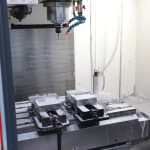
Turning different materials, HXC use of tools
2024-11-05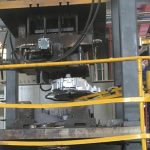
Pressure Die Casting: FAQ Guide
2024-11-05
HXC high-precision manufacturing process mystery
With the evolution of industrial development and changing demands, the precision machining industry has undergone significant transformations, characterized by an increase in categories, specialization in directions, and a trend towards greater professionalization. Technological advancements have spurred continuous innovation in techniques, enhancing both the quality and precision of machining. In sectors such as aerospace, medical devices, and optical instruments, the precision requirements for components are stringent, often reaching micrometer or even nanometer levels. To meet the needs of other industries, the precision machining sector is also innovating and breaking through in its machining technologies.
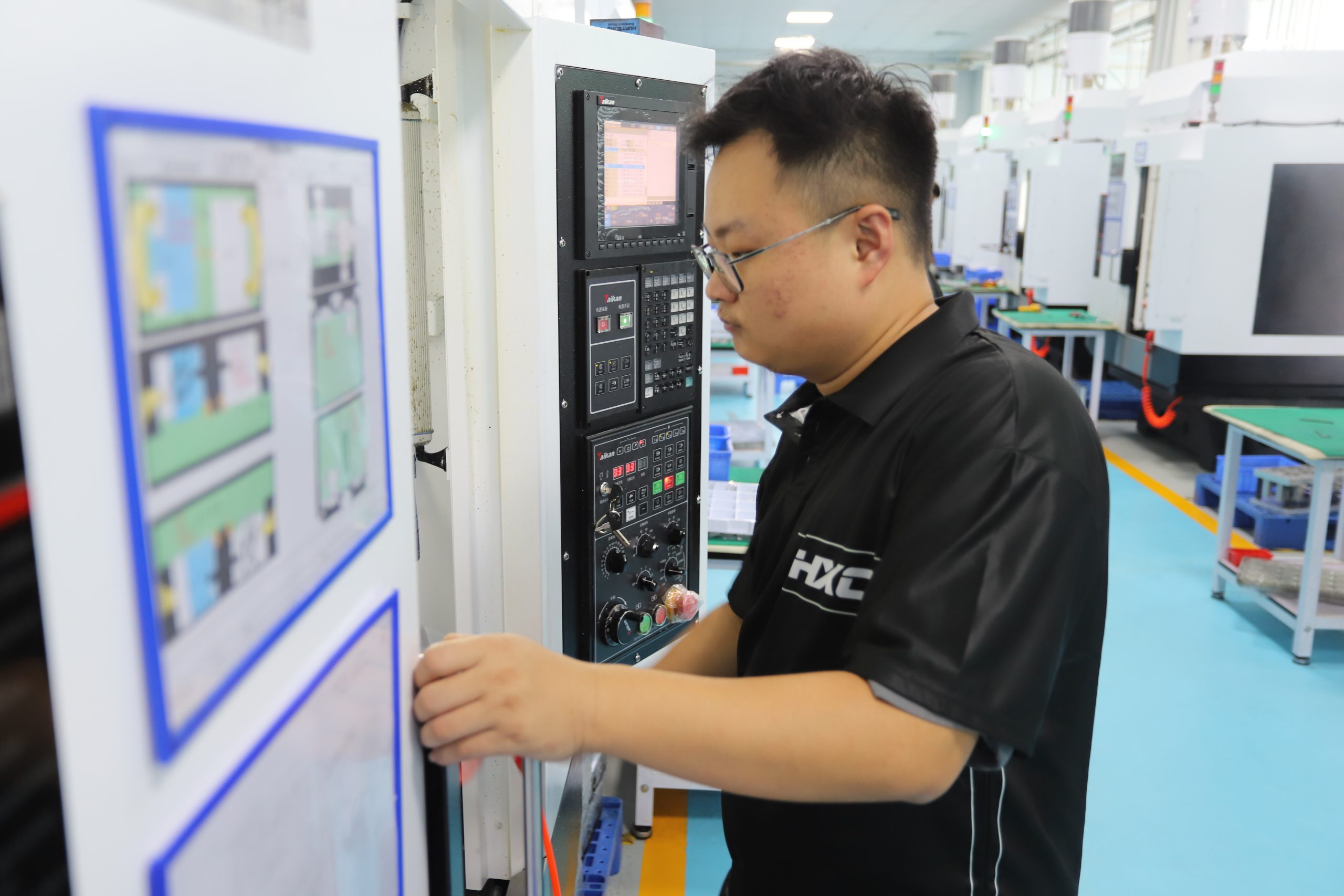
1.Core Processes of Precision Machining
The key technologies in precision machining include ultra-precision turning, grinding, and polishing. Ultra-precision turning employs diamond tools to achieve nanometer-level machining accuracy, particularly suitable for processing optical components. Grinding uses diamond or CBN (Cubic Boron Nitride) wheels, effectively handling hard and brittle materials with precision up to sub-micron levels.
Moreover, precision measurement technology is crucial for ensuring machining accuracy. Equipment such as laser interferometers and white light interferometers can achieve high-precision measurements at the nanometer level, ensuring that component dimensions and shapes meet standards. Online measurement technology allows real-time monitoring of the machining process, enabling timely adjustments and further ensuring machining quality.
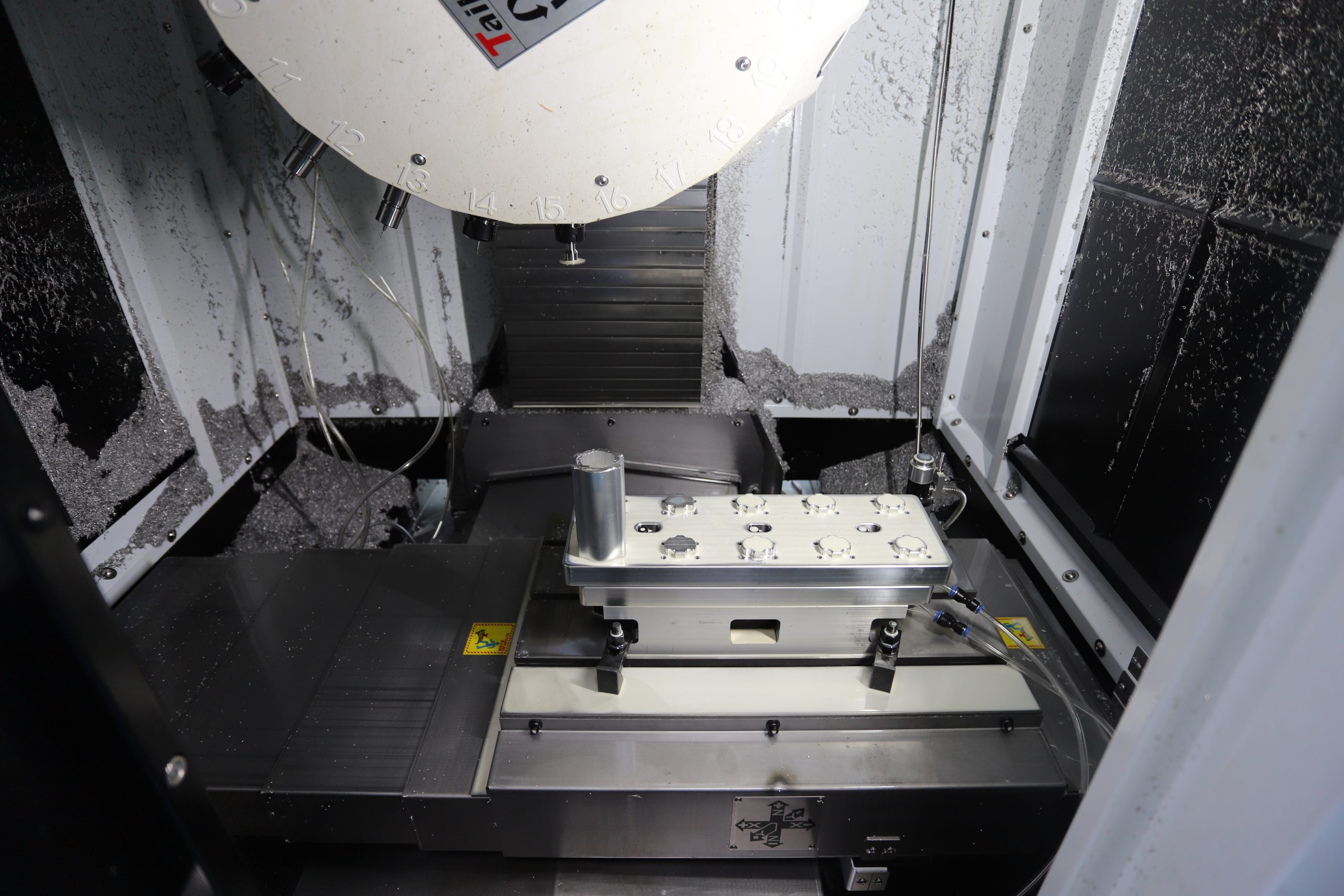
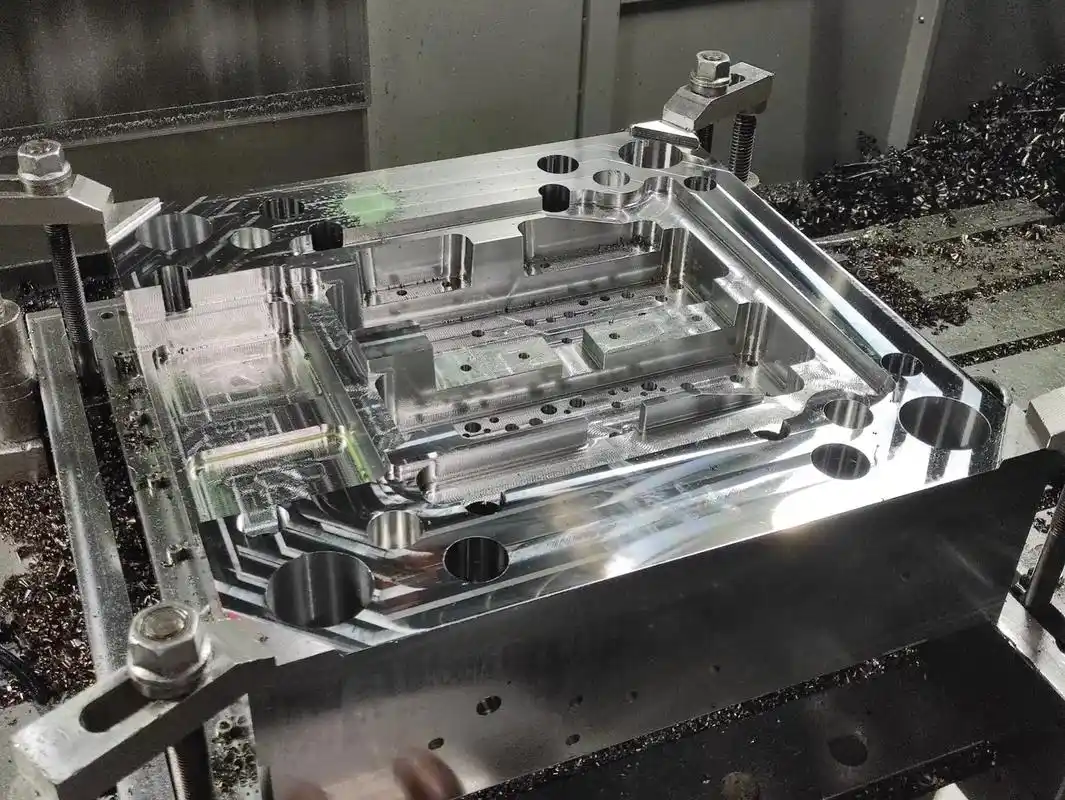
2. Technical Characteristics of Precision Machining
Precision component machining involves numerous stringent requirements and characteristics. Firstly, in terms of accuracy, it is essential to strictly adhere to design specifications during machining and inspection to achieve high machining accuracy and surface finish, ensuring superior precision. Secondly, the selection of equipment is critical; high-precision CNC machining tools and precision measuring instruments are necessary to ensure that the produced components meet standard precision and quality. Additionally, leveraging modern manufacturing technologies such as CAD/CAM, 3D printing, and micro-machining is indispensable for enhancing machining precision and efficiency.
Regarding raw materials, precision manufacturing demands the use of high-quality materials with consistent and standardized batches. The hardness, density, and mechanical properties of these materials must also meet manufacturing requirements. In terms of the production environment, maintaining strict cleanliness is key, as even minor impurities or contamination can adversely affect the quality of component manufacturing.
In terms of machining processes, precision components often require special extended processes such as electrical discharge machining (EDM), wire cutting, and other non-traditional, efficient, and gentle techniques. Furthermore, the entire precision component machining process must adhere to a meticulous quality control approach, strictly managing each intermediate step and promptly addressing any issues to ensure that the quality and precision of the components fully meet requirements.
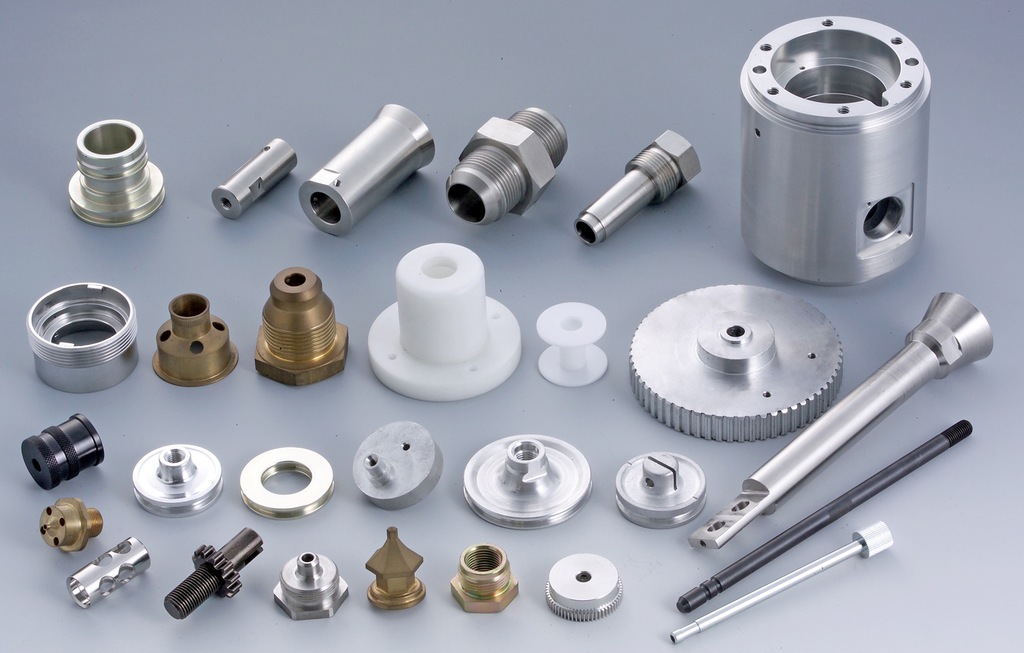
3. Conclusion
Precision component machining technology is advancing towards higher precision, greater efficiency, and broader applicability. With continuous breakthroughs in new materials, processes, and technologies, precision machining will play an increasingly vital role in high-end manufacturing, driving the manufacturing industry towards higher standards.
- Date
- 2024-11-05
- Date
- 2024-11-05
- Date
- 2024-10-21
- Date
- 2024-10-19