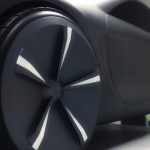
High-precision car model prototype
2025-04-09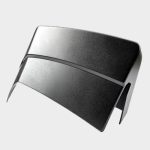
Automobile prototype processing case-housing parts
2025-04-14Silicone mold: save time and effort in small batch production
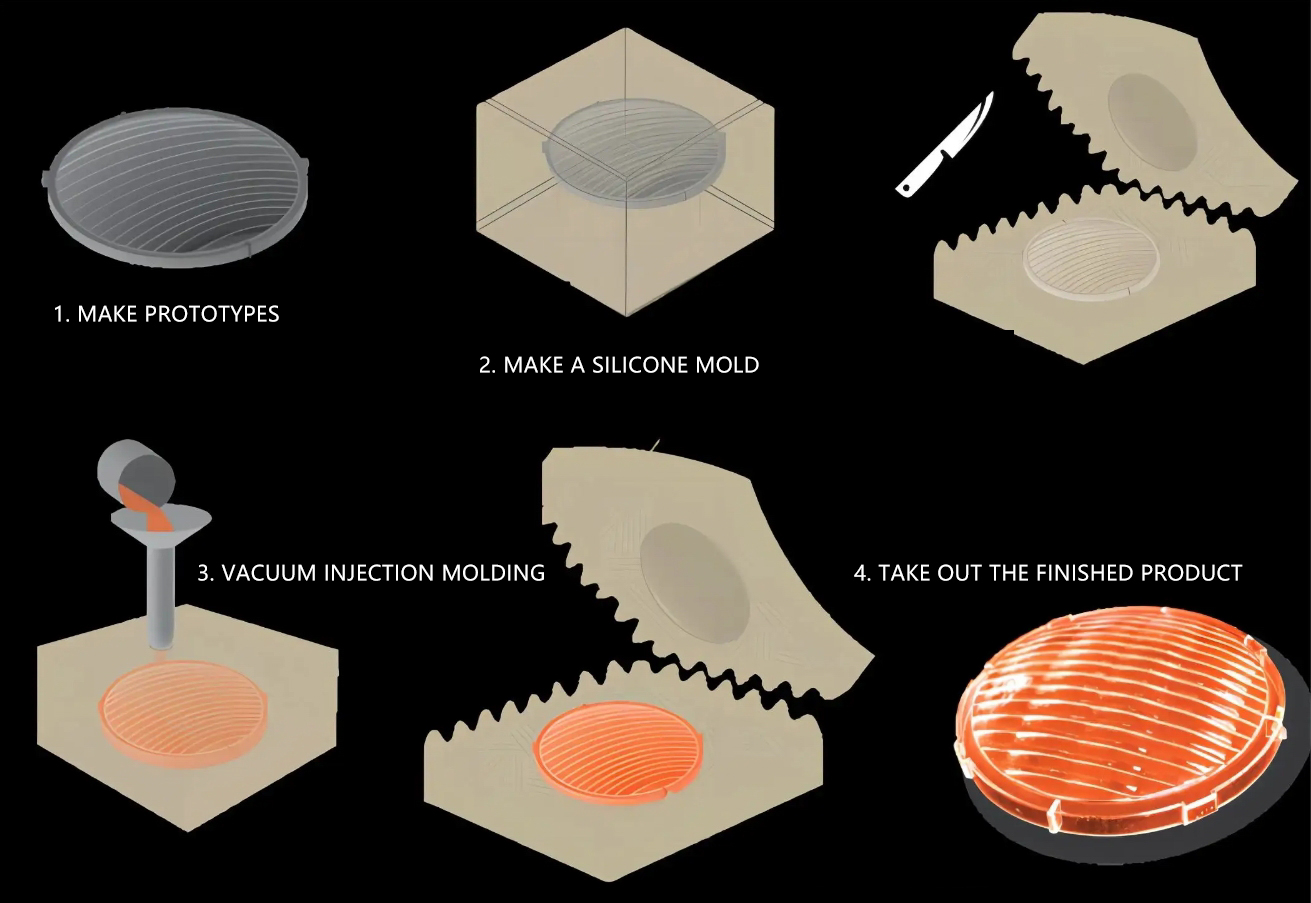
Silicone molding, also known as vacuum casting or vacuum molding, is a process performed in a vacuum environment. It involves degassing, stirring, preheating and molding the castable, followed by secondary curing in a constant temperature oven. In this way, the produced plastic parts can achieve strength and hardness requirements similar to those of raw materials such as ABS.
This process is mainly used in new product development and small batch production scenarios, because it can produce plastic parts with performance close to that of open mold injection products. In addition, silicone molds also allow color matching to meet diverse production needs according to customer needs.
1. Materials used
ABS, PP, PC, and soft rubber, etc.
2. Process advantages
Silicone molds are an ideal choice for small batches of high-quality plastic prototypes. They can not only quickly verify the feasibility of product design, but also help customers customize small batches of parts in the fastest and most economical way when the quantity demanded does not meet the requirements for opening steel molds.
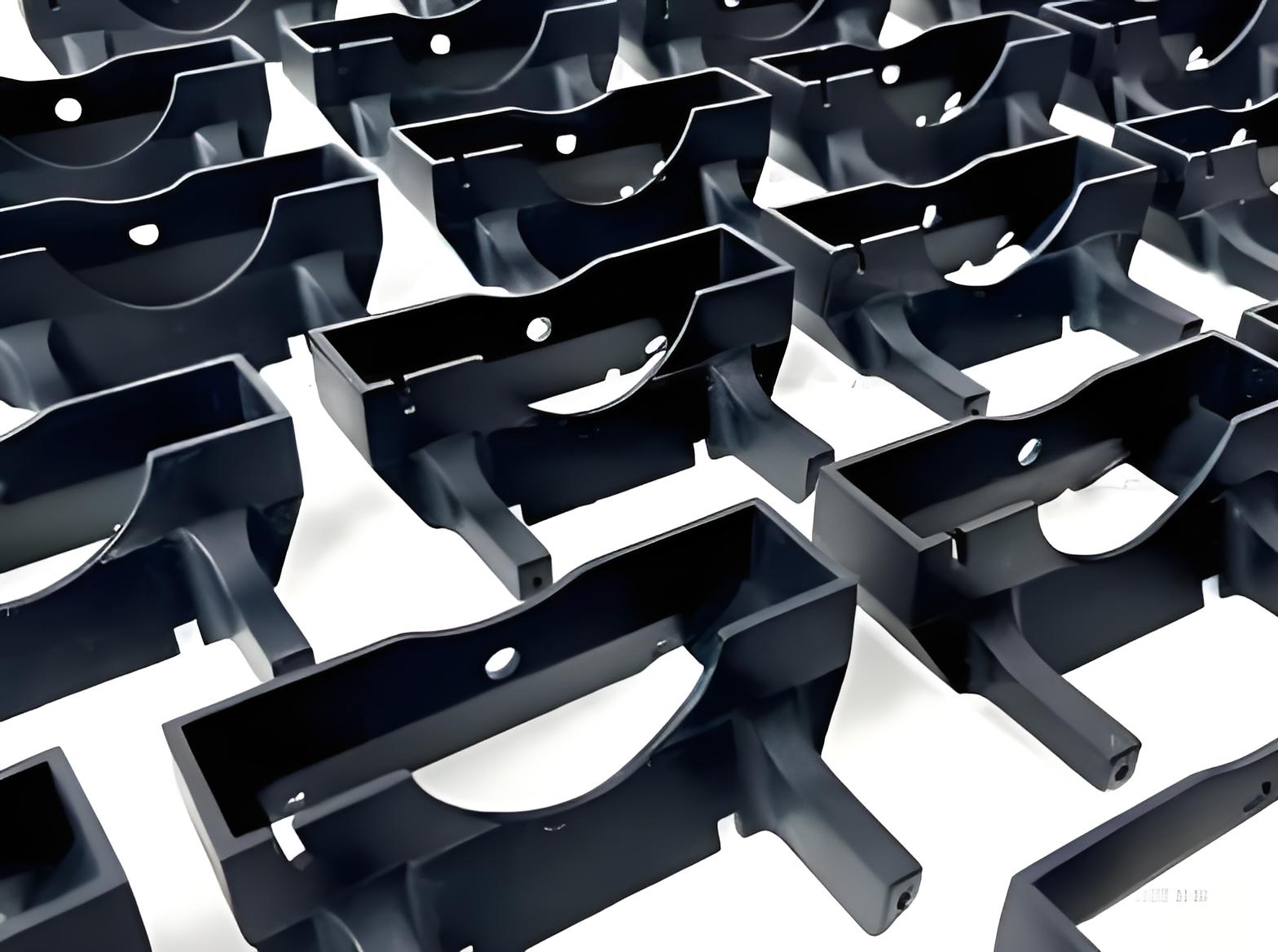
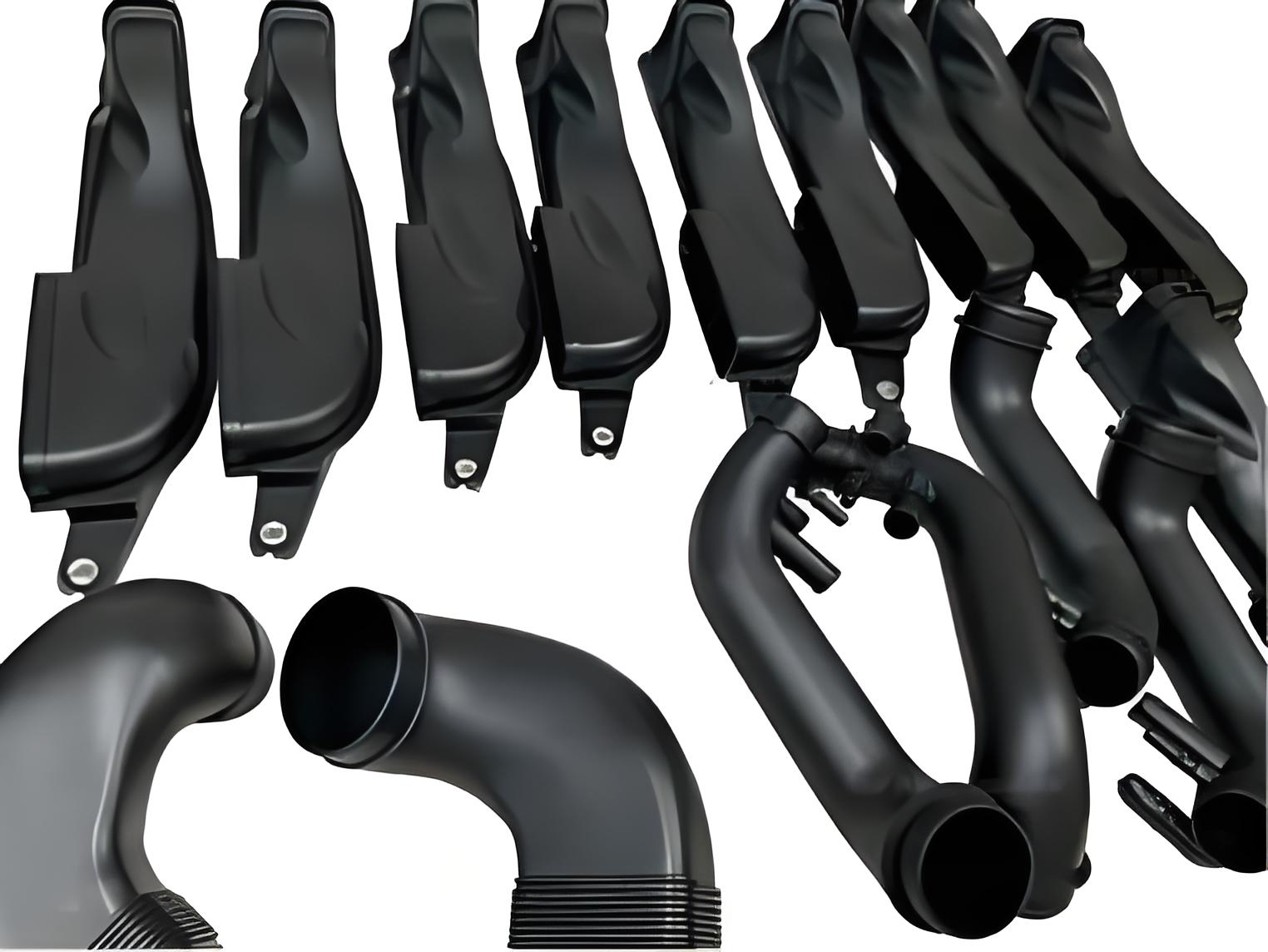
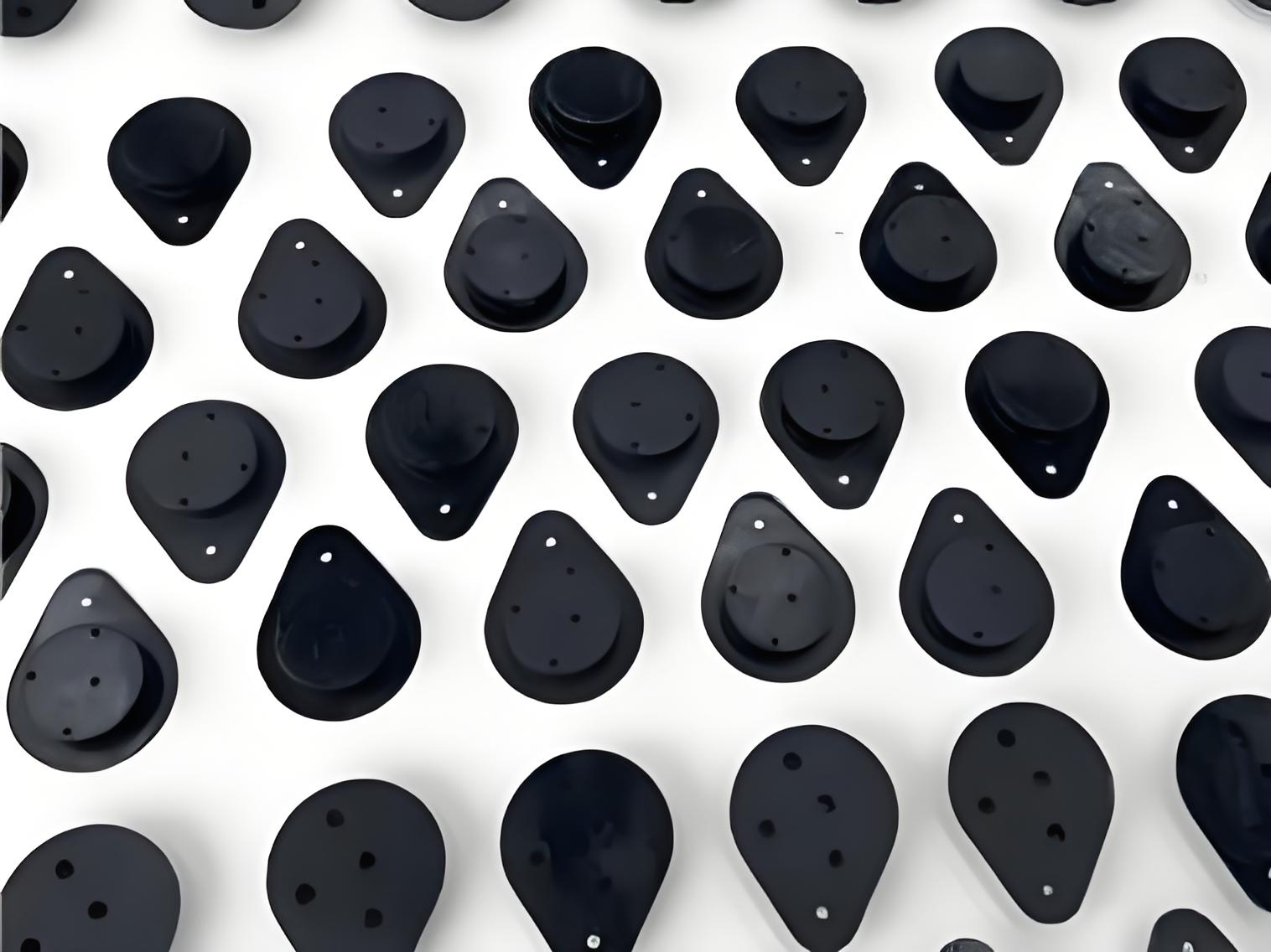
- a. Significantly shorten the product development cycle. By adopting the mold-reproduction technology, product prototypes can be quickly formed, thereby accelerating the testing and verification process. This not only saves valuable time resources, but also improves R&D efficiency, allowing products to be launched to the market earlier.
- b. Effectively reduce the cost of product development and manufacturing. Compared with traditional manufacturing methods, mold replication can reduce the consumption of raw materials and discover and correct potential problems in the early stages of product design, thus avoiding expensive modification costs in the later stages.
- c. It helps in design flexibility. By making a real product prototype, designers can more intuitively evaluate the appearance and performance of the product, and then make necessary adjustments and optimizations to the design. This not only improves the accuracy of the design, but also enhances the market competitiveness of the product.
- d. High degree of restoration and high product precision. The structure, details and texture of the prototype can be accurately replicated to provide high-quality and high-precision injection molded parts.
3. Process flow
Part 1: Prototype production
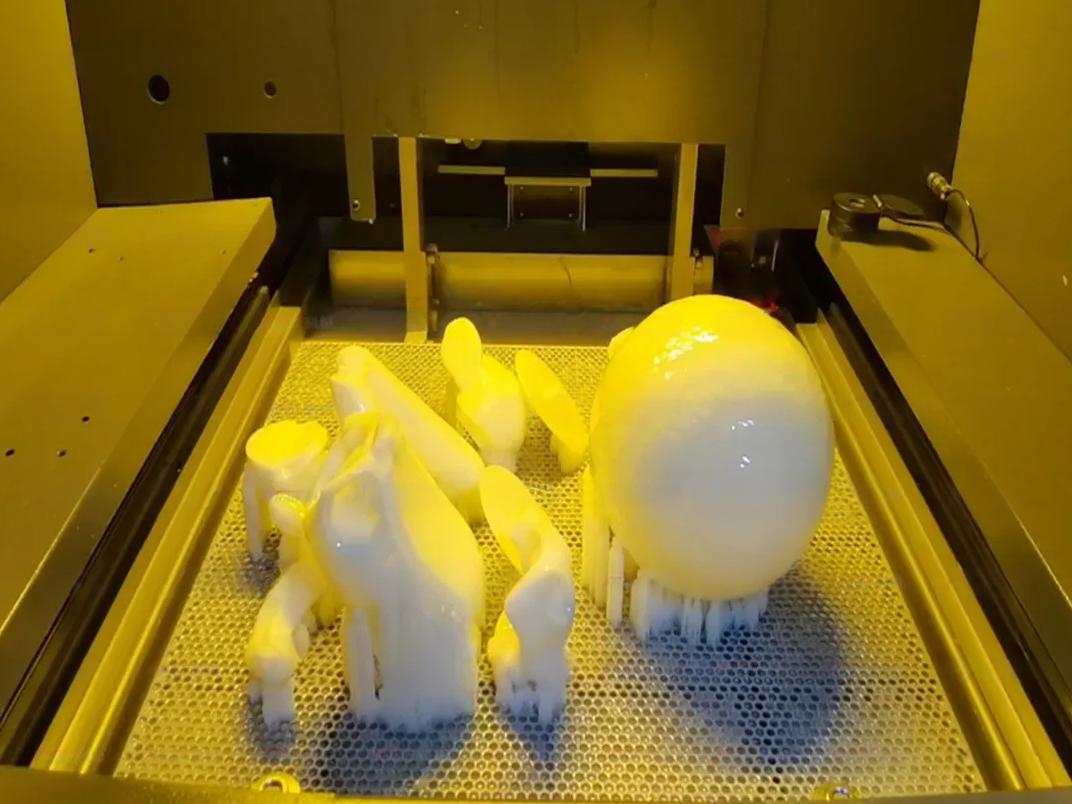
3D Printing Prototypes
Based on the provided 3D drawings, prototype parts are manufactured through 3D printing technologies such as SLA and DLP, which can retain complex shapes, structures and surface fineness to the greatest extent, greatly shorten the time from design to prototype, and enable designers and engineers to verify the feasibility of the design more quickly and make iterative improvements based on feedback.
Part 2: Making silicone mold
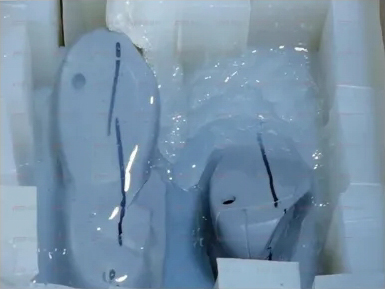
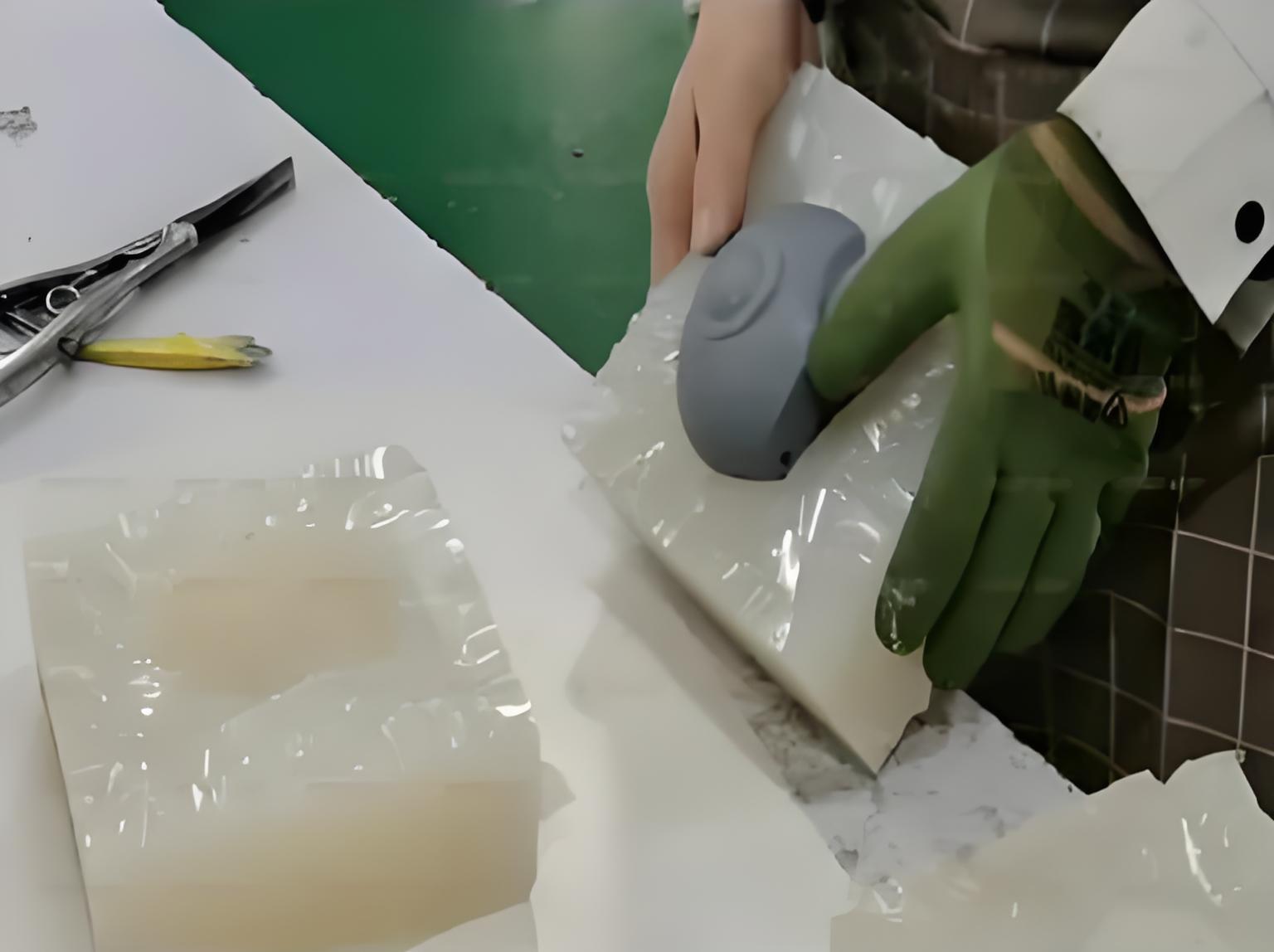
Silicone mold making
Molding and taking out 3D prototype
After the prototype is manufactured, the mold frame is made, the prototype is fixed, silicone is poured, and after waiting for drying, the prototype is removed to obtain the silicone mold, and the silicone mold manufacturing is completed.
NOTE: If the mold is large or intricate, you may need to proceed carefully and slowly. Wash the silicone mold, making sure the surface is clean. Trim or smooth the edges of the mold if necessary.
Part 3: Vacuum injection molding
Prepare appropriate casting materials such as resin, wax or concrete according to the needs of the product to be made, and slowly and evenly inject the casting materials into the silicone mold to ensure that the entire mold is filled. Wait for a certain amount of time for it to solidify or harden according to the requirements of the material. When the casting material is completely solidified, carefully remove the finished product from the silicone mold.
Note: After curing in a 60°-70° constant temperature box for 30-60 minutes, demoulding is possible. If necessary, secondary curing is performed in a 70°-80° constant temperature box for 2-3 hours. Under normal circumstances, the service life of silicone molds is 15-20 times.
4. Process application
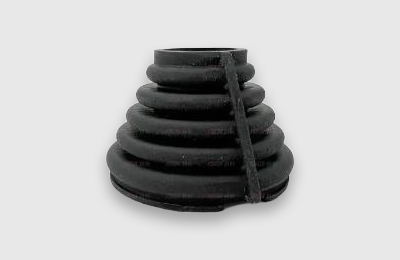
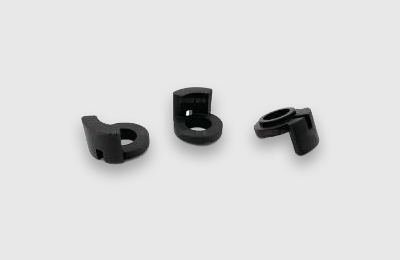
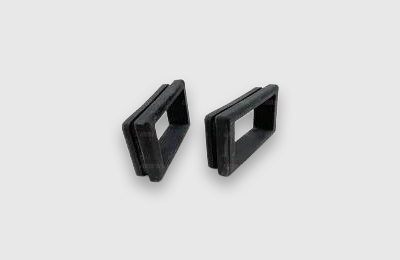
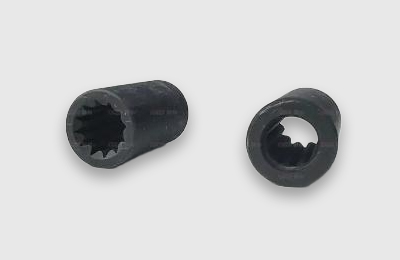
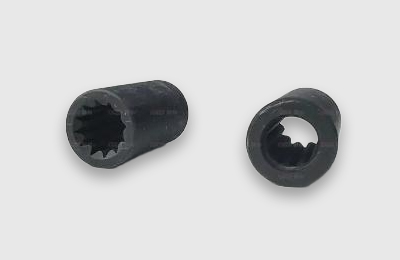
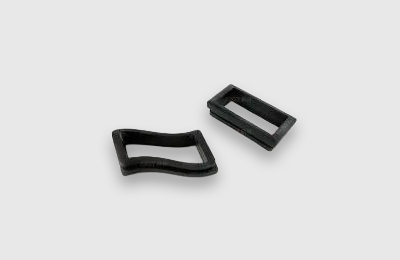
- a. Plastic prototype: Its raw material is plastic, mainly some plastic product prototypes, such as TVs, monitors, drones, hair dryers, etc. The most common photosensitive resin in 3D prototype proofing belongs to the plastic prototype category.
- b. Silicone mold prototype: Its raw material is silicone, and it is mainly used to display the appearance of product design, such as cars, mobile phones, toys, handicrafts, daily necessities, etc.