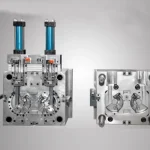
HXC Bending Tube Core-Pulling Mold
2024-10-15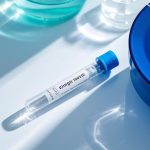
Medical Case, Virus Collection Tube
2024-10-19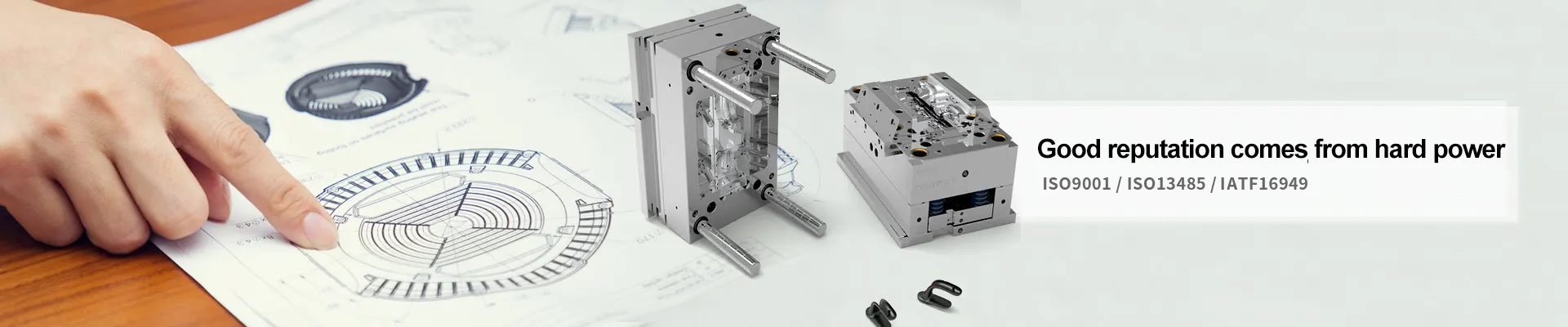
Automotive precision mold customization case
Nowadays, designing and manufacturing of high precise mold has been widely spread in various industries. Precise mold is the fundation of mass production of mold product. In the field of new energy vehicles has also been widely applied. HXC have collaborated deeply , and their products have gained widespread recognition in the market.
The new energy vehicle is the new business of the worldwide automotive industry. Every country has slight difference in the plan of new energy vihicle, but the goal is to take fully advantages of new energy vehicles, reduce the actual pressure on environmental resources, and promote the sustainable development of the domestic economy. Nowadays, China's new energy vehicle industry has entered a new stage of rapid development with scale and high quality. Continuously improving supporting service facilities to make new energy vehicles more attractive.
However, charging is one of the most important sections. An highly effective and stable charging board is a strong support for the electrical cars.
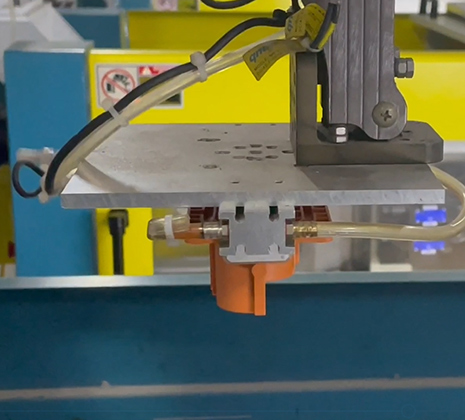
Regarding products:
- Nowadays, designing and manufacturing of high precise mold has been widely spread in various industries. Precise mold is the fundation of mass production of mold product. In the field of new energy vehicles has also been widely applied. HXC have collaborated deeply , and their products have gained widespread recognition in the market.
- The new energy vehicle is the new business of the worldwide automotive industry. Every country has slight difference in the plan of new energy vihicle, but the goal is to take fully advantages of new energy vehicles, reduce the actual pressure on environmental resources, and promote the sustainable development of the domestic economy. Nowadays, China's new energy vehicle industry has entered a new stage of rapid development with scale and high quality. Continuously improving supporting service facilities to make new energy vehicles more attractive.
- However, charging is one of the most important sections. An highly effective and stable charging board is a strong support for the electrical cars.
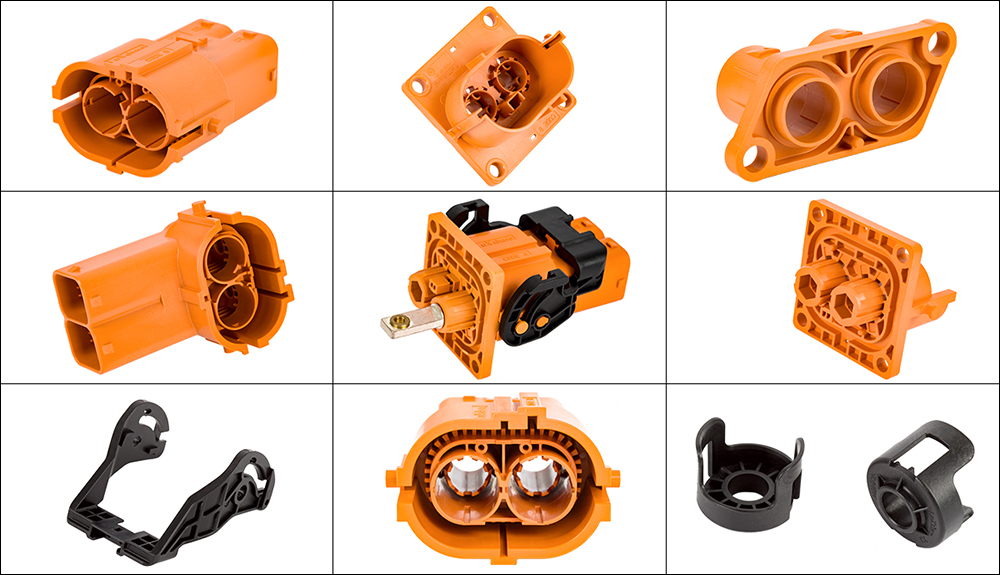
Process:
Mold: CNC machining, wire cutting machining, electrical discharge machining (EDM), mold saving, grinder, fitter.
Product: Injection molding processing.
Material :
PA66+GF25(RAL2003)、PA66+GF30(RAL2003)Product: PA66+GF25 (RAL2003), PA66+GF30 (RAL2003)
Mold: Longji LKM 2344 Advanced Stainless Steel Mold
Regarding mold steel material:
Longji LKM2344 is a type of steel mateiral that was electroslag remelted. The material is uniform, with good hardenability, excellent mechanical processing and polishing properties, good wear resistance at high and low temperatures, easy cutting, high toughness and ductility.The thickness of the material is consistent in both longitudinal and transverse strength, with good high-temperature strength and resistance to thermal fatigue. Due to the advantage of small deformation during quenching, suitable for aluminum, zinc, alloy extrusion molds, long-life plastic hard molds, etc.
Feature: AISIH13/DIN1.2344
hardness: Soft annealed to HB180-210
Chemical composition: Carbon (C) 0.38, Manganese (Mn) 0.4, Silicon (Si) 1.0, Chromium (Cr) 5.0, Molybdenum (Mo) 1.3, Vanadium (V) 1.0.
Mold design manufacturing difficulties:
In the mold design and manufacturing, multiple problems have been encounterd. Some are serious. Some could affect the quality significantly. However, some other serious issues will affect the deliver of product. We have selected the typical ones to talk about. Due to technology confidentiality, the information could not be publiced completely. Thanks for understanding.
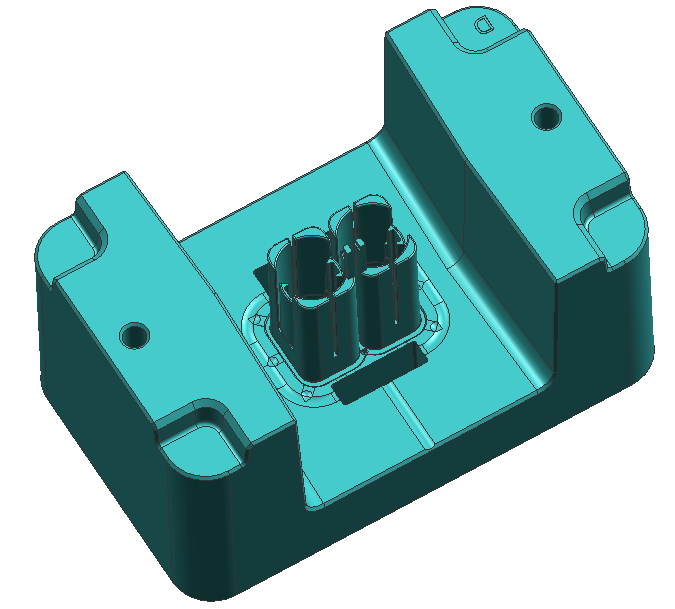
Problem: complex product structure. Traditional cooling mode cannot meet up the needs and the injection molding cycle has been as long as 85s. The deformity of product is evident.
Solution: mold inlay adopts 3D printing with a flexible waterway design.
Improvement effect: The deformation degree has been reduced from 0.6mm to between 0.08-0.12, and the injection molding cycle has been shortened from 85 seconds to a minimum of 25 seconds.
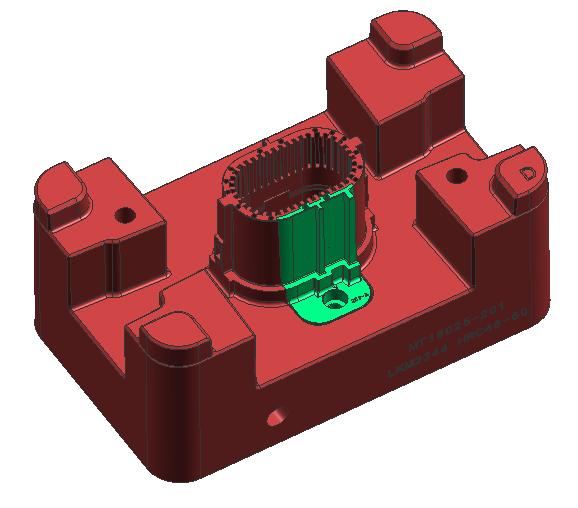
Problem: There are 5 products on the mold. After one of them is completed, the mold needs to be removed from the machine to replace the interchangeable inserts, and the mold is dropped from the mold, causing downtime.
Improvement solution: The parts are designed to be disassembled from the front, and the mold can be replaced without lowering the mold.
Improvement effect: The original replacement time is shortened from 4 hours to 15 minutes.
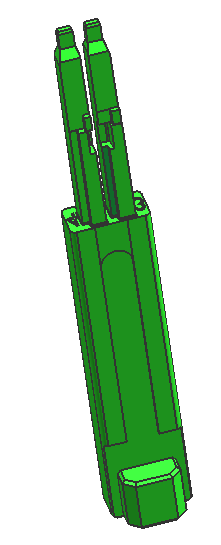
Problem: The size of the mold insert is 7.4x6.5x51.83mm. The top and middle parts of the insert are inserted and need to be sealed. The insert deforms during the processing. Even if the parts are processed and put into the mold for production, deformation still occur after 2000 PCS, making the mold unable to be produced.
Improvement solution: adopt special steel for processing, and then perform deep cooling process after processing to ensure dimensional stability and no deformation.
Improvement effect: The mold insert needs to be replaced after 2000 PCS, but after improvement, it only needs to be replaced after 50,000 PCS.
Injection molding process :
In injection molding workshop, the precised injection molding molds are all rully automatic robot produced by HXC, each takes around 25sec averagely.
Custom mold summary :
Since 2018, our long-term cooperation with customers has started from the design and manufacture of molds. During this process, we delivered products in batches. These products were widely used in new energy vehicle projects. While achieving a win-win situation with customers, HXC also contributed our own efforts to the promotion of the new energy industry. I believe that in the field of new energy in the future, HXC will have a broader development prospect.
Indeed, all the success is not random, but our effort through more than ten years of industry experience, continuous summarization and innovation to achieve the project. The efforts of all staff are inseparable. At the same time, the support of sophisticated equipment, the gathering of cutting-edge technical talents, and the continuous improvement of strength are the secrets of our success.
Striving for excellence is our aim and also the motivation to pay attention to each detail.