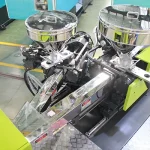
Professional and reliable two-color mold and injection molding solutions
2025-04-16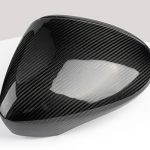
Porsche 911 rearview mirror shell processing case
2025-04-18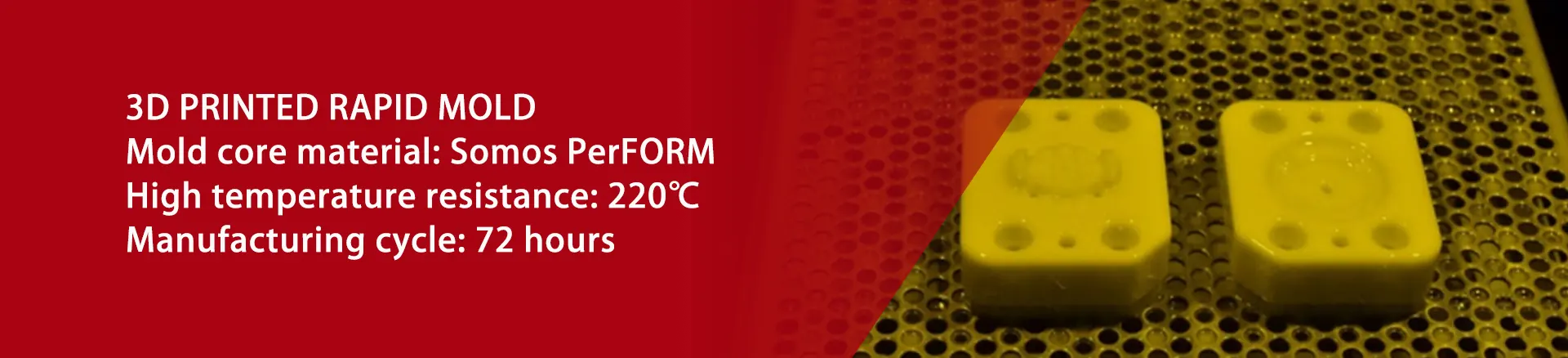
Project Information
This is an intelligent hardware product specifically designed for bicycle riders, which makes it more convenient for riders to fix their mobile phones for use
The sample part is a component that fixes the product to the bicycle bracket. In the earliest stage of development, the SLA 3D printing method was directly used to quickly produce the prototype. It is inexpensive and fast. A 3D printed sample can be obtained within one day, which is used for verifying the product's size and structure
The feature of the mass-produced product is that it can be directly installed on the dash cam. It can be snapped into the bracket through a rotating installation, which is convenient for riders to quickly install and remove. During the outdoor sports of riders, the bumps on the road surface and the vibration transmitted from the bicycle to the dash cam will test the installation stability and connection strength of the connector
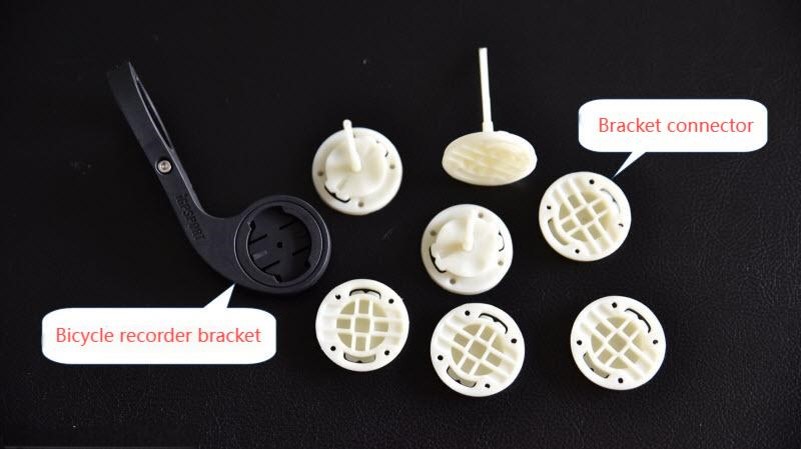
Mold core printing
Lorem ipsum dolor sit amet, consectetur adipiscing elit, sed do eiusmod tempor incididunt ut labore et dolore magna aliqua. Ut enim ad minim veniam, quis nostrud exercitation ullamco laboris nisi ut aliquip ex ea commodo consequat. Duis aute irure dolor in reprehenderit in voluptate velit esse cillum dolore eu fugiat nulla pariatur. Excepteur sint occaecat cupidatat non proident, sunt in culpa qui officia deserunt mollit anim id est laborum.
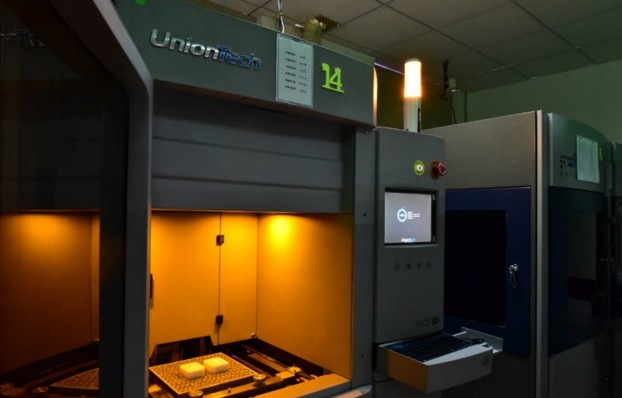
Printing cycle: 3.5 hours
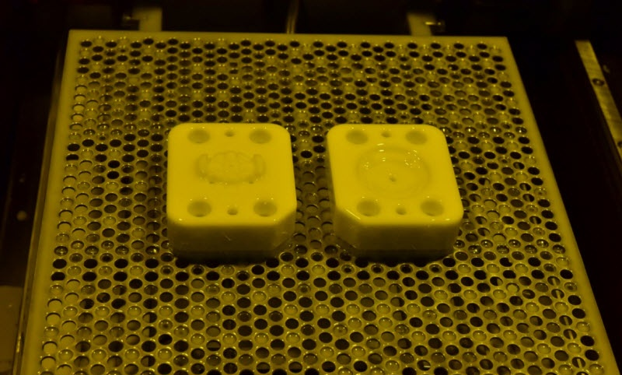
3D printed mold core
The mold material used is Somos PerFORM photosensitive resin material, which contains ceramic components. The hardness of the mold and its high-temperature resistance meet the requirements of rapid molds.It can resist high temperatures up to 220℃
Mold assembly
The dimensional tolerance of the periphery of the 3D printed mold core is ±0.1mm. After fixing the front and rear mold cores, they need to be machined according to the dimensions of the mold base to meet the specified requirements.
The mold base part adopts a traditional metal mold base. The product is ejected automatically by an ejector pin plate. For low-volume injection molding, traditional injection molding is also used. Except that the molding part is completed by 3D printing, other structures of the mold are processed in the traditional way
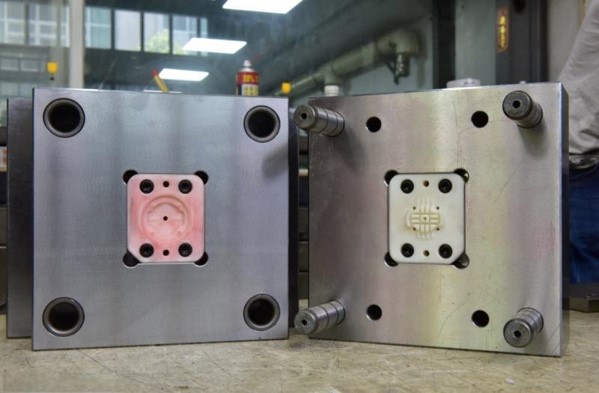
Mold trial
The number of the first mold trial is 15 pieces, which are used for dimensional inspection and assembly testing. All the data obtained from the inspection provides support for the subsequent assembly testing and helps to confirm the subsequent modification plan. The assembly testing mainly aims to verify whether the toughness of the material can support the weight of the mobile phone and determine whether it is necessary to make structural adjustments to the product.
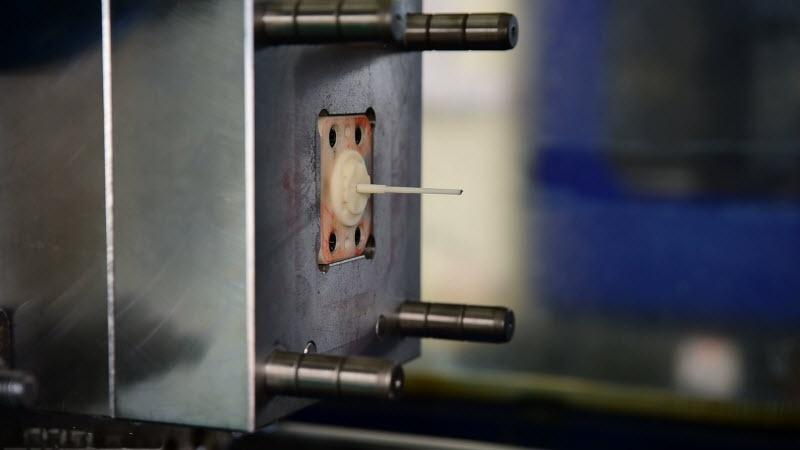
Small batch trial production
After we carried out dimensional inspection and assembly testing on the product, we sent the data and the test videos to the customer for confirmation at the same time. We also held a video conference with the customer, and it was confirmed that small batch trial production could be carried out. The first batch of 35 products was sent to the customer for the final mountain terrain test.
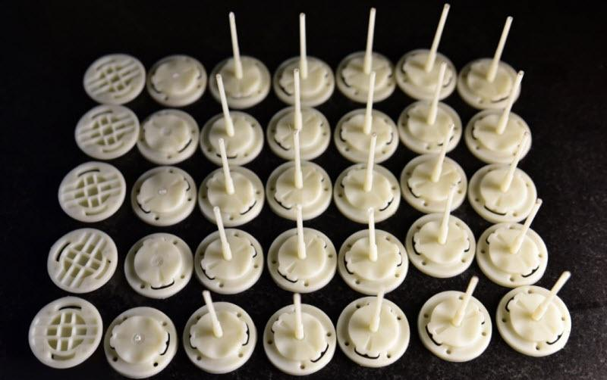
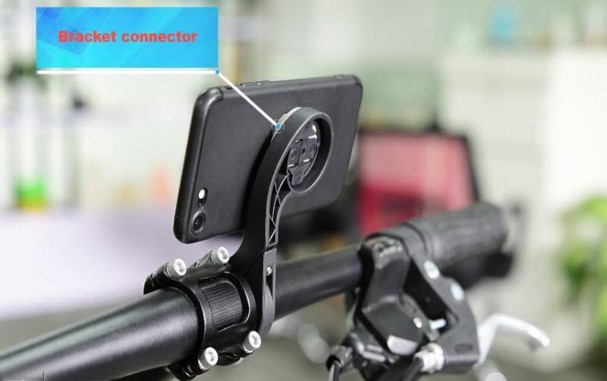
Functional testing
It is necessary to select products made by rapid molds for the final mountain terrain test, because there will still be significant differences in performance between the materials of the mold replication products and the injection molding materials. For example, in terms of the mechanical properties of structural components, and the product we produced this time belongs to structural components. Choosing production by rapid molds can avoid such problems.