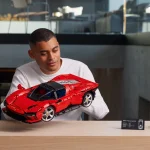
LEGO 零件
2024-10-21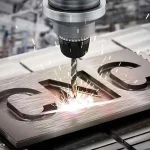
HXC high-precision manufacturing process mystery
2024-11-05
Turning different materials,HXC use of tools
In this era of rapid technological advancement and iteration, the boundaries of the traditional mechanical field are continuously being expanded. Metal materials, after being processed into precision parts, act like keys that unlock the doors to numerous emerging industries. Among these, the 3C industry—comprising computers, communications, and consumer electronics—stands out as a shining star in the new industrial landscape, showcasing vigorous vitality.
In the process of metal machining, metal cutting is the crucial key. The role of cutting tools in the machining process is pivotal, directly influencing the quality of the product. The success or failure of a product often hinges on the choice of cutting tools. Today, let's delve into the fascinating "small world" of turning operations and explore how to select the ideal "dream tool" when dealing with different metal materials.
Steel materials can be categorized into non-alloy steel, low-alloy steel, and high-alloy steel, and the type of tool also affects the efficiency of turning operations.
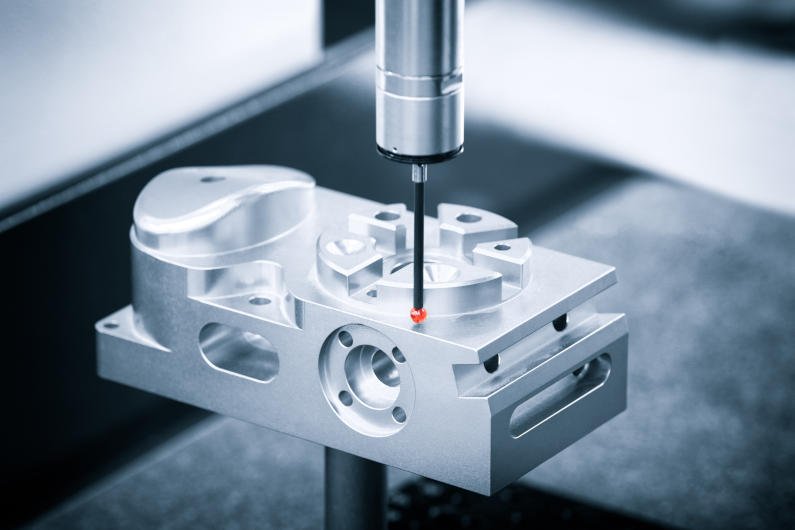
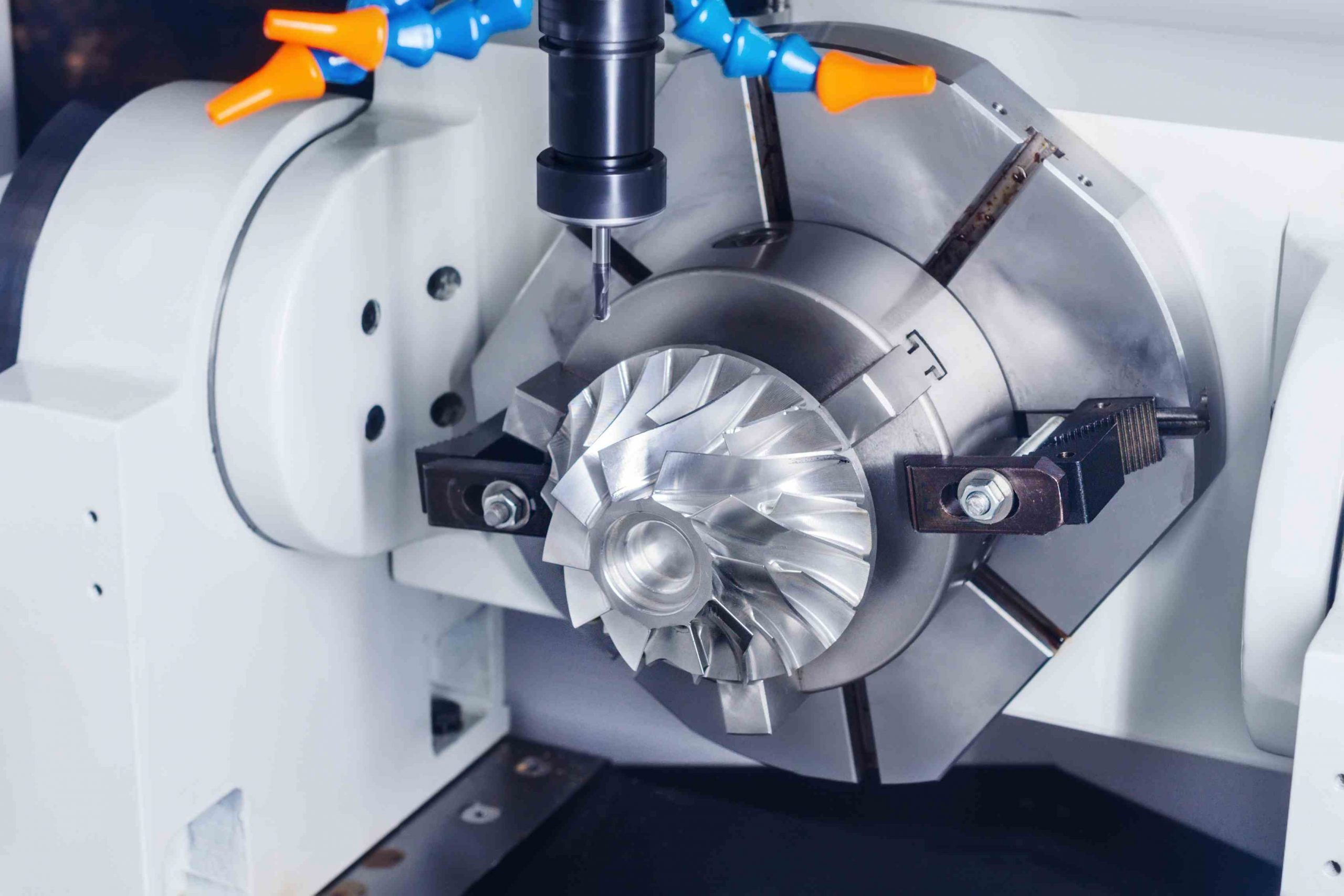
Non-alloy steel (carbon content below 0.55%): The battle against chip breaking
When turning non-alloy steel, chip breaking is like a stubborn "roadblock," and it is also prone to forming built-up edges. In the delicate work of precision part machining, overcoming the challenges of chip formation and breaking requires increasing the feed rate. Excessive built-up edges can shorten tool life. Increasing the cutting speed can reduce the occurrence of built-up edges, ensuring smooth machining.
In this process, some key considerations for tool selection have been summarized: First, the tool coating is crucial; wear-resistant coatings can resist the erosion of built-up edges and extend tool life. Second, the tool's rake angle should not be too small; an appropriate rake angle helps chips flow out smoothly, reducing clogging.
Low-alloy steel: Clever tricks to combat wear
The machinability of low-alloy steel depends on heat treatment (hardness) and alloy content. During turning, the most common tool wear is flank wear and crater wear. Therefore, tools with extremely high resistance to flank wear should be preferred.
When selecting such tools, attention should be paid to the tool body material; high-quality carbide tool bodies provide solid support for wear resistance. Additionally, the tool's edge sharpness retention should be good; otherwise, frequent sharpening will delay work and affect overall efficiency.
High-alloy steel: No fear of high-temperature deformation
High-alloy steel is similar to low-alloy steel in that the higher the alloy content and hardness, the lower the machinability. When turning precision parts made of high-alloy steel with a hardness of HB450, the cutting zone instantly becomes a "steaming pot," prone to causing plastic deformation. Therefore, tools with high resistance to plastic deformation and cutting edge strength should be considered.
When selecting tools, attention should be paid to the tool's heat dissipation structure; good heat dissipation design can prevent high-temperature accumulation and avoid rapid tool softening. Additionally, the compatibility between the tool and the workpiece must be precisely considered; different shapes and specifications of high-alloy steel workpieces require targeted tool matching to achieve high-quality cutting.
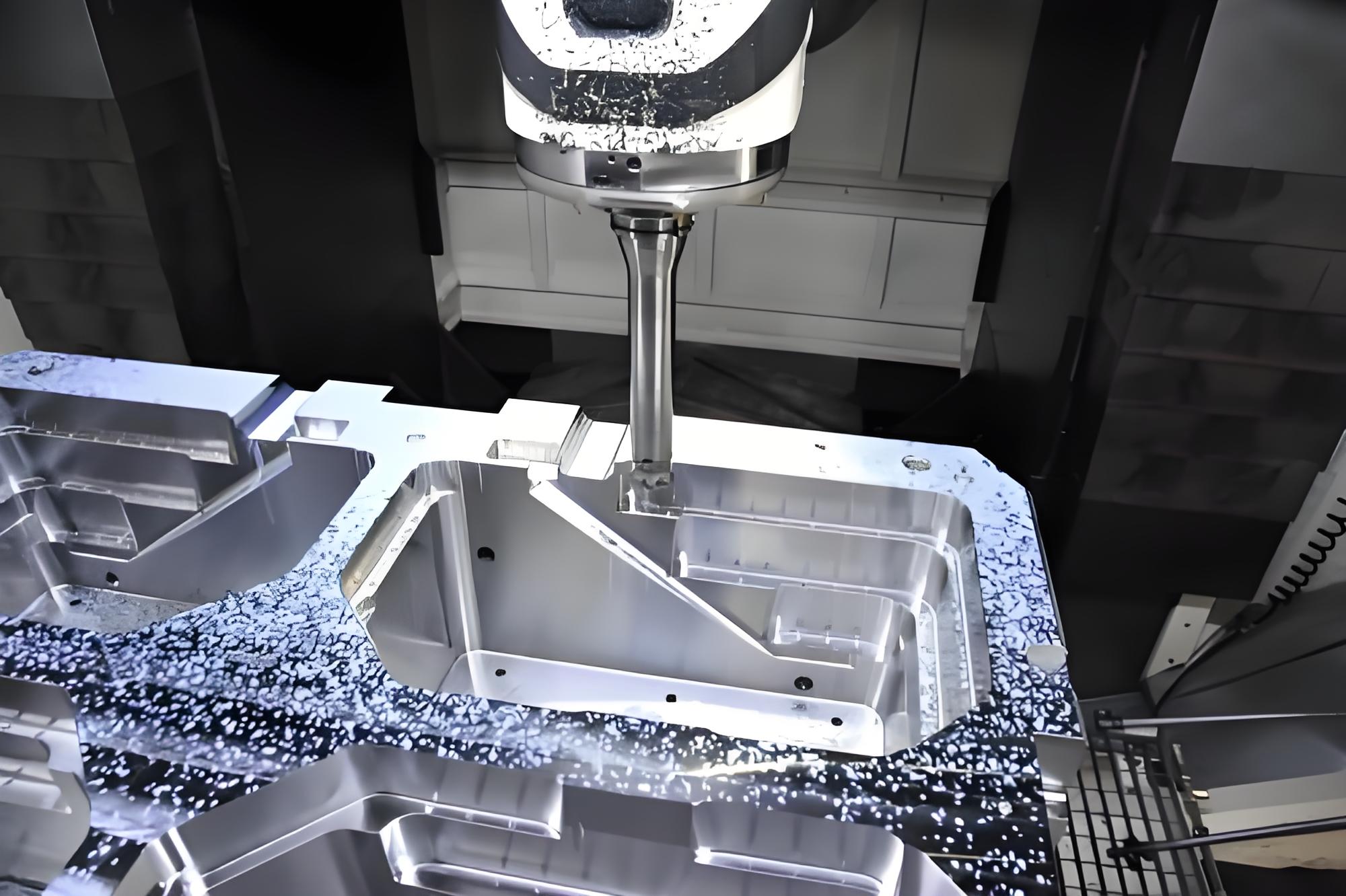
Stainless steel cutting: Stainless steel also has its "quirks"
Stainless steel can be classified into ferritic/martensitic stainless steel, austenitic stainless steel, and duplex (austenitic/ferritic) stainless steel.
Ferritic and martensitic stainless steel: Clever handling of similar characteristics
The cutting characteristics of these two types of stainless steel are similar to those of low-alloy steel. When dealing with hardened martensitic stainless steel in precision machining, tools with high resistance to plastic deformation are required to "tame" this tough material and carve out perfect parts.
For these types of stainless steel, the tool's corrosion resistance cannot be overlooked, given the unique machining environment of stainless steel. Moreover, the tool's toughness must be sufficient; tools with poor toughness are prone to chipping when dealing with hardened stainless steel, leading to machining failures.
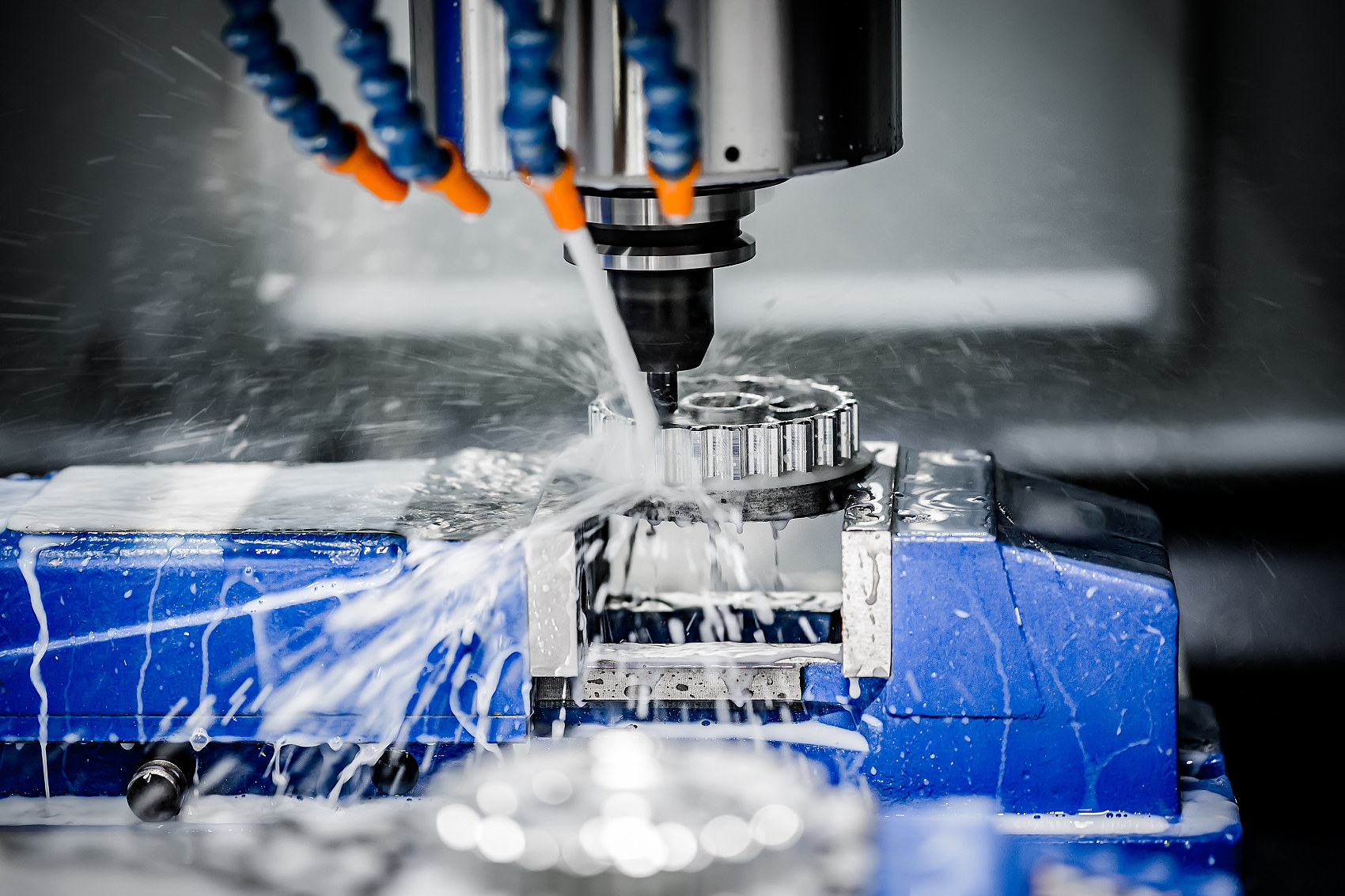
Austenitic stainless steel: Cleverly resolving special wear issues
Among stainless steels, austenitic stainless steel is the most common. However, common tools often experience crater wear, plastic deformation, and built-up edges during machining. Turning also produces "work hardening," which leads to groove wear and burrs on the tool. Therefore, round inserts or small lead angles should be chosen to prevent groove wear, effectively blocking it.
When selecting tools, attention should be paid to the chip breaker design; a reasonable chip breaker can ensure timely chip breaking, preventing chip entanglement. Additionally, the tool's surface finish should be high; rough tool surfaces are more prone to chip adhesion, exacerbating wear.
Turning is one of the most common metal cutting methods in precision part machining. Feed rate, cutting speed, and cutting depth are the main parameters that directly affect tool life. Different materials have different characteristics, and with the vast variety of materials, specific analysis is required during machine operation.
- Date
- 2024-11-05
- Date
- 2024-11-05
- Date
- 2024-10-21
- Date
- 2024-10-19