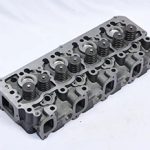
Development of contact ladle for automobile cylinder head
2025-03-20
Machining Case of the Whole HXC Unmanned Aerial Vehicle (UAV)
In an era of deep integration between artificial intelligence and aviation technology, unmanned aerial vehicles (UAVs) have transcended their roots as mere remotely operated devices, evolving into intelligent systems capable of autonomous decision-making. Whether navigating complex urban landscapes for 3D modeling or pinpointing fire risks in forest surveillance, UAVs are reshaping the frontiers of aerial operations through cutting-edge technological capabilities. At the forefront of this innovation, HXC empowers global UAV manufacturers with faster, more precise component solutions, driving accelerated progress across the industry. Specializing in end-to-end UAV production, HXC seamlessly handles every phase—from prototyping and design to large-scale manufacturing—ensuring efficiency and excellence at every step.
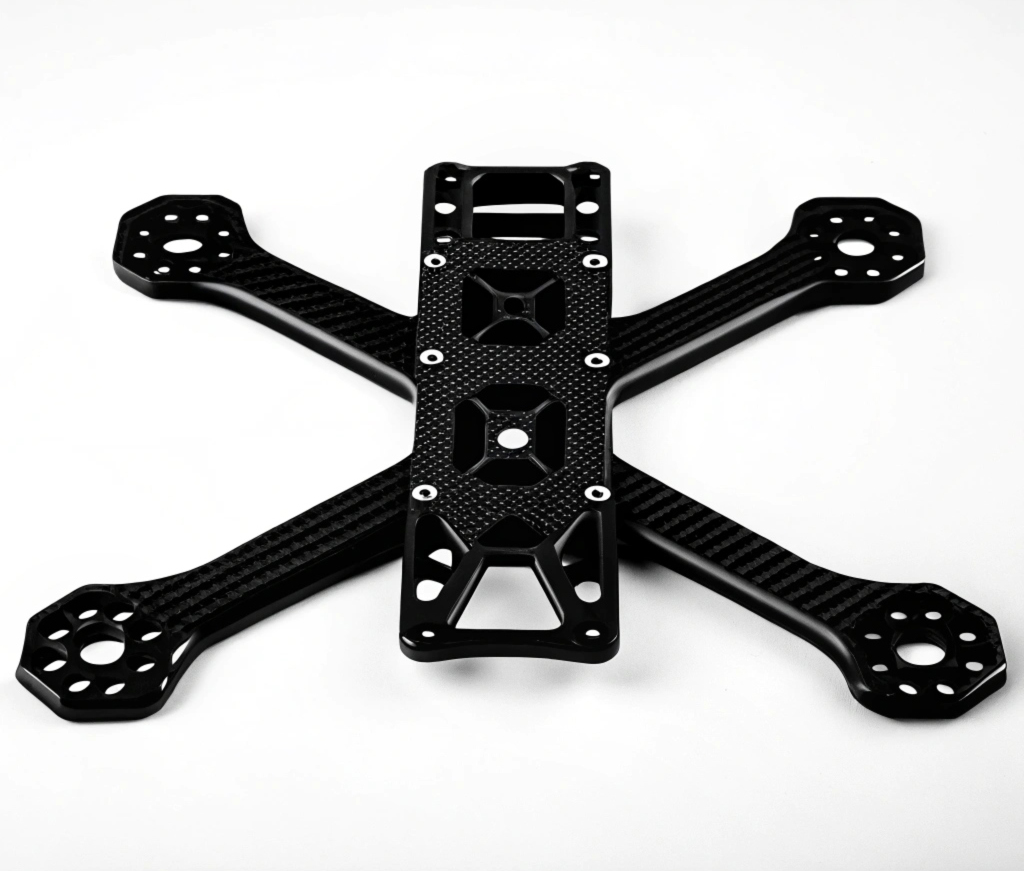
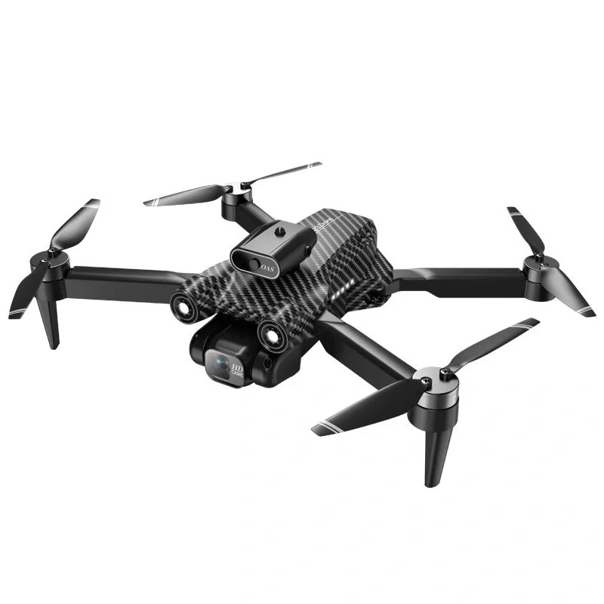
Advantages of Carbon Fiber in UAVs
Carbon fiber composites are widely adopted in UAV manufacturing due to their exceptional properties:
- High Strength-to-Weight Ratio: Carbon fiber offers superior strength and rigidity while being significantly lighter than traditional materials like steel or aluminum. the S900 (DJI S900) uses carbon fiber to achieve a lightweight yet robust structure, enabling longer flight times and higher payload capacities.
- Durability: The resistance of carbon fiber unmanned aerial vehicles (UAVs) to impacts and harsh environmental conditions ensures their reliability in challenging operational scenarios.
- Design Flexibility: The material’s malleability allows for intricate designs, such as the aerodynamic frames of racing drones or the integrated structures of industrial UAVs.
Exhibition of carbon fiber unmanned aerial vehicle (UAV) parts
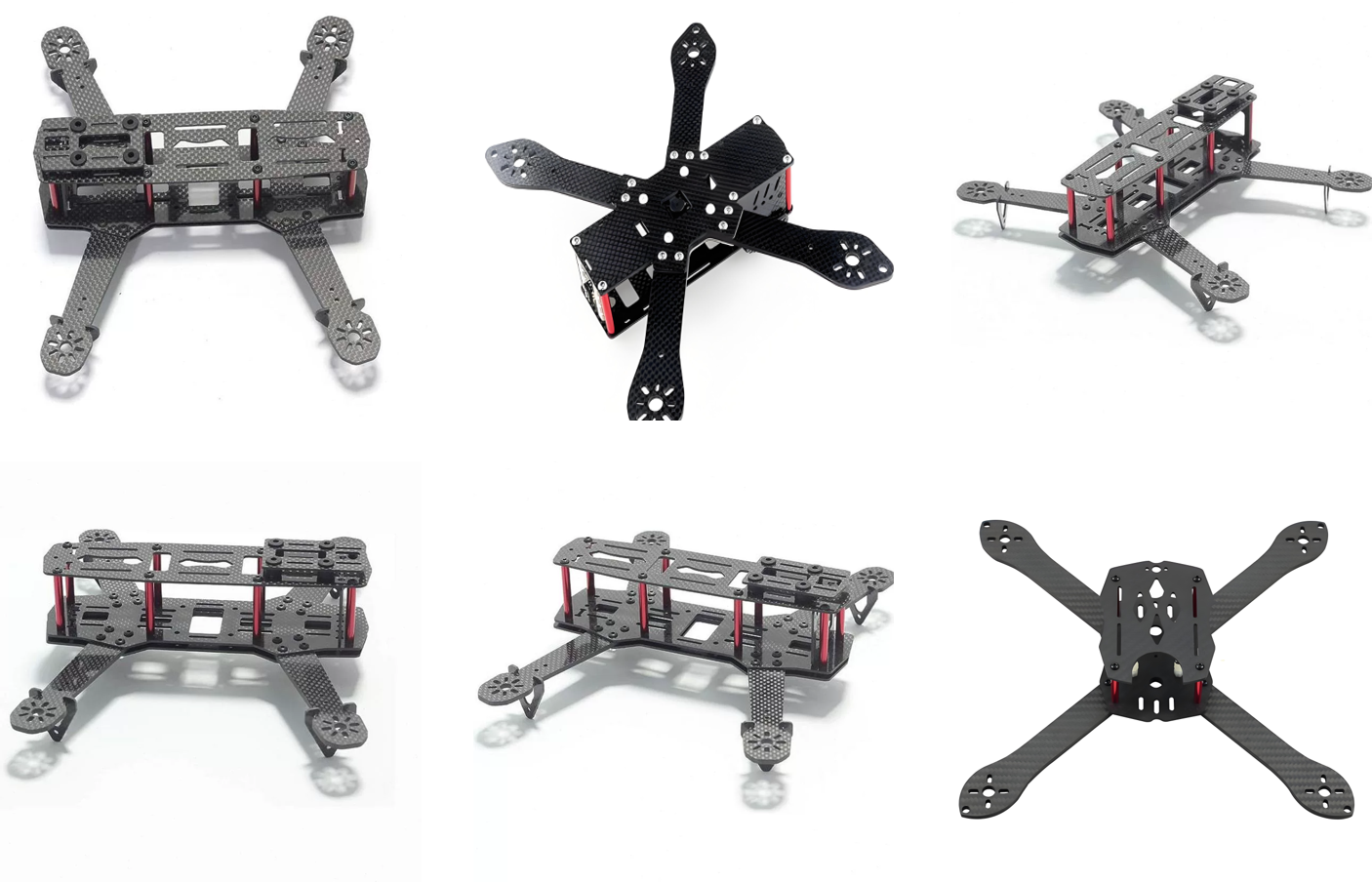
CNC Prototype Machining for Unmanned Aerial Vehicles (UAVs)
CNC machining technology has emerged as a pivotal technique in the fabrication of UAV components. The progress of computer - numerical - control (CNC) machining has instigated a paradigm shift in UAV design concepts. Component design is trending towards greater integration and intricacy. HXC Precision is capable of delivering prototype samples in as little as 48 hours for the prototyping of diverse UAV components
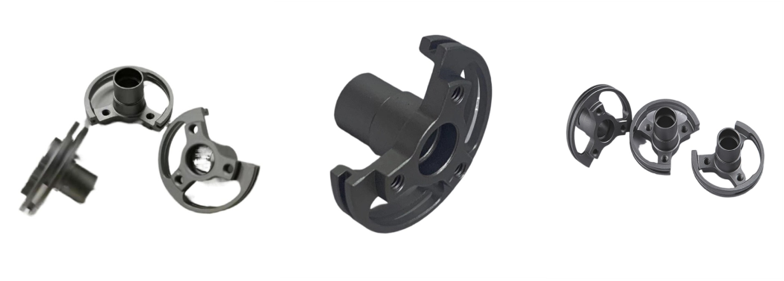
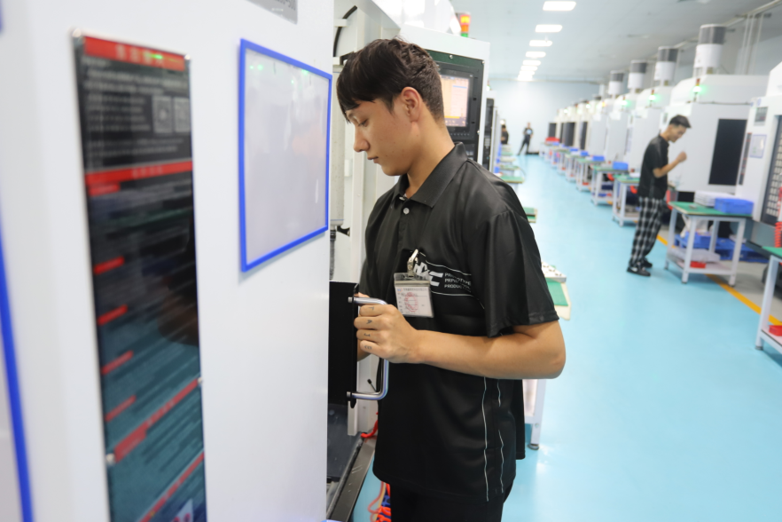
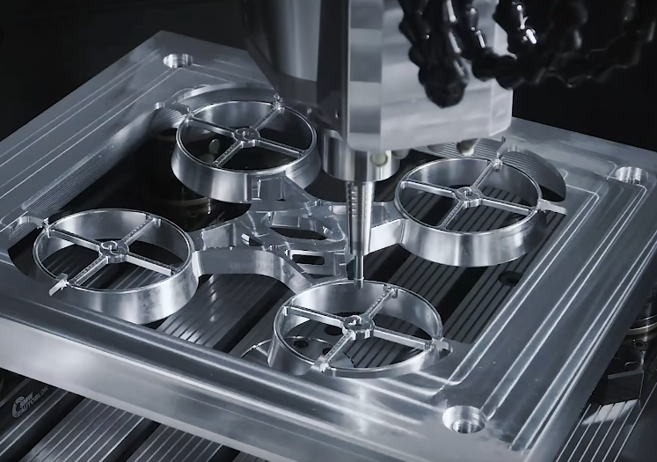
5-axis machining of UAV parts
Through high precision, high flexibility, and high efficiency, 5-axis machining technology has become a key process in the manufacturing of UAV parts, meeting the requirements of complex designs, lightweight structures, and stringent performance standards
Advantages of 5-axis Machining for Unmanned Aerial Vehicle (UAV) Parts
High-precision Machining
Through the multi-axis linkage in 5-axis machining, it is possible to complete the machining of complex curved surfaces, inclined surfaces, and structures with multiple features in one go. This reduces the accumulation of errors caused by traditional multi-process clamping. It is especially suitable for the high-precision requirements of UAV parts, ensuring the dimensional consistency and performance stability of the parts.
Adaptability to Complex Shapes
The cutting tools in 5-axis machining can flexibly adjust their angles in five degrees of freedom. They can easily handle complex geometries that are difficult to machine with traditional 3-axis machine tools, enhancing the freedom of part design.
Lightweight Optimization
5-axis machining can precisely control the amount of material removed, enabling the design of more complex lightweight structures. While ensuring the strength of the parts, it can significantly reduce the weight, which is crucial for the endurance and payload efficiency of UAVs.
Improving Material Utilization Rate
For expensive materials such as carbon fiber and titanium alloy, 5-axis machining can reduce the generation of waste materials by optimizing the tool path, improve the material utilization rate, and lower the manufacturing cost.
Enhancing Production Efficiency
A 5-axis machine tool can complete the machining of multiple surfaces in a single clamping, reducing the turnover and waiting time between processes. It is particularly suitable for the rapid production of small-batch and high-precision UAV parts, shortening the delivery cycle.
Integrated Manufacturing
5-axis machining can achieve full-process coverage from rough machining to finishing machining, reducing the transfer of parts between different pieces of equipment, lowering the risk of human intervention, and improving the overall machining efficiency and quality stability.
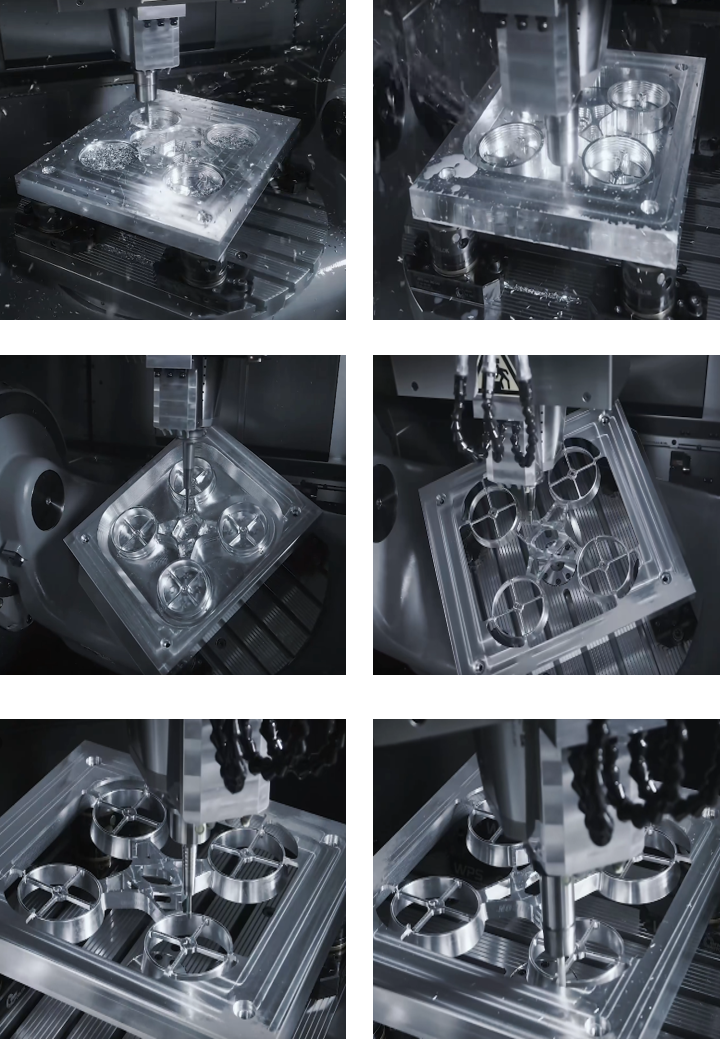
Exhibition of Core Parts of Unmanned Aerial Vehicles (UAVs)
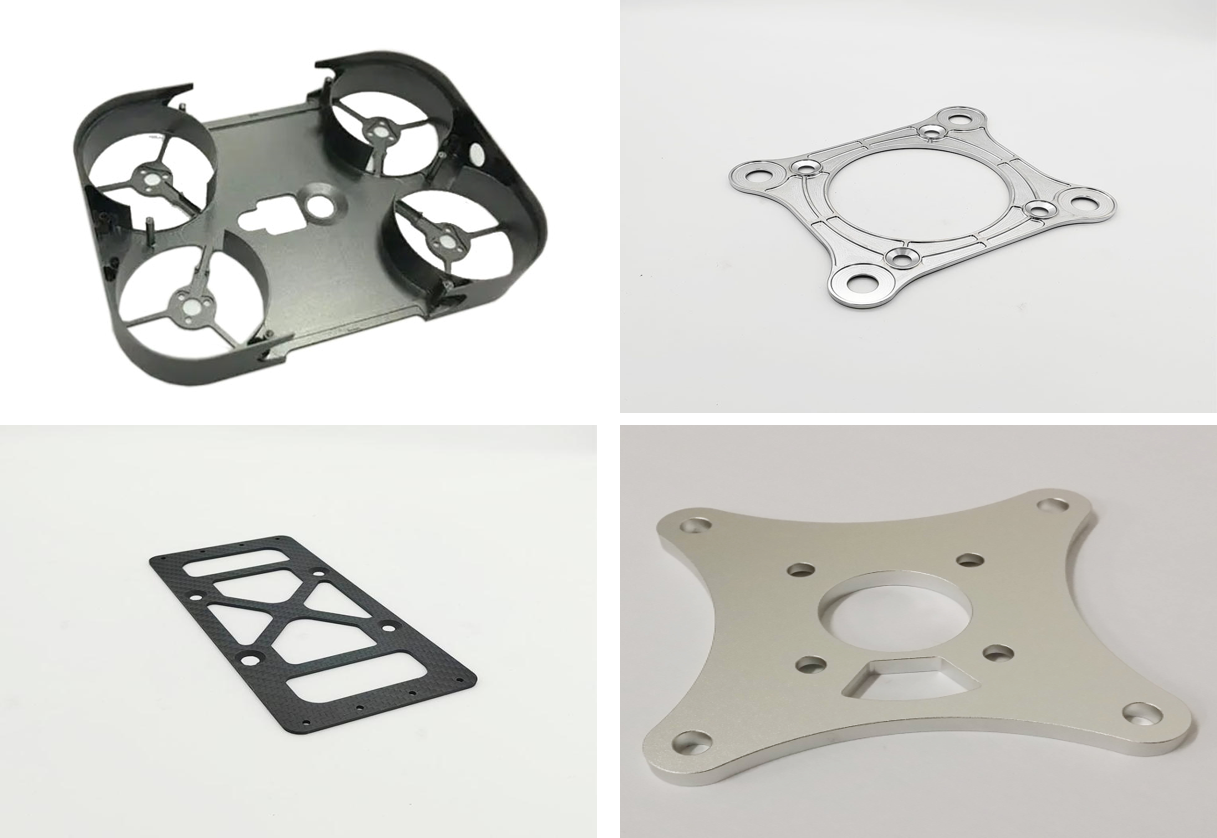
Exhibition of Unmanned Aerial Vehicle (UAV) Propellers
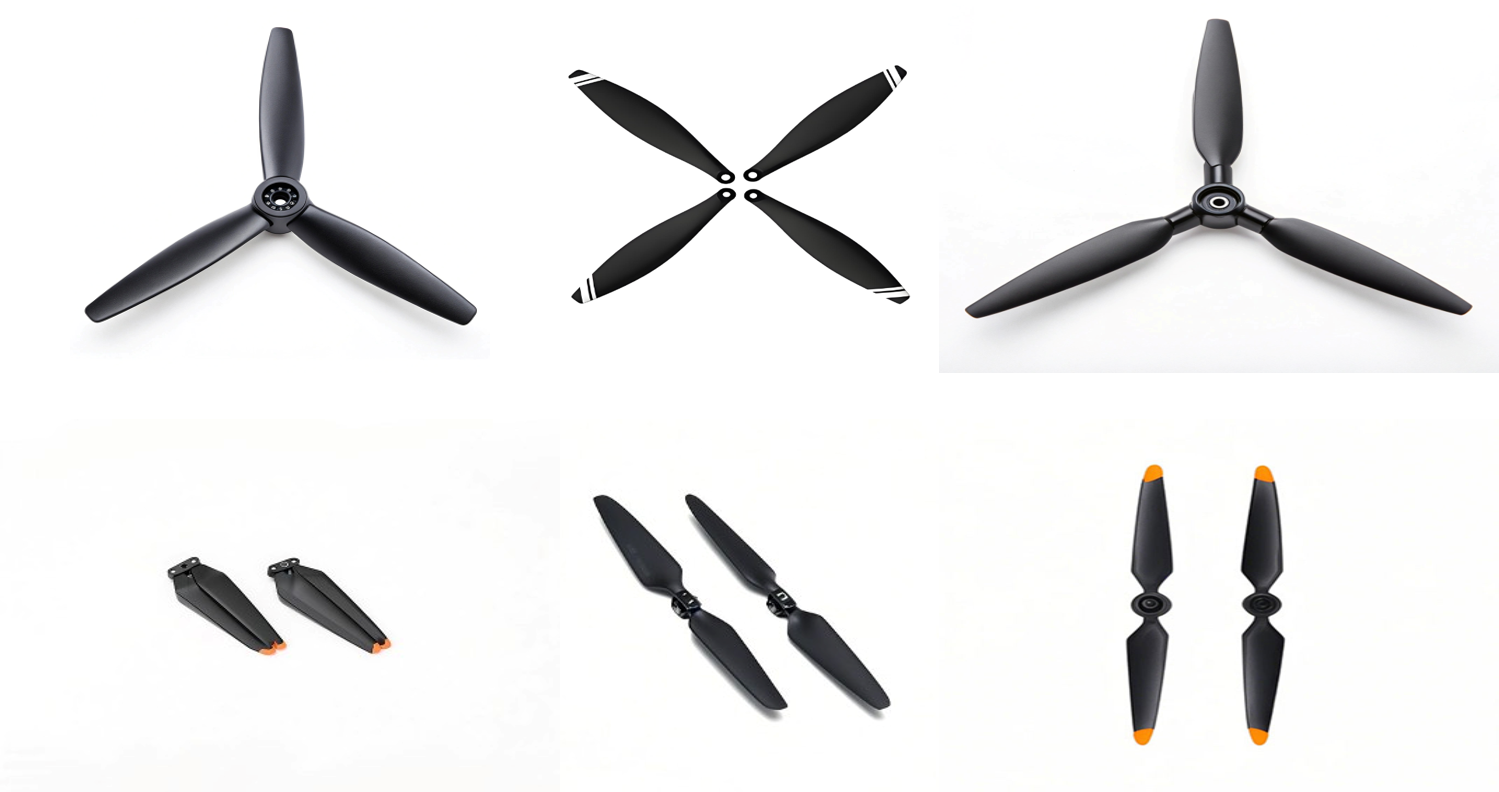
Exhibition of Parts of UAV Supporting Equipment
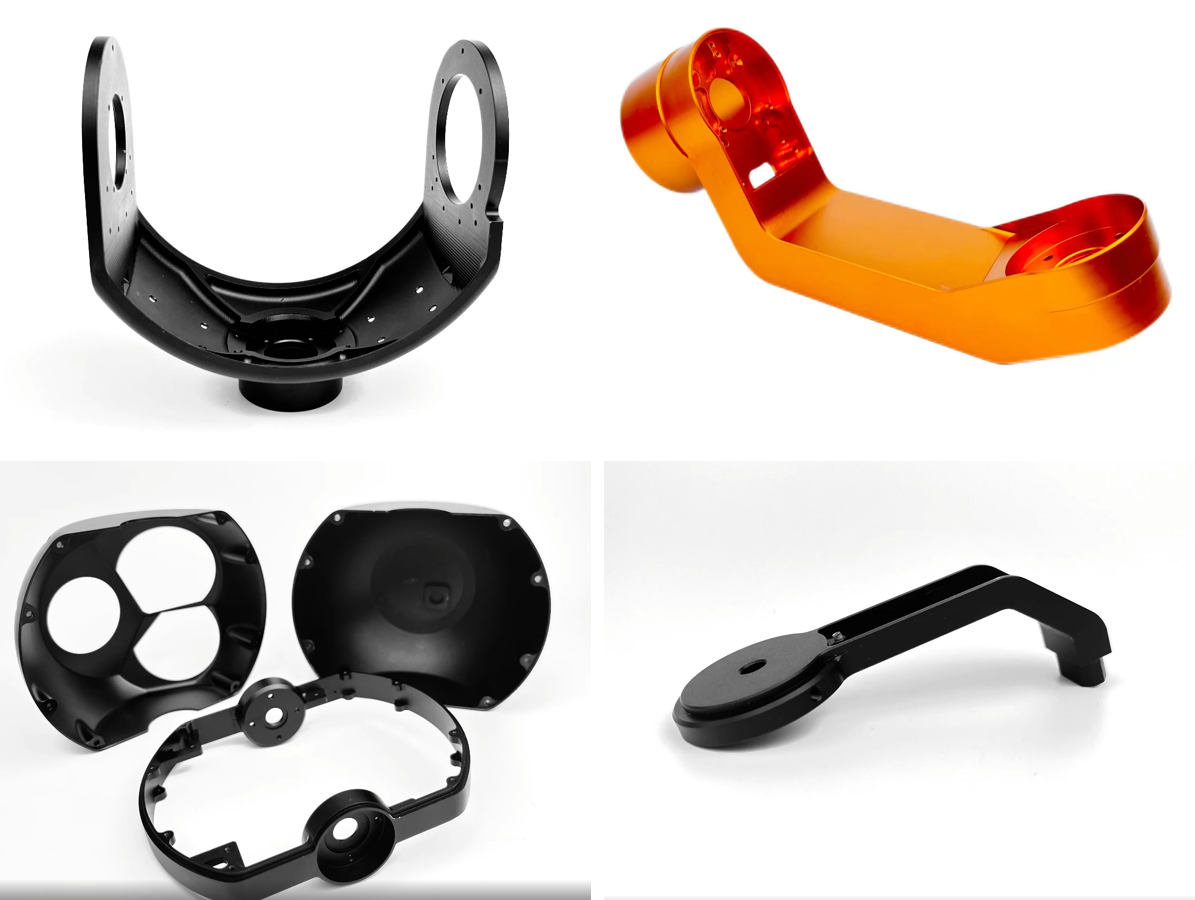
Exhibition of UAV Camera Assemblies
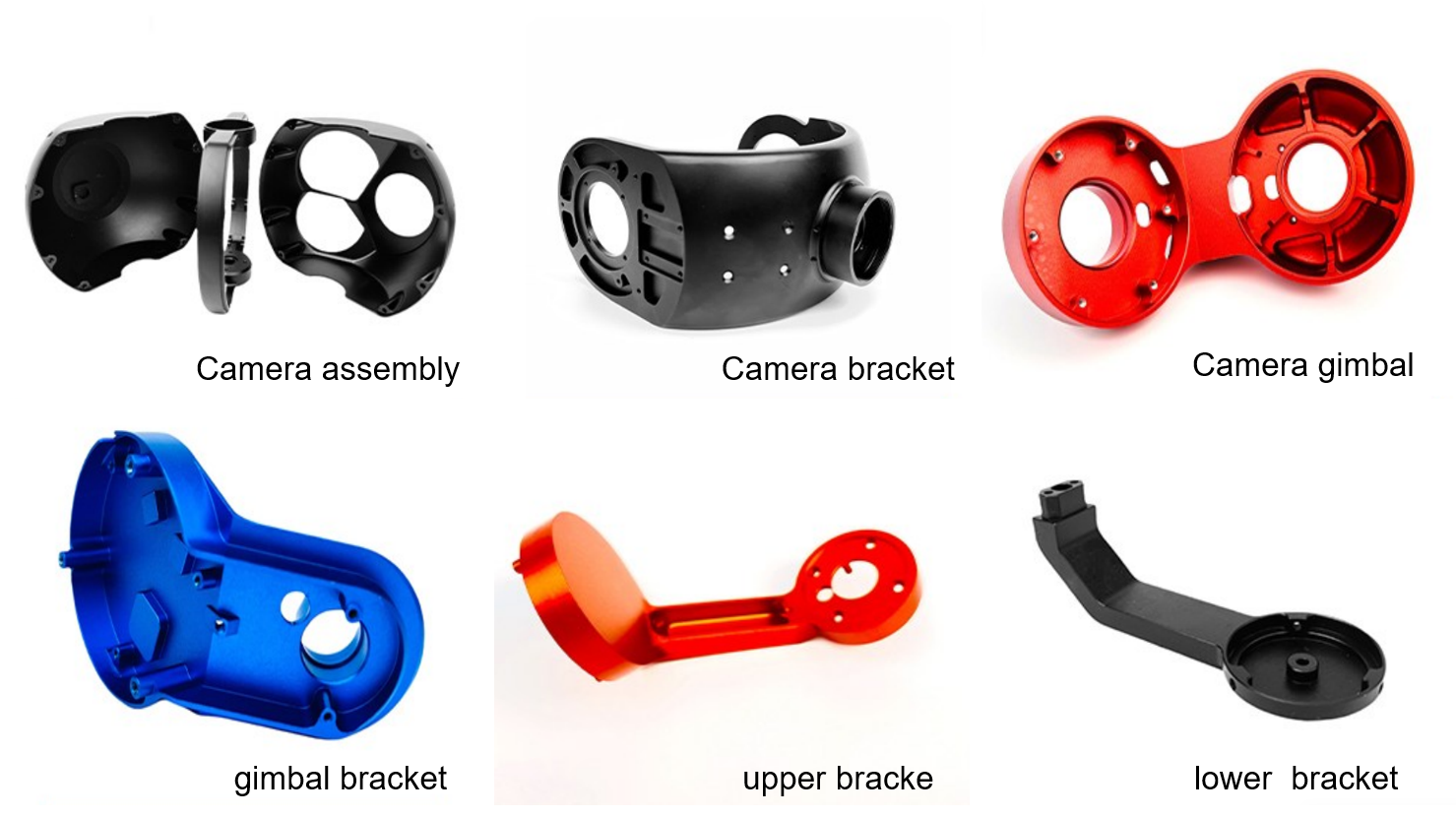
Surface Treatment of Unmanned Aerial Vehicle (UAV) Accessories
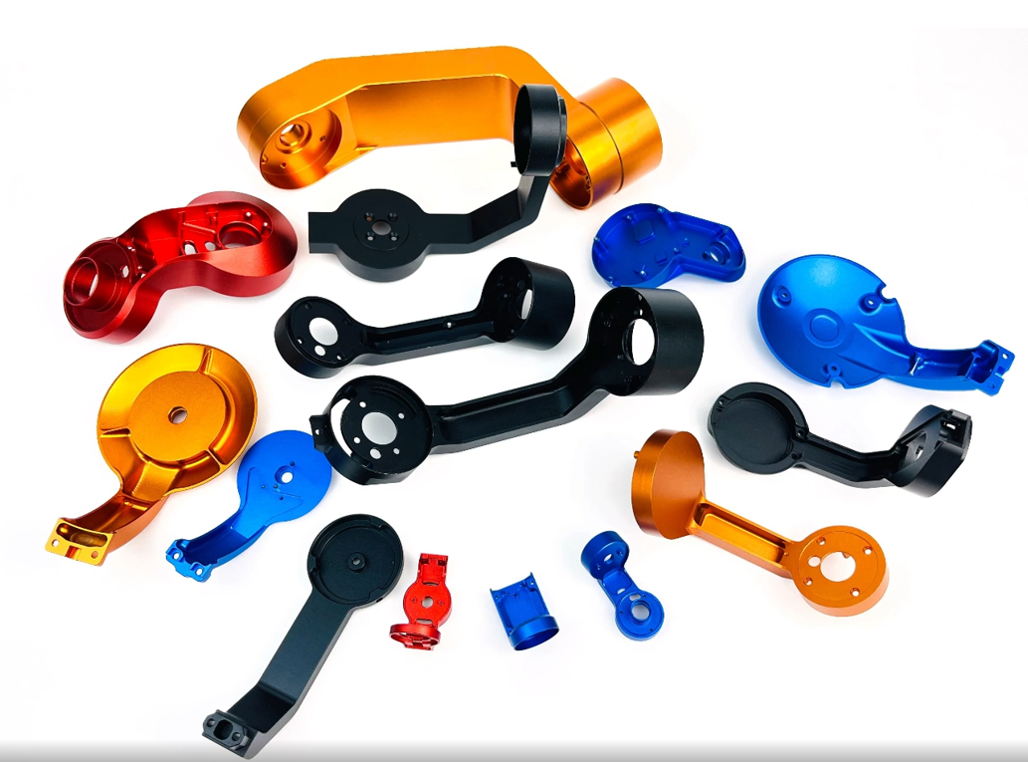