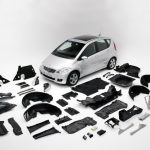
Solutions for the automotive industry
2024-11-05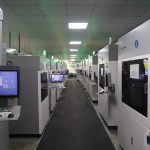
Bently GT3-R solution
2024-11-16
Medical Equipment :
Healthcare is one industry that is the most corelated to human being. It determines the health, lifesapn and life quality. In modern society, with the technology, healthcare has grown fast which brings more opportunities and expectations to human growth. However, after COVID has been everywhere in the world, it is a tough job for global healthcare. In the meantime, it improves the healthcare significantly.
HXC has worked closely with customers worldwide on reseaching muliple innovated medical equipement and has been applied into each area.
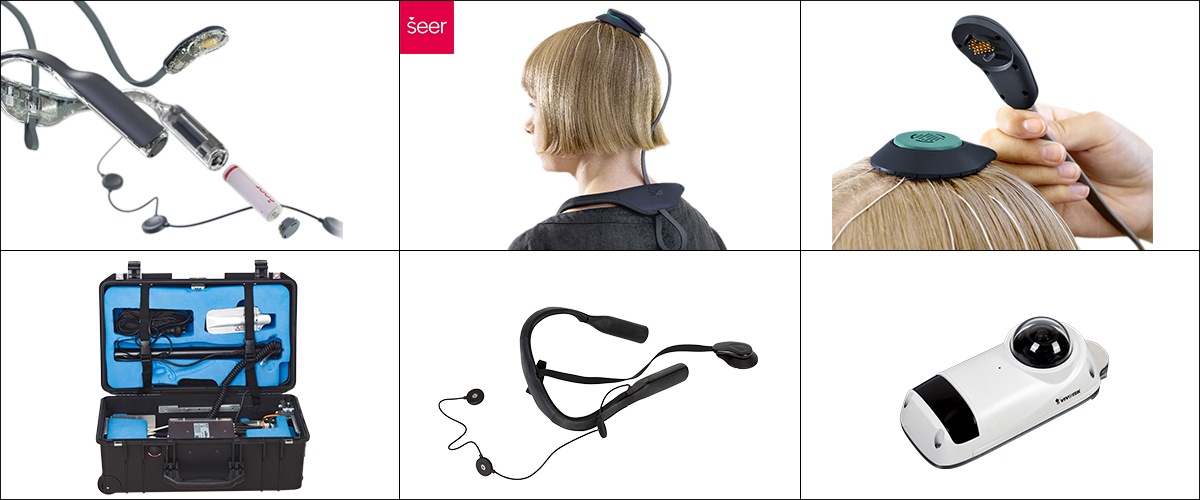
One of our customers that is from Australia, Seer, created a wearable epilepsy diagnosis and monitoring device that has been certified by the US FDA. It combines the advantages of devices, cloud computing, and computer science to transition clinical monitoring from hospitals to homes. The product can diagnose and manage neurological, cardiac, and sleep conditions, creating new clinical care pathways, which is a revolutionary technological breakthrough and won the 2021 Reddot Award for it.
HXC worked with Seer, from prototype to mold design and manufacture, injection molding, mass production till delivering in the end. The problem has been fixed with researching and manufacturing capacity, which made whole reseach process completed smoothly, achieving rapid launch in the market.
While HXC has also accumulated valuable experience and updated with tendency in the combination of high-tech and medical equipment applications.
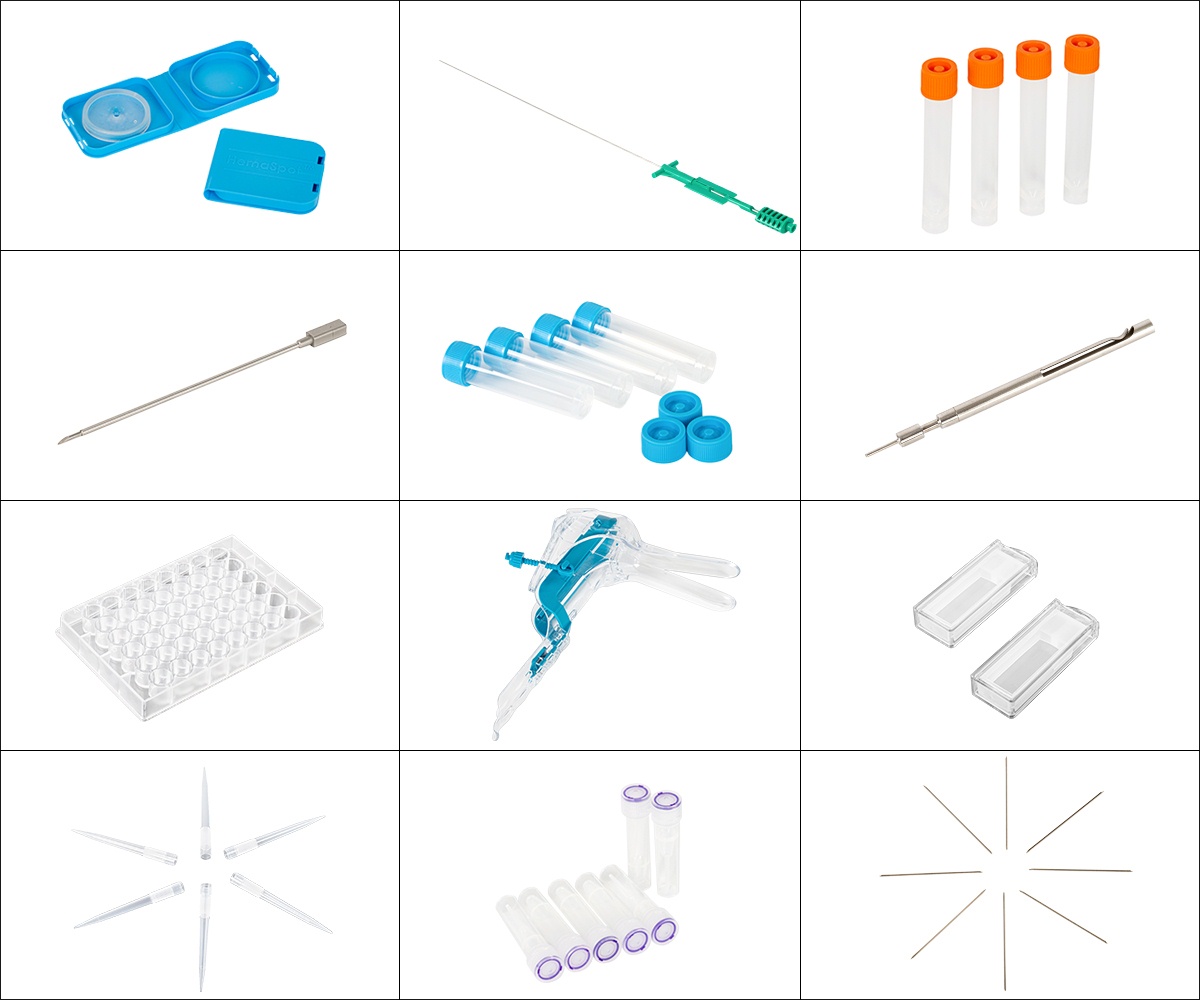
Medical consumables:
Medical consumables accounts giant amount in the medical equipment, also is the product that everyone may contact. Thus, it has a higher requirement in material, size, accuracy,sealing, dust free practicing. Normally,high precise molds and CNC processing will be used.
Plastic tube product requires uniform wall thickness, just like the Daan Gene Co, Ltd, producting virus collection tubes with the mold accuracy of 0.005mm. There is also strict limitation in the biased injection problem. A series of problem encountering in designing will be fixed by our professional engineering team. Now, the tube has been updated to 48 cavities and lids with 64 cavities, which largely improves the working efficiency.
Medical consumable is a big challange for the manufactuer in many aspects, like comprehensive design, processing level, manufacturing capability, working environemnt, etc. With more than 10 years of experience, HXC is specilized in developing, manufacturing capacity, scientific management, meeting all the production needs of all types of medical consumables to achieve better manufacturing.
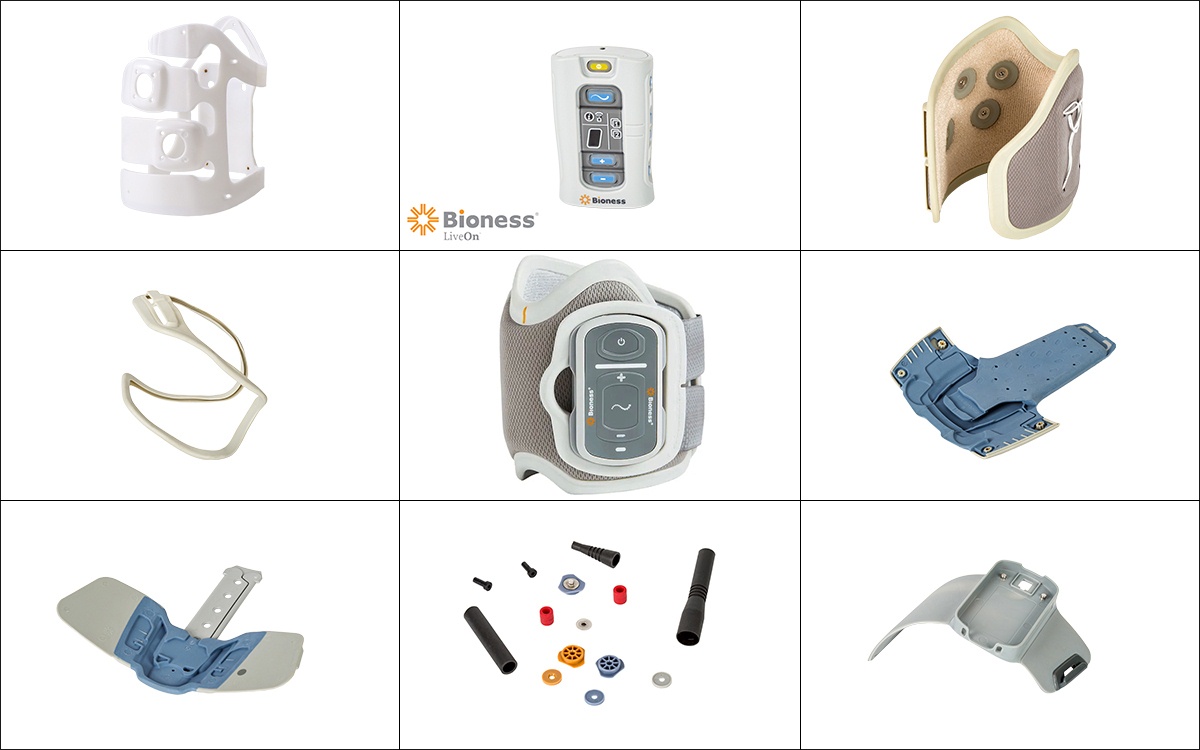
Medical Accessories:
HXC produced processing accessories for all types of medical equipement, from prototype to mass production, from plastic parts to metal parts, customized one-stop industrial manufacturing services are provided using various processes such as CNC machining, 3D printing, sheet metal, injection molding, replication, stamping, die-casting, extrusion, etc., to meet the product needs of global customers.Especially for products and companies that intend to put their product concepts into mass production and market launch, our one-stop service can improves the efficiency and quality greatly with saved cost, and significant short market lanuching time.
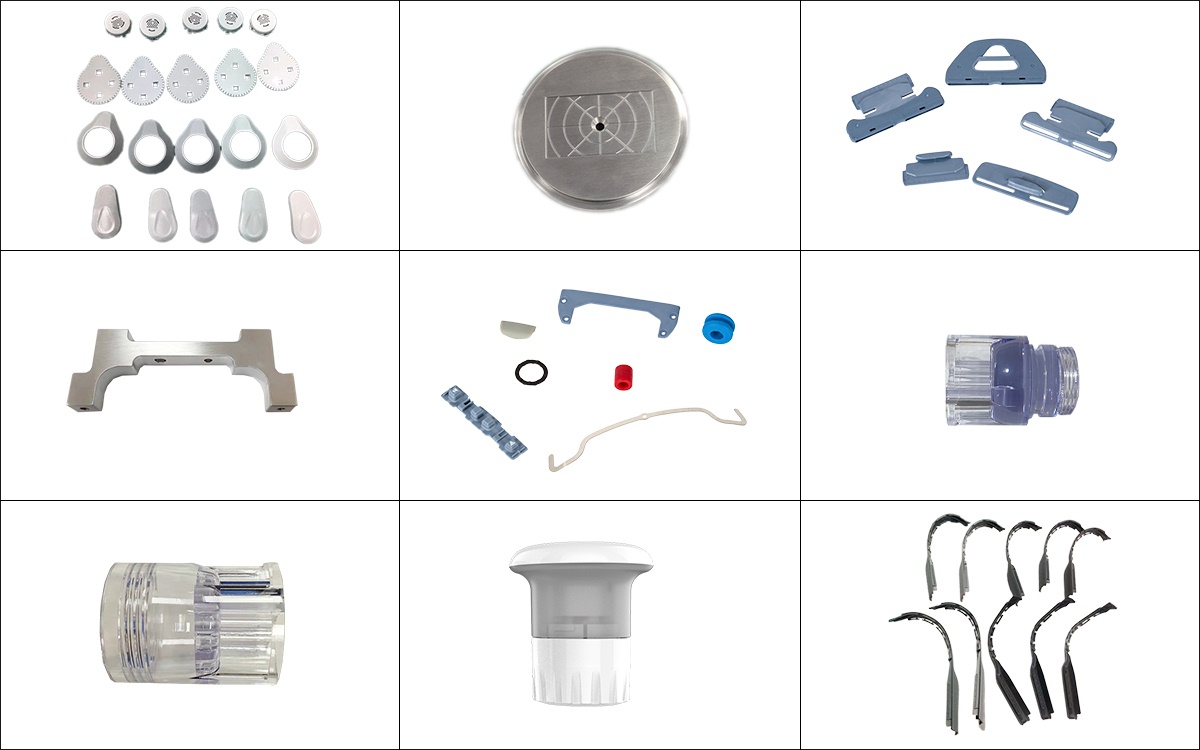
Mass production assembly:
HXC owns German HERMLE C22, C42, C62 5-axis machining centers, AGIE spark machines, Sodick spark machines, Okuma, FANUC and other precision mold processing equipment, and a constant temperature and humidity production workshop. The processing accuracy can reach 0.002mm, and the T1 qualification rate exceeds 90%. Strong mold designing team and over 10 years of precise mold designing experience, as well as quite a few members with over 20 years of industrial experience.Thousands of sets of finished molds are produced and sent to various parts of the world annually.
HXC has independent and standard assembly production lines, and a dust-free workshop of 100000 level. We have injection molding machines such as Sumitomo and Shadick, and can process large quantities of injection molds, two-color molds, and encapsulated molds. The significant production capacity enables us to achieve a yield of over 30 million injection molded products.
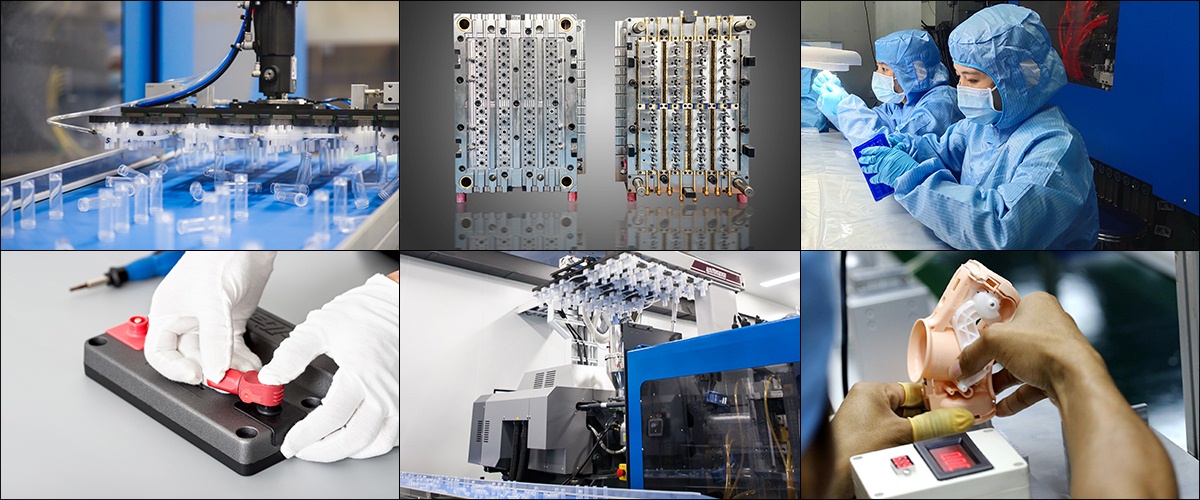