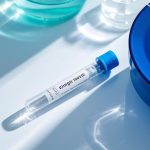
Medical Case, Virus Collection Tube
2024-10-19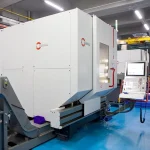
5-axis CNC machining center
2024-10-19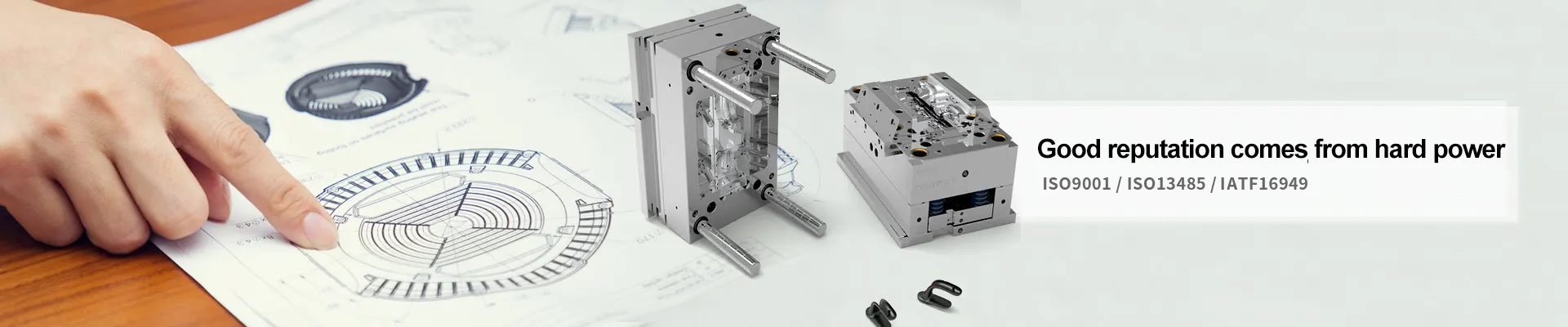
Stage Light Die-Cast Parts Customized
Z has been one of our important partners for many years. Z is a global, design and manufacturing company specializing in artistic lighting, and holds a leading position in its business field. This product is a major accessory in stage lighting and an important internal functional component.
Firstly, start with prototype design and structure verification then to undergo bath production. At soon as we received the drawing sheet from customers, we feel it was difficult to meet up the requirements in the aspect of accuracy. However, if we completely use CNC machining, the cost would be quite high and is hard for batch production.
The previous products first produced sheet metal parts through stamping molds, and the more than 20 spare parts on the handle had to be produced separately and then riveted and spot welded together. This approach was difficult to achieve the accuracy required by customers, had poor repeatability, high production costs, and sometimes failed strength tests.
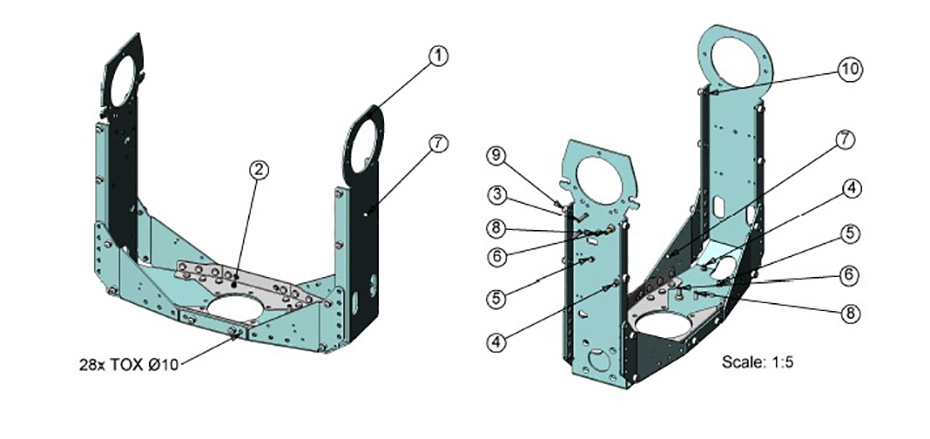
Thus, it is all team work. Our R&D team worked together with the customers to update the product structure. Now, the formation is done once with die-casting and then CNC machining high-precision parts, the production process is greatly simplified, the production cycle is shortened, and the production cost is reduced. While increasing the overall strength of the product, it can also meet the precision requirements of customers.
Via the experience from the first generation of product, customer provided us with detailed improvement of 2D drawing sheet for the prototype processing. Prototype works through CNC machnining, and the material we used is AL661 Aluminum alloy. HXC owsn the industrial leading 3-axis and German HERMLE 5-axis CNC machining, CNC machining can ensure the dimensional tolerance of the product and meet the accuracy requirements of customers. Five days later, we completed the prototype production.
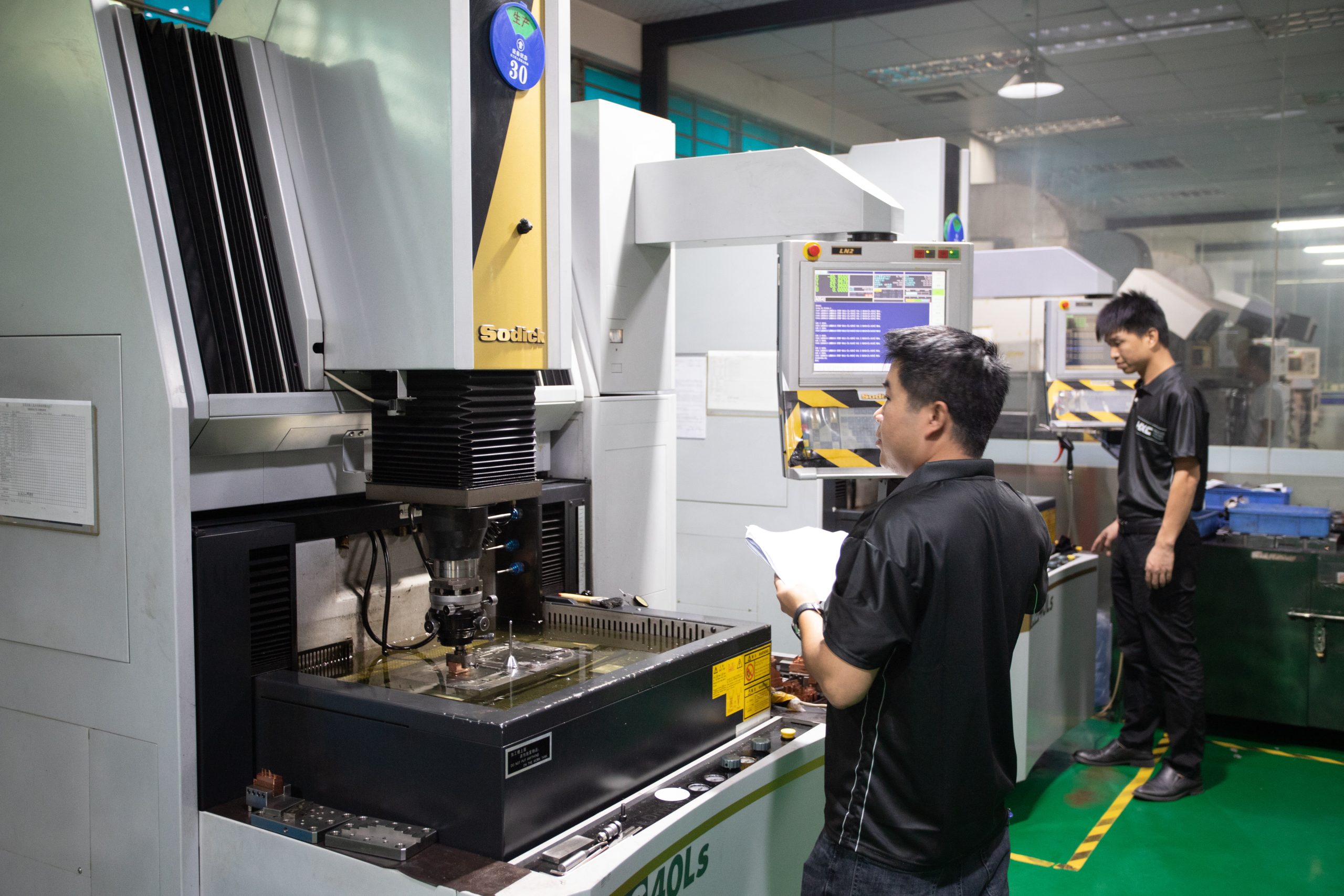
After delivering the prototype, the customer's design and functional requirements were verified, and then the drawings were modified to prepare for mass production. But if CNC machining is used for mass production, the production cost will be too high. After multiple studies and discussions, both parties decided to continue using the casting production process of the previous generation product and adjust the material to ADC12 cast aluminum for mass production.
HXC design team and production department have conducted multiple research and experiments, hoping to break through the production limitations of the previous generation of products by changing the production process to a one-time die-casting molding. The 20 parts on the product are molded in one go, and then all dimensional and positional tolerance requirements are completed through precision CNC machining. Through continuous efforts, we have achieved the expected design idea. However, this major reform has not been smooth sailing and has encountered some significant technological challenges.
Challenges and Solutions
To be successful in die casting by once, the mold design must be different from the last generation. However, we encountered technology difficulties during the design and experimental processes.
1.After we received the 2D drawing sheet for the new generation of product, we found that the tolerace requirement is extremely high. The tolerace of teh hole of the intermediate bearing installation can reach up to 0.008—0.033mm。In addition, the local material is thick and if we use common plan to inject, sand holes would occur in the middle. Based on many years of designing experience of our designing staff. In terms of mold design, a three-point fine water inlet scheme was designed to inject glue. Then, through model flow analysis, it was found that this solution is feasible and can achieve the desired effect
2.There is a significant risk with this product is that there is too much empty material at both ends, and the product length is relatively long, even the opening is too large, which can easily cause product deformation and fail to meet the customer's requirements for a length tolerance of ± 0.5mm and an assembly hole distance tolerance of ± 0.1mm between the two support legs. Later, we designed an auxiliary flow channel at this location, fixing the support feet on both sides. Later, we removed the auxiliary flow channel through CNC machining to avoid deformation and control the accuracy within the tolerance range required by the customer.
3.In the post-processing process, we also encountered difficulties. How can we ensure all dimensional accuracy in machining? After repeated research and discussion by the design and production personnel, a clever approach has finally come up with: during the machining process, the high demand bearing holes are first machined in place, then fixed in place, and then machined in other positions, ensuring the dimensional and positional accuracy of all positions.
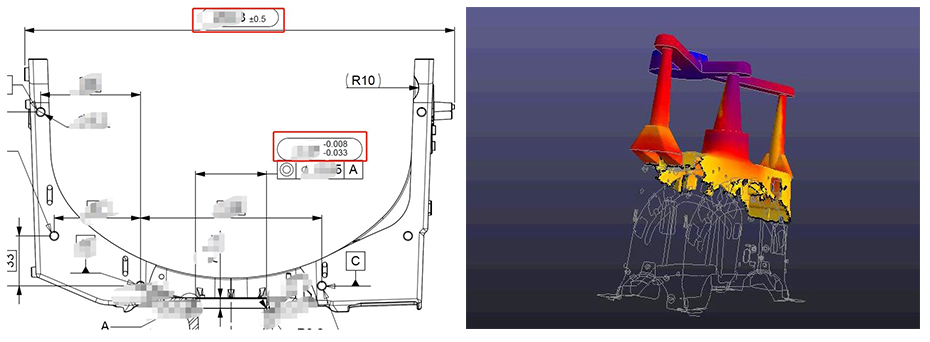
Mold design and manufacturing
After the plan is confirmed, to achieve the batch production, HXC stared on designing die cast mold.
After the plan is confirmed, the mold design will be easy. We completed the mold design, manufacturing, mold testnig and inspection in one month.
Batch production process steps
For batch production, the aluminum billet was put into the furnace and melt into the aluminum solution, then use the already made mold to press out the embryo of the product on the die-casting machine, then rinse off the slag around the product, and send it for polishing and grinding to trim the product burrs.
Start precise processing of parts with CNC workshop to meet high size requirement and more fine surface.
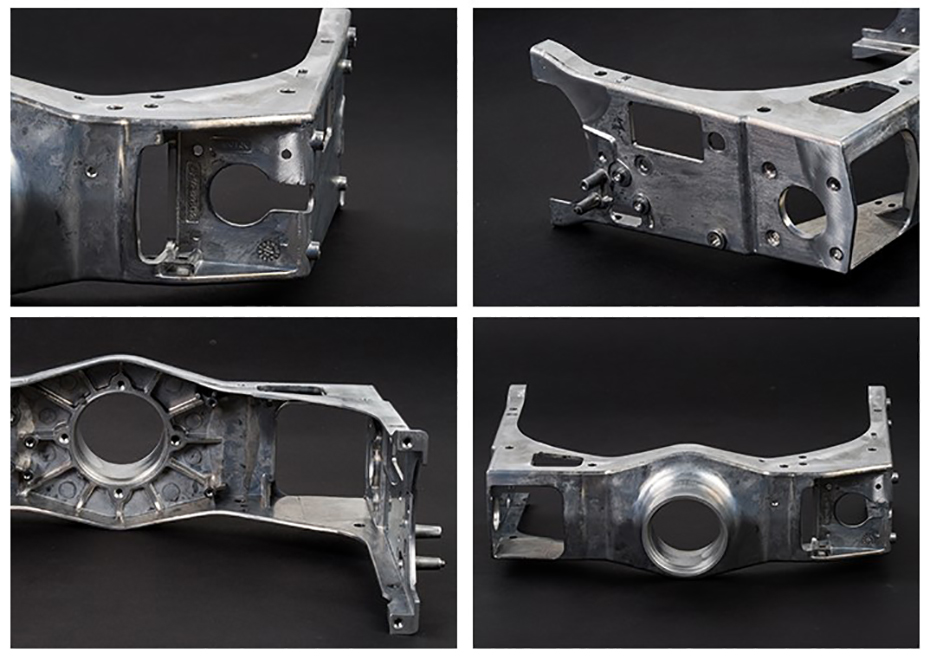
Fro products with surface requirement, the post-treatment will be carried out, like sand spraying, oxidation, powder coating, etc. As this product is an internal functional component, there are no high requirements for the surface of the product, so there is no need for fine surface treatment in the later stage.
Then, to conduct the size inspection to make sure it meet up the standards.
Customer Feedback
Customer was quite satisfied with our product. Project manager Steven said:'we have worked with HXC for many many years.They are our trusted partner and their R&D team is really impressive and a high level of craftsmanship. Every time we make prototypes, they will found problms in design and other potential problems that may arise in future mass production, which we can improve in a timely manner. This has saved us a lot of time and cost, and has helped us avoid many mistakes. We have been stayed in touch with HXC throughout the process. Having such a business partner, we feel very happy and relax.