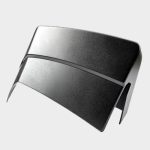
Automobile prototype processing case-housing parts
2025-04-14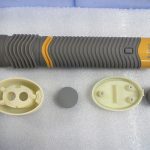
Prototype Case-Medical Cleaner
2025-04-15Automobile prototype processing case-headlight frame
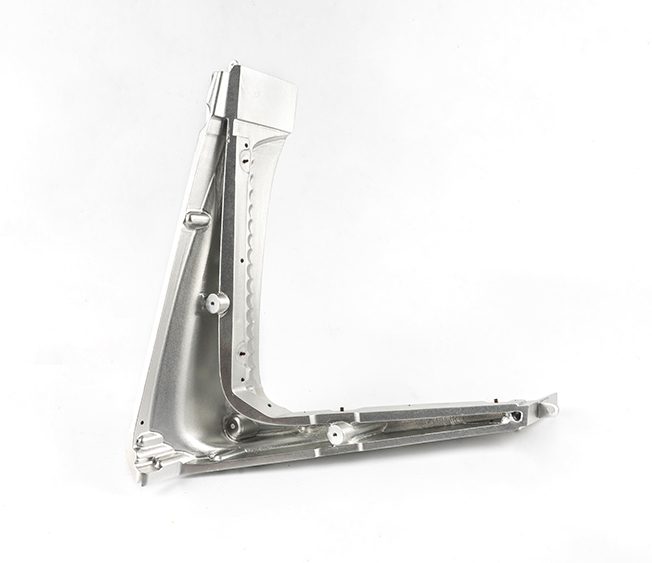
Processing method: CNC metal processing
Material: Aluminum
Maximum precision: 0.01mm Production cycle: 2~3 days
Product size: 25cm*28cm*30cm
Post-processing: Polishing
Case Introduction
Lamp stand prototype processing refers to the production of samples or models used to verify the design of lamp stands during the design and development of automotive lamps. These prototypes (also called samples, prototypes) are important physical prototypes used to evaluate the practicality, structural strength, assembly compatibility of the design, and to conduct related functional tests. The following are the general steps for lamp stand prototype processing:
Design stage: Designers first use computer-aided design (CAD) software to draw the design of the headlight frame. This includes determining key parameters such as the size, shape, support structure and connection points of the headlight frame.
Material selection: Choose the appropriate material according to the purpose and needs of the prototype. Common materials include plastics (such as ABS, PC), metals (such as aluminum alloy), or other composite materials.
Manufacturing method: Choose appropriate rapid prototyping technology to manufacture the prototype. Common methods include 3D printing (such as stereolithography, selective laser melting), CNC milling, laser cutting, etc.
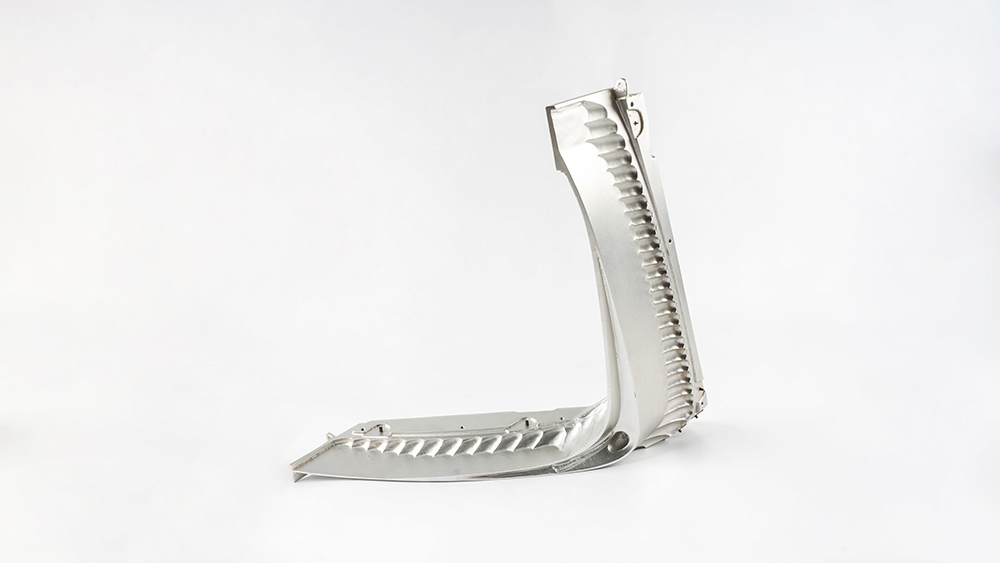
Post-processing: After rapid prototyping, the prototype usually requires further post-processing, such as grinding, polishing, painting, assembly, etc., to achieve the final appearance and functional requirements.
Assembly and testing: Install the headlight holder prototype on the corresponding vehicle, conduct fit check and function test to ensure that its structure is stable and the headlight assembly can be installed correctly.
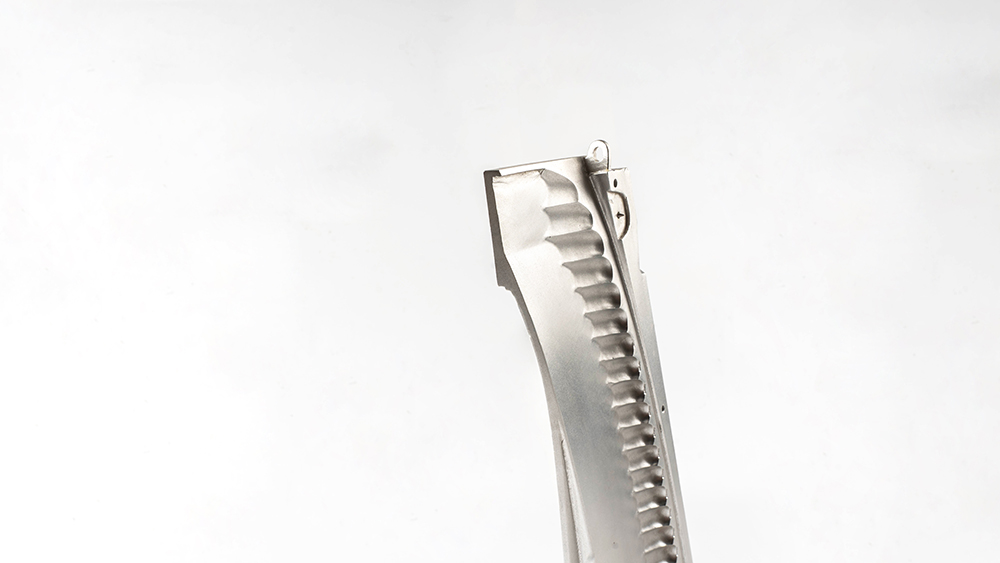
Evaluation and optimization: Based on the results of actual assembly and testing, necessary adjustments and optimizations are made to the headlight bracket design. This may involve multiple rounds of iterations until the product meets the design standards and performance expectations.
Confirmation and preparation for production: Once the headlight frame prototype is verified and confirmed to meet all design and performance standards, the project can move to the next step, such as the design and manufacture of mass production molds.
Headlight frame prototype processing is an important part of ensuring product design quality. It allows engineers and designers to discover and solve problems before actual production, thereby reducing production costs and risks.
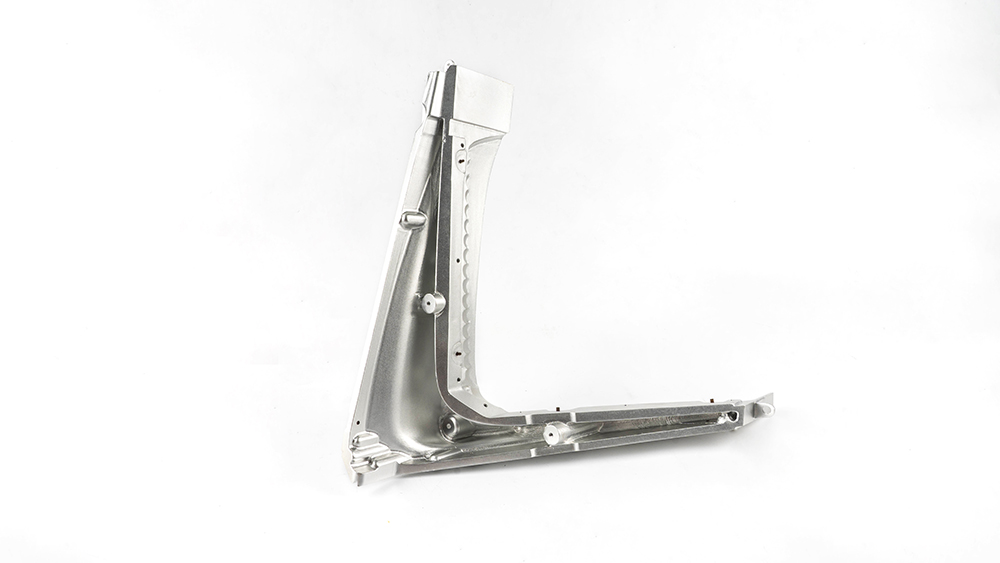