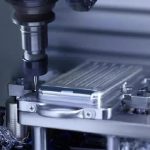
What exactly is the “CNC process” used in smart lock processing?
2025-03-27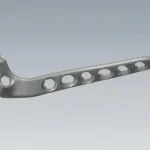
5-Axis CNC Machining of Medical Titanium Bone Plates (TC4) Case Study
2025-03-29Research on 5-axis CNC machining of vortex stainless steel impeller
Project Background
HXC Precision
HXC Precision received an order from an industrial equipment manufacturer to process a batch of stainless steel impellers for turbines. The impeller material is SUS316 stainless steel, which has excellent corrosion resistance and mechanical properties and is suitable for harsh industrial environments. However, the impeller has a complex geometry and extremely high requirements for accuracy and surface finish, which became an important challenge in processing.
Challenges
1. Material properties:
SUS316 stainless steel is prone to work hardening during processing, resulting in increased tool wear, which in turn affects processing efficiency and quality.
2. Geometric complexity:
The impeller has multiple curved surfaces and internal flow channel structures, and conventional three-axis or four-axis equipment cannot meet the processing requirements of its complex shapes.
3. High precision and surface quality requirements:
The geometry of the blades must be highly consistent to ensure the dynamic balance and operating efficiency of the turbine, and the blade surface requires extremely high finish to reduce air or fluid resistance.
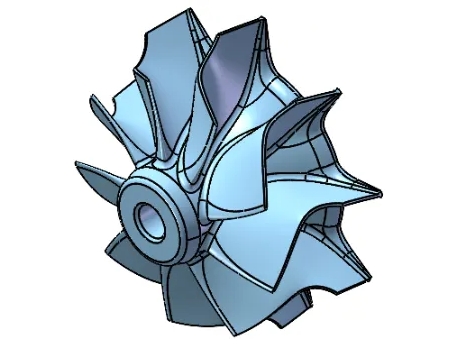
Solution
1. Equipment selection and process design
HXC Precision selected an advanced five-axis CNC machining center for processing. Five-axis machining can achieve multi-angle linkage processing of complex curved surfaces, reduce the number of clamping times, ensure accuracy and improve production efficiency. For complex flow channel areas, a partition processing strategy is adopted, combining rough processing and fine processing.
2. Tool and cutting parameter optimization
In order to cope with the hardening characteristics of SUS316 stainless steel, HXC Precision selected coated carbide tools and ceramic tools for high-strength cutting parts. Through experiments, the cutting parameters were optimized, and a lower feed speed and medium speed were used to reduce tool wear and thermal deformation of the workpiece. At the same time, an efficient coolant system was used to reduce the cutting temperature and prevent rapid tool wear.
3. Processing path optimization
Use advanced CAM software to simulate the impeller geometry in detail and plan the path to ensure that the idle travel is minimized during processing and to avoid sudden tool cuts that may cause tool wear or workpiece deformation. The processing path uses different feed methods in different areas of the blade to ensure the processing accuracy of each part.
4. Online measurement and quality control
During the processing, an online measurement system is used to monitor the thickness, curvature and key dimensions of the blades in real time through precision probes to ensure that compensation is adjusted at any time during the processing to avoid processing errors. The final impeller product is tested by a three-coordinate measuring machine (CMM) and a dynamic balancing machine
The dynamic balancing machine ensures that the error of all key dimensions is controlled within ±3mm and the imbalance is less than 0.1gmm.
5. Surface treatment
In order to meet the high requirements of turbines for the surface finish of the impeller, the impeller is also ultra-precision polished after processing, so that the surface roughness reaches within Ra 0.3, ensuring the best fluid dynamics performance at high speed.
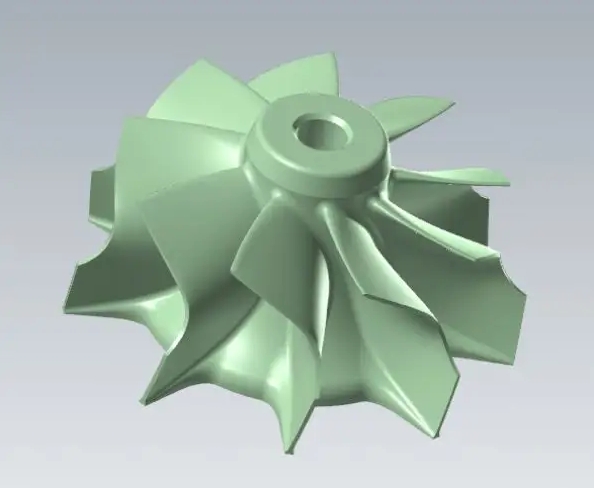
Solution
Precision and consistency:
The key dimensional accuracy of all impellers has reached the design standard, with the thinnest blade thickness of 0.9mm (height 28mm), the imbalance within 0.1gmm, and the error control within ±3 microns, ensuring the balance and efficient operation of the turbine.
Surface finish:
The surface finish of the impeller reaches Ra 0.3, which significantly improves the fluid mechanics efficiency and reduces the energy loss during operation.
Processing efficiency:
Thanks to the optimized tool selection and processing path, Yixin Precision has increased the processing efficiency by 20% and shortened the delivery cycle while ensuring quality.
Customer feedback:
The customer is very satisfied with the high precision and smooth surface of the impeller, and further established a long-term cooperative relationship with HXC Precision for subsequent high-performance parts production.
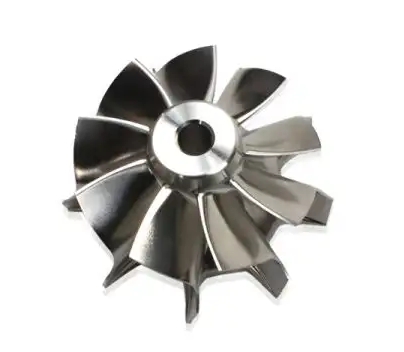
Summary
This case fully demonstrates the advantages of five-axis CNC machining technology in the processing of complex surfaces and high-demand parts. HXC Precision successfully solved the difficulties in stainless steel material processing through high-precision equipment, optimized process flow and rigorous quality control, and provided customers with high-quality turbine impeller products.