
Injection molding service case
2025-03-05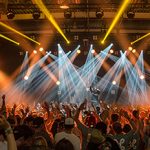
Art Lighting Solutions
2025-03-06Customized case of virus collection tube precision mold
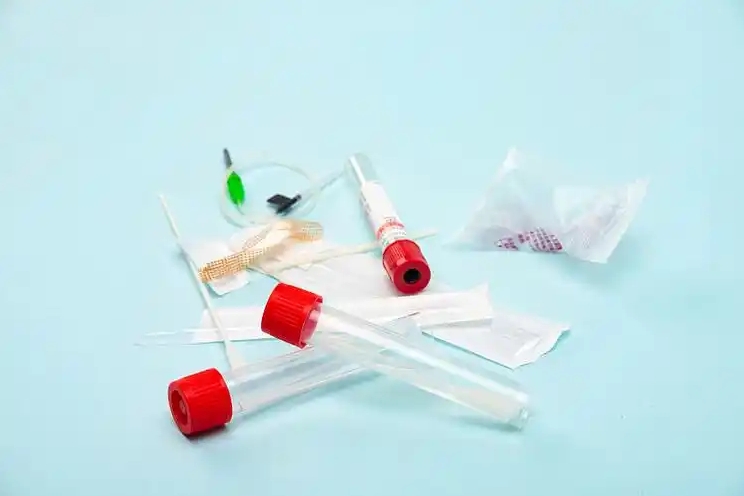
HXC manufactures virus collection tube molds, and then produces 10ml and 30ml virus collection tubes on a large scale through injection molding, which cooperates with large-scale nucleic acid testing of the new coronavirus and makes positive contributions to the early detection and control of the new coronavirus.
Nucleic acid testing is an effective means of prevention and control, and a line of defense for actively screening asymptomatic infections and positive cases. It can detect the source of infection as early as possible and control the spread of the epidemic from the source, preventing the entire epidemic prevention and control from being greatly challenged by the inability to diagnose and isolate in time. This is a particularly important part of the fight against the epidemic. The virus collection tube is undoubtedly one of the important tools for nucleic acid testing.
About the product
We produce high-precision molds for mass production of COVID-19 collection tubes and their caps, which are products that everyone is very familiar with. We have produced precision molds for 10ml and 30ml virus collection tubes. Today we will focus on the 10ml virus collection tube mold that was put into mass production earlier. The 10ml virus collection tube is the same test tube that we often encounter when doing nucleic acid testing, with 10 people in a group using the same tube.
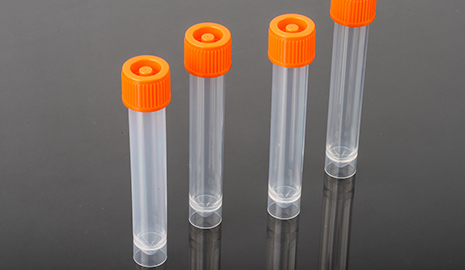
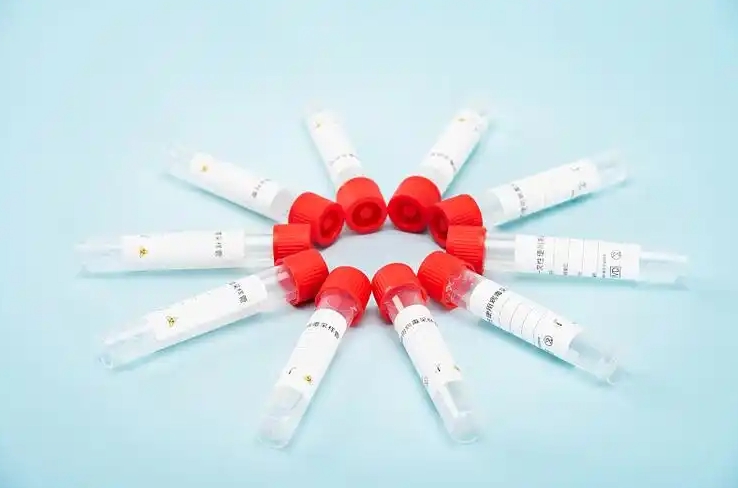
About the Project
Based on more than ten years of experience in the medical industry and rich accumulation of similar products, HXC adopts the IPD (Integrated Product Development) product development model. For each past project, there are detailed project development records. This, to a large extent, not only avoids repeated errors, but also reasonably utilizes existing results, greatly saving the development and production cycle.
Difficulties in mold design and manufacturing technology
In the design and manufacture of molds, we encountered problems of all sizes. Some problems may seem minor, but they will obviously affect the quality of the product, while some serious problems will directly affect the delivery of the product. We have selected representative problems for analysis, but due to technical confidentiality, we cannot make them fully public. Please understand.
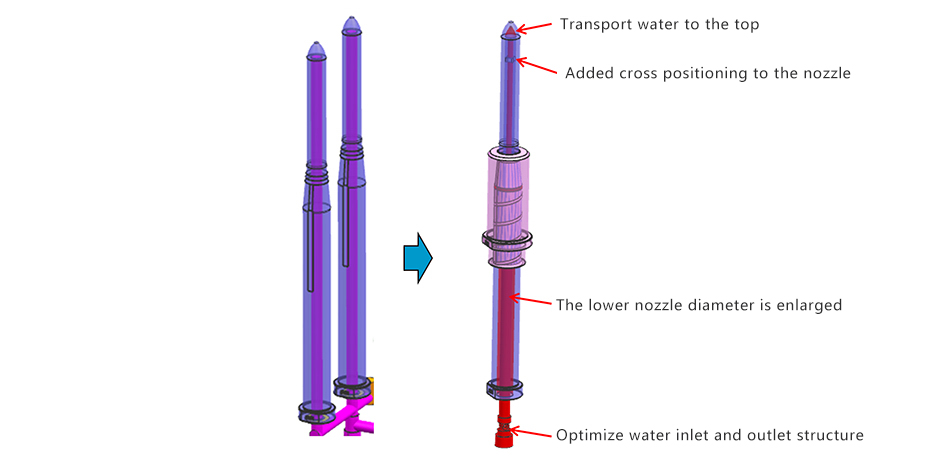
Improvement plan: Optimize the water transport structure as shown in the figure. The mold temperature can be controlled within a 3-degree deviation range.
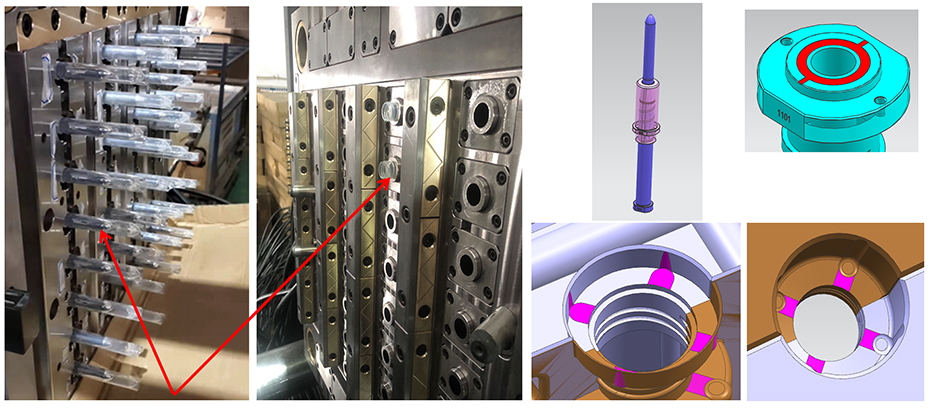
Problem: When the product is T1, it sticks to the front mold and then to the back mold. When ejecting, the front mold is deformed by pulling, and the back mold is deformed by squeezing.
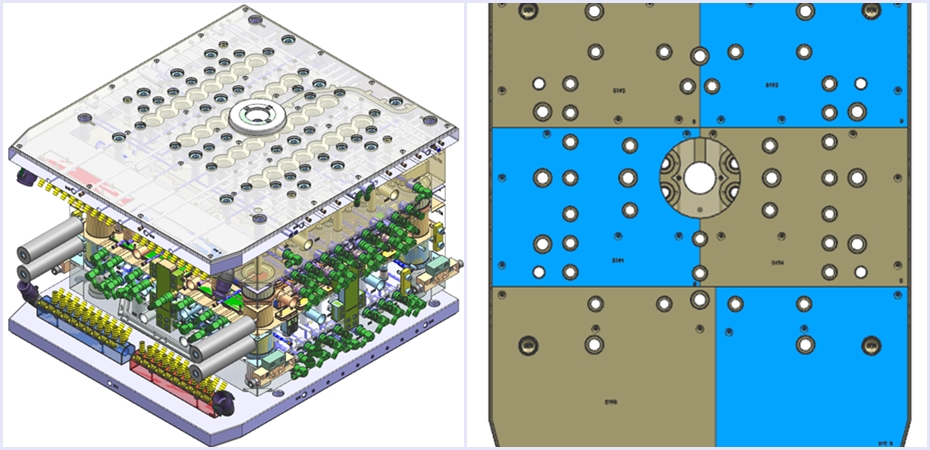
Problem: The insulation board is too large and easy to deform
Mould customization effect
The HXC design team constantly solves problems that arise in design and production one by one. In the face of new solutions and customers' ever-increasing product requirements, we always adhere to the principle that meeting customer requirements is our goal. By modifying the design, testing the mold, repairing the mold, and testing the mold again, we finally fully meet the customer's requirements and deliver qualified products to customers in a timely manner.
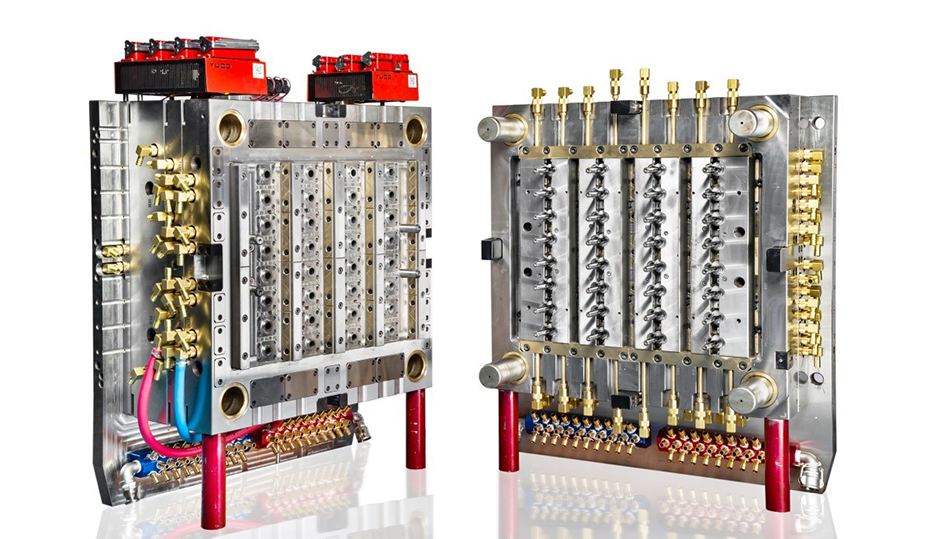
Injection molding process
HXC's injection molds are produced in a dust-free production workshop on Sumitomo injection molding machines. Using fully automatic robots, each set of molds can produce 32 virus tubes every 18 seconds. Each set of molds can produce more than 150,000 virus tubes per day, providing a large amount of support for the front line in the fight against the epidemic.