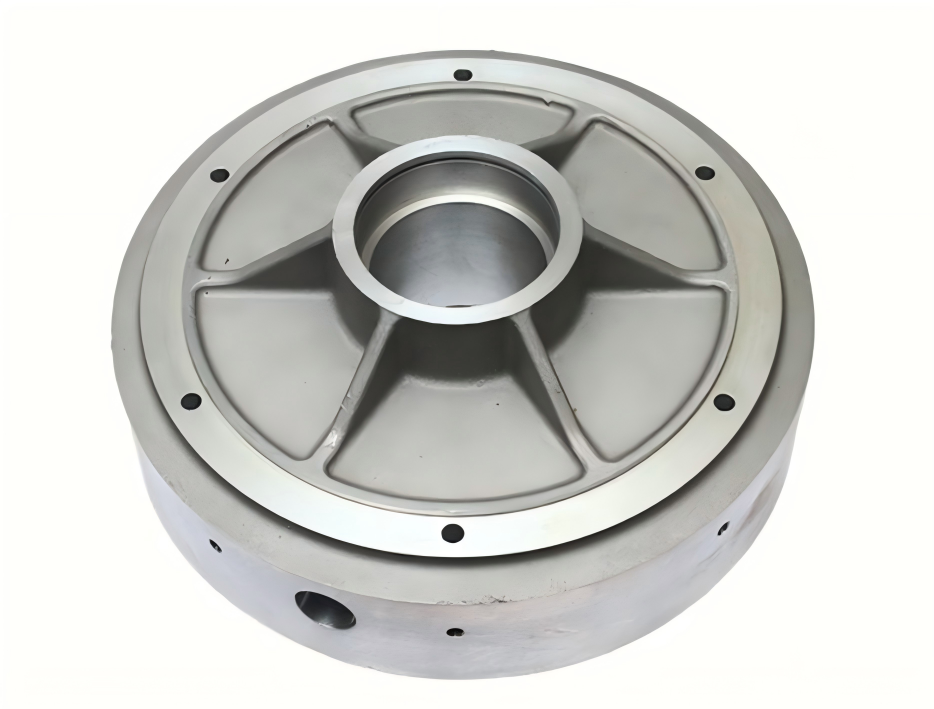
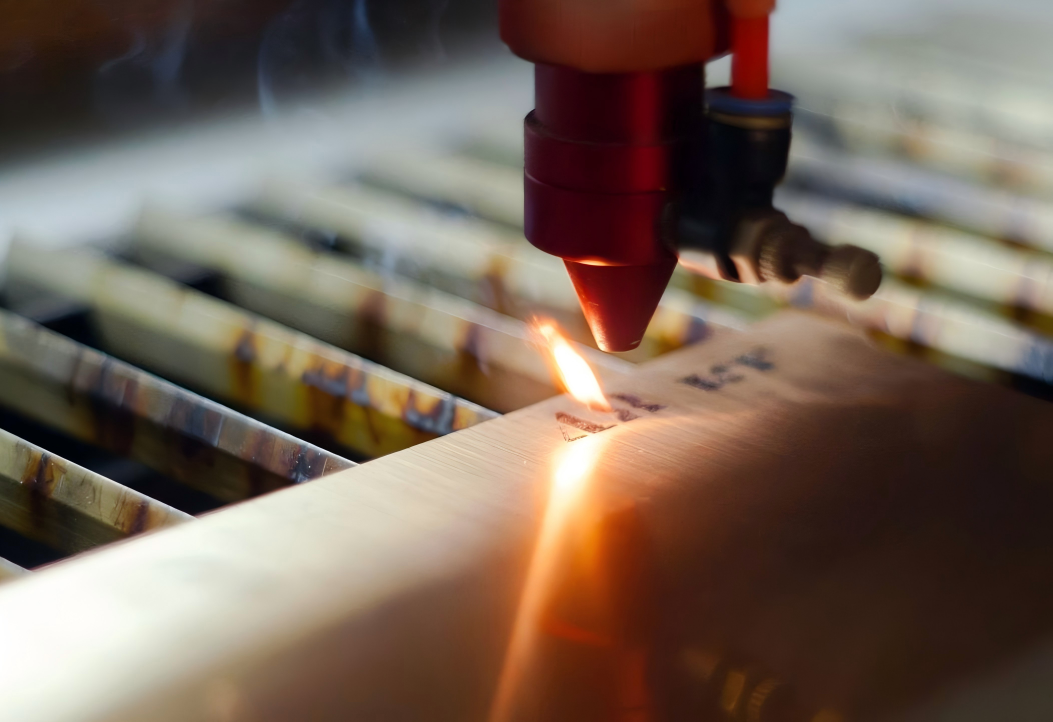
Laser Engraving
Laser engraving, also known as laser carving or laser marking, is a surface treatment process based on optical principles. It uses a laser beam to carve permanent marks on the surface of materials or inside transparent materials. For example, the fonts on the back cover of a watch are created using this process.
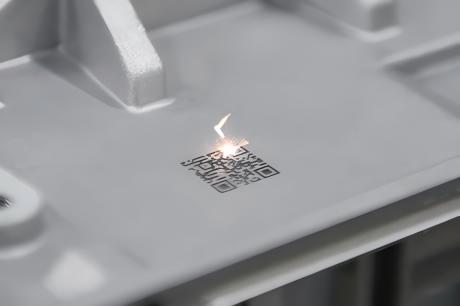
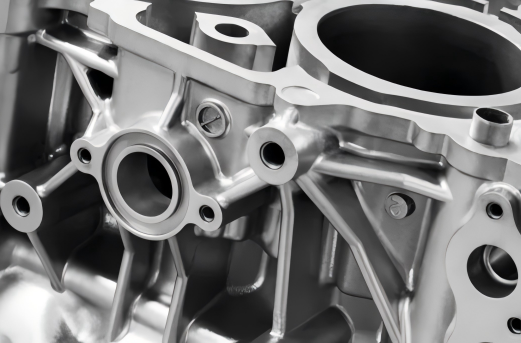
Sandblasting
Sandblasting is a process of cleaning and roughening the surface of the substrate by means of the impact of a high-speed sand flow. That is, compressed air is used as the power source to form a high-speed spraying beam, which sprays the blasting materials (copper ore sand, quartz sand, emery, iron sand) at high speed onto the surface of the workpiece to be processed, causing changes in the appearance or shape of the outer surface of the workpiece.
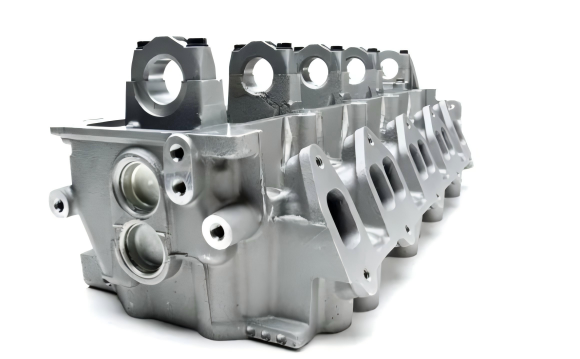
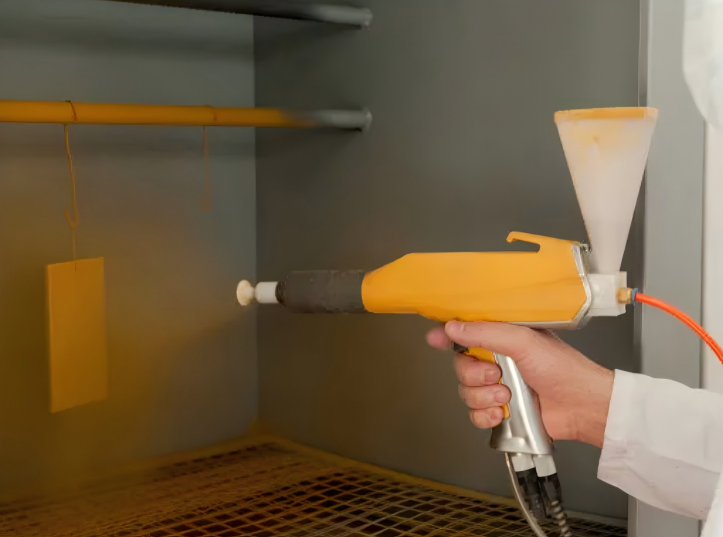
Powder Spraying
The powder spraying process is an efficient and environmentally friendly surface treatment technology. Powder coatings are evenly coated on the surface of die-cast parts through methods such as electrostatic adsorption or fluidized beds, and a dense coating is formed after high-temperature curing. It is suitable for outdoor equipment, automotive parts, etc.
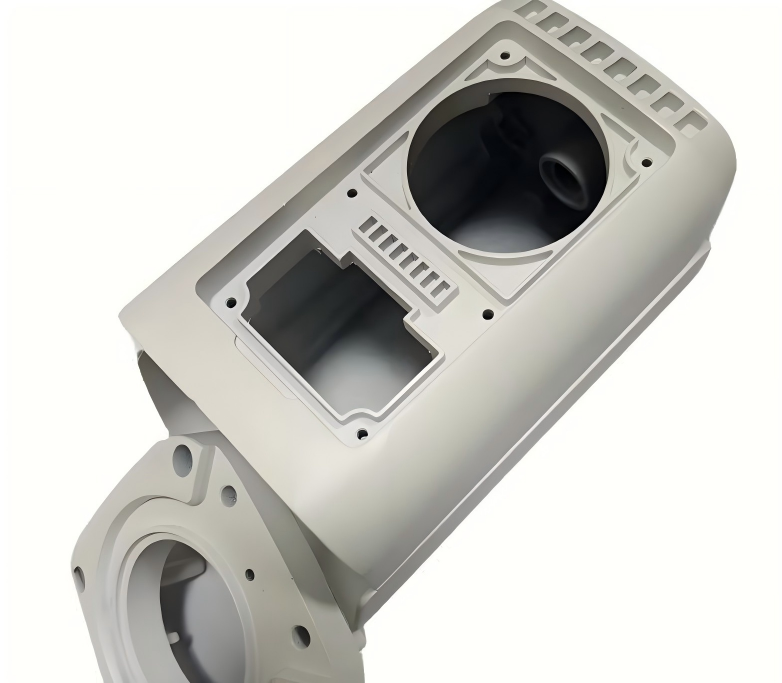
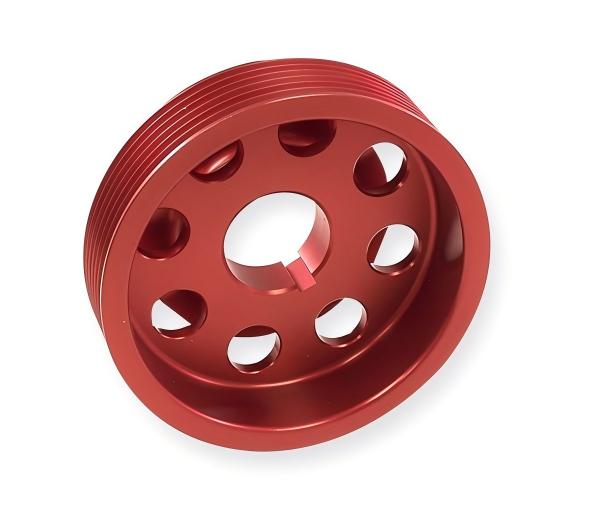
Painting
The painting process is a traditional process that achieves decoration and protection by covering the surface with liquid paint. Its core lies in the formation of a paint film through atomized spraying and the volatilization of the solvent. It is applicable to the casings of consumer electronics, decorative parts of toys, etc.
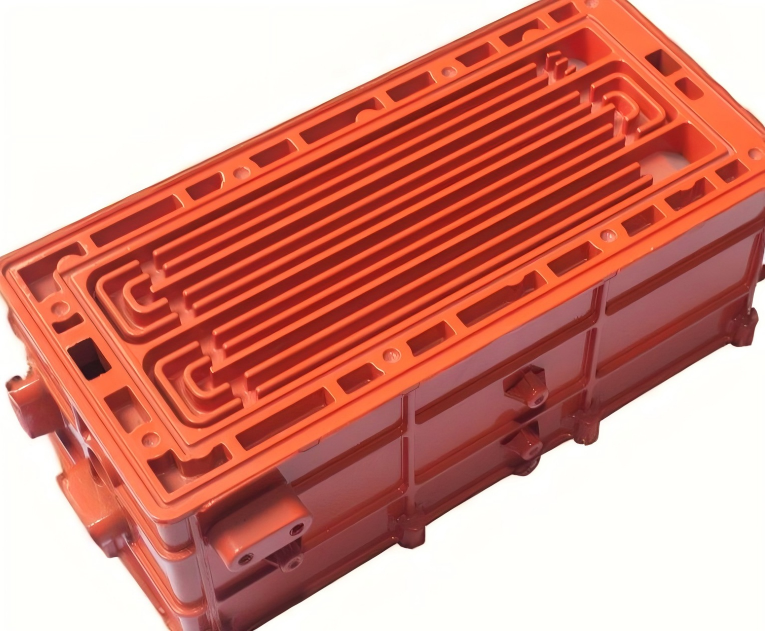
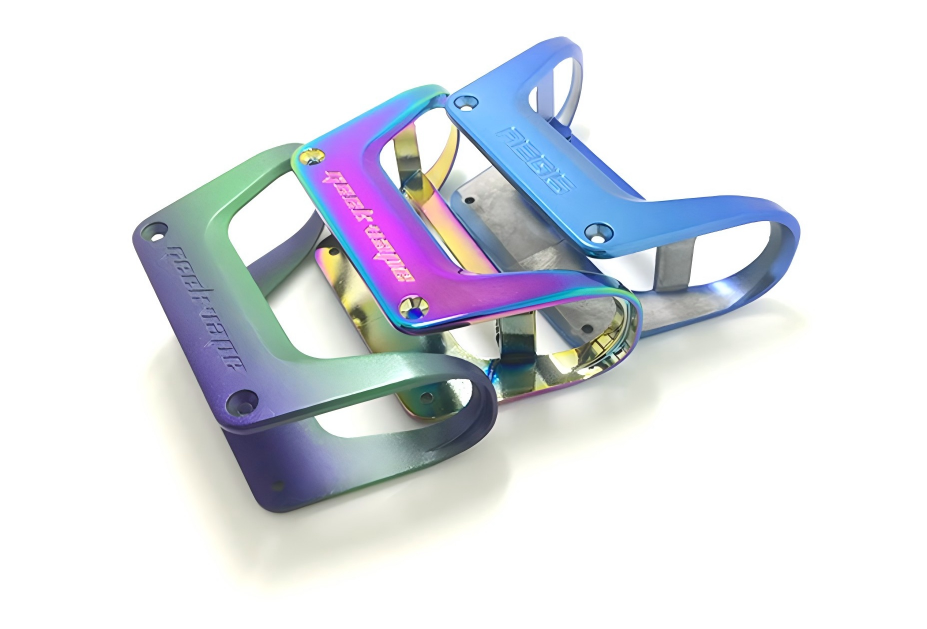
Electroplating
The electroplating process makes the surface of die-cast products more glossy and crystal clear. A corrosion-resistant coating is applied to the surface layer, thus increasing the service life of the parts. The electroplating process is divided into three types, namely rack plating, barrel plating, and vacuum plating. The products suitable for electroplating are mostly artworks, home decorations, leisure products, etc.
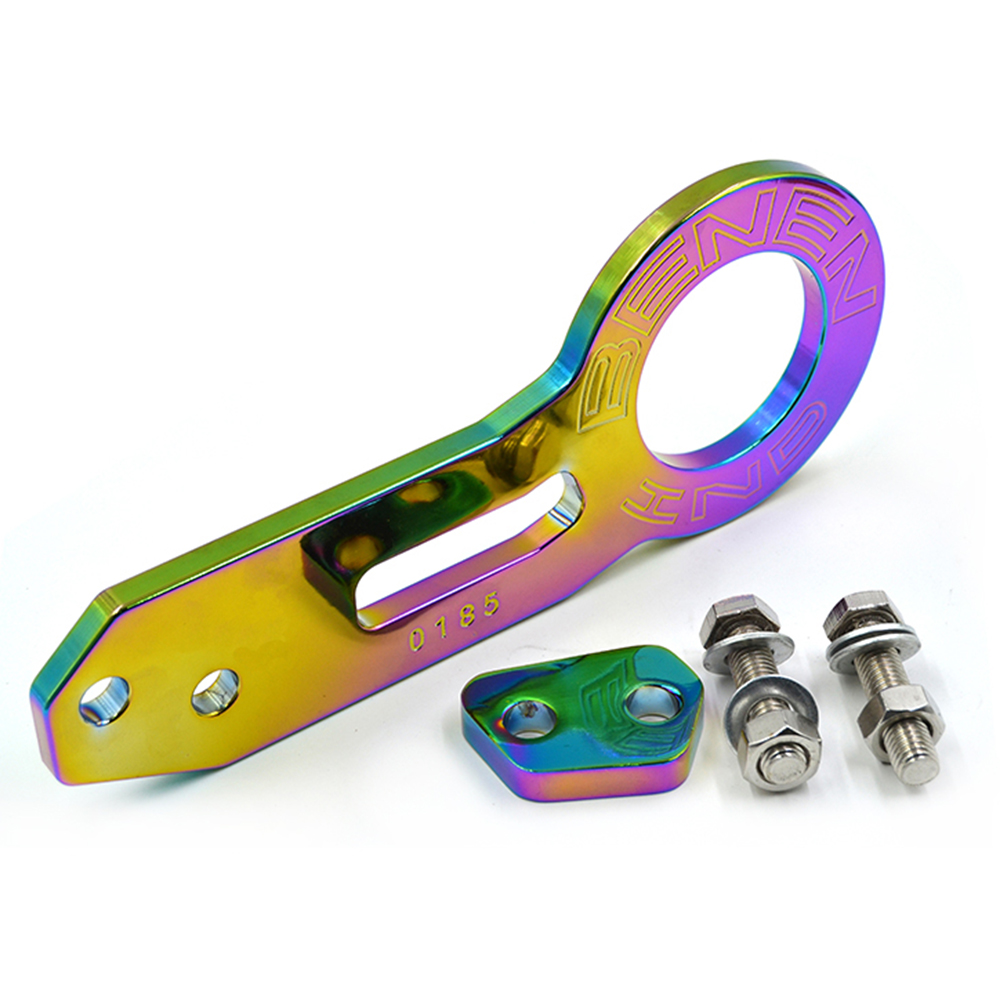
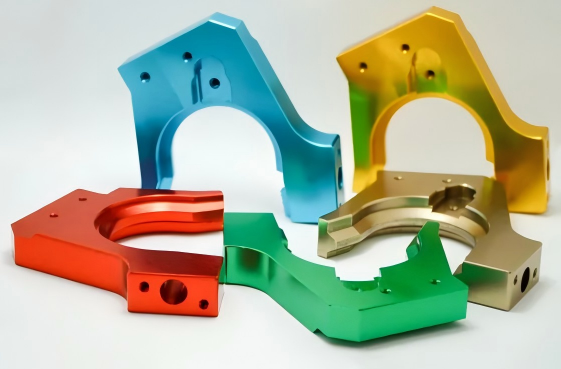
Anodizing
The anodizing process is a key technology for forming an oxide film on the surface of aluminum and aluminum alloys through an electrochemical method. It is mainly used to enhance the corrosion resistance, wear resistance, and decorative properties of the parts.
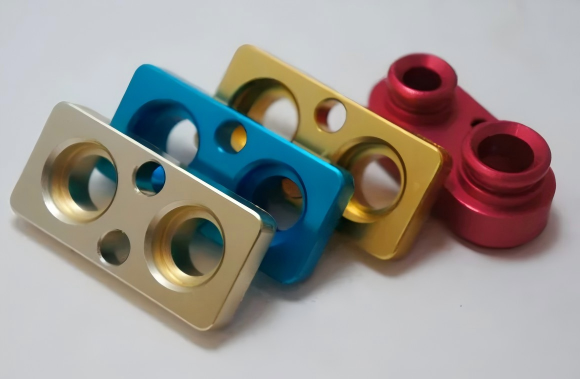
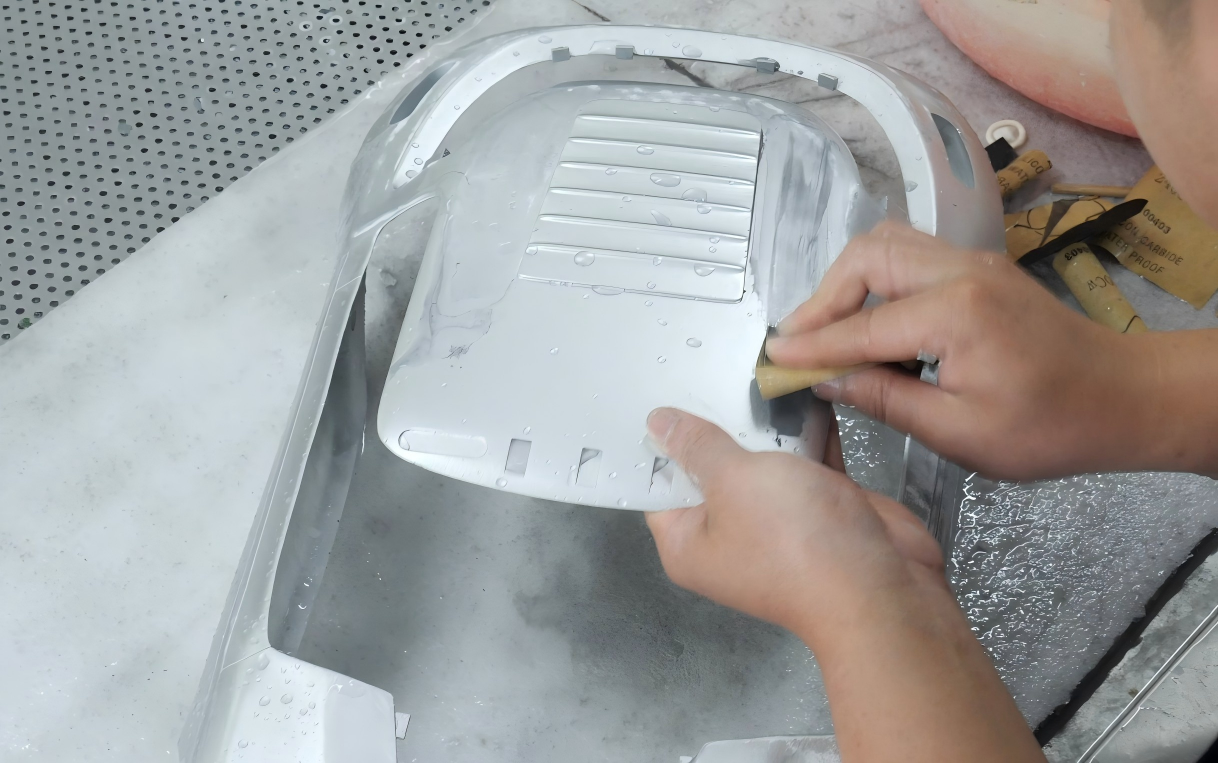
Grinding and Polishing
Polishing is divided into two types, namely mechanical polishing and chemical polishing. Mechanical polishing has good flatness and high gloss. Chemical polishing is fast in speed and has good anti-corrosion properties. It is suitable for workpieces with special and complex shapes, and can quickly improve the appearance brightness and corrosion resistance of die-cast parts.
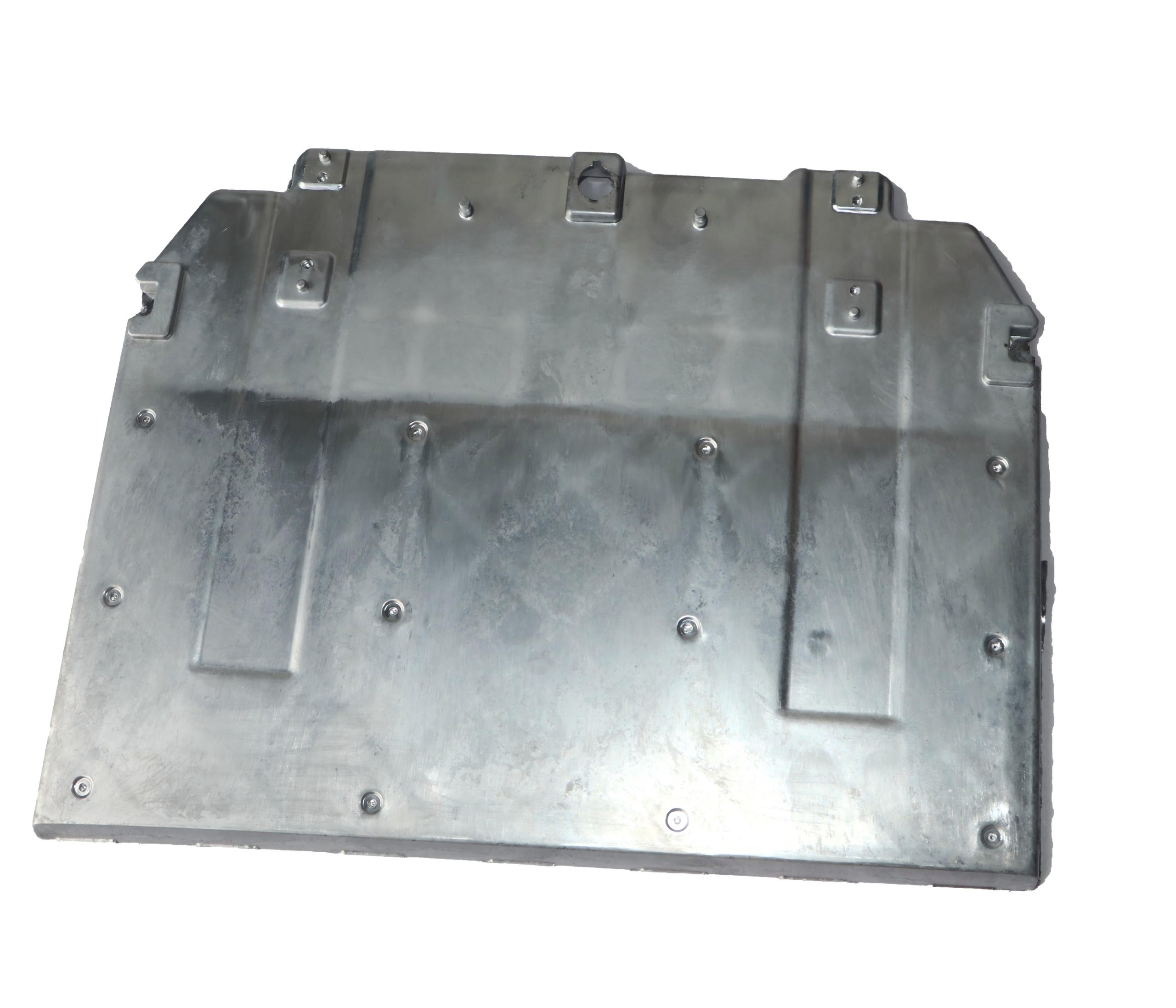