How does HXC's processing inspection process differ from other suppliers?
HXC has a strict quality management process, from incoming material inspection, first piece inspection, to finished product inspection, every step is strictly controlled to ensure that your workpiece meets the requirements. When we deliver the product, you will receive complete documents and certificates of conformity to ensure that your regulatory and performance goals are met.
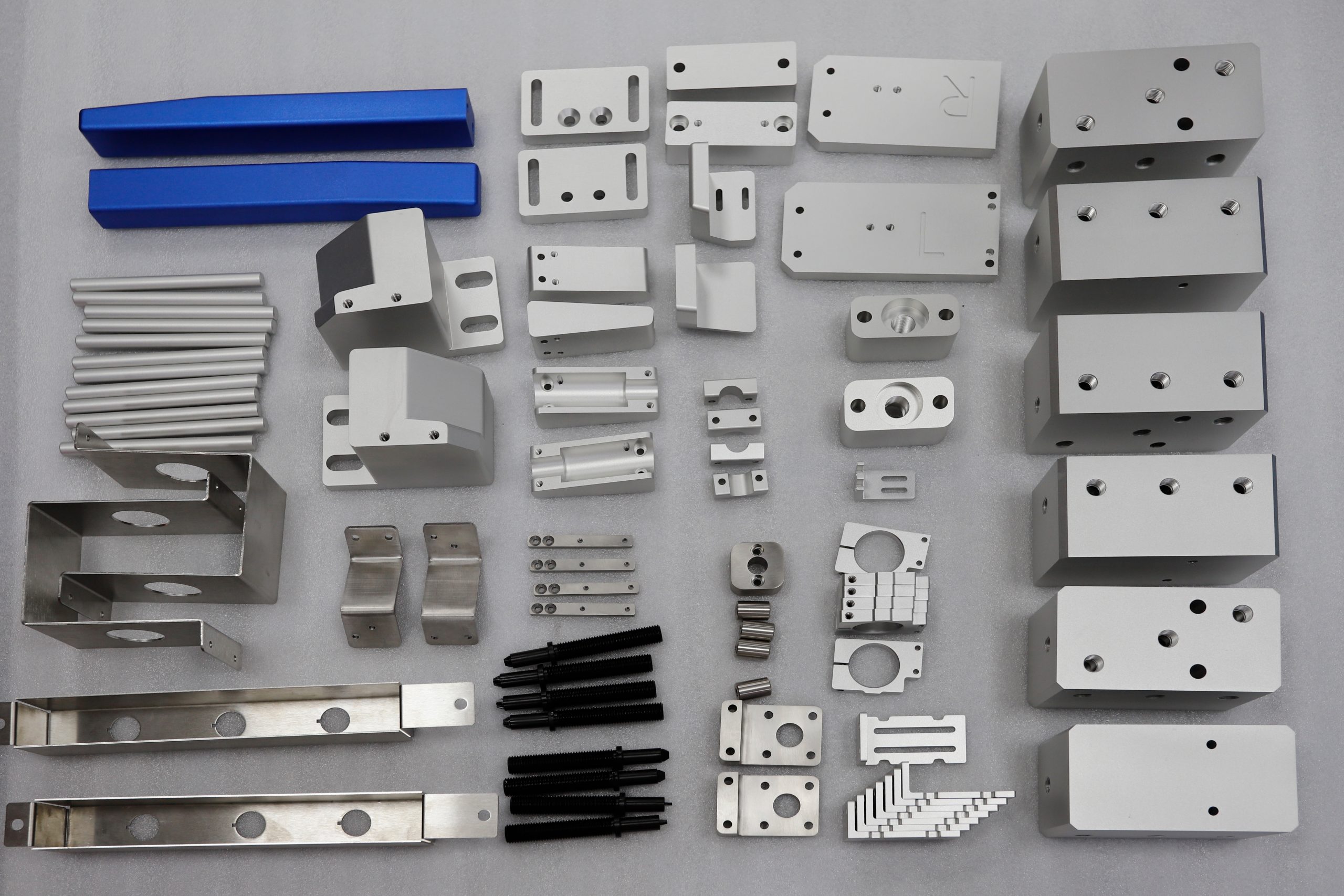
Experienced international team
Quality inspection relies not only on advanced inspection equipment, but also on well-trained technicians with years of experience. As workpieces become more complex and advanced applications place higher and higher tolerance requirements, precision measurement by professionals is the way to ensure accurate product delivery.
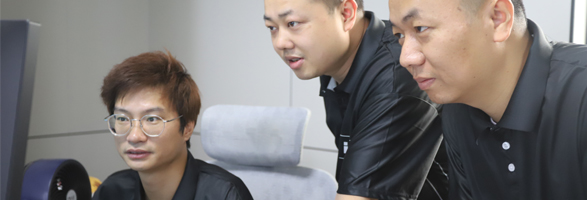
Quality control is essential at every stage of production
To maintain quality from start to finish, HXC provides the following inspection and review services:
- Incoming verification of all processing materials
- Design for Manufacturability review of all quotations
- Contract review after receipt of purchase order
- First article inspection and in-process inspection
- Final inspection and testing with required reports and certificates
ISO certification and quality standards
We are committed to continuous improvement of our industry-leading quality control and quality assurance processes, and for medical products we are fully certified and compliant with ISO 9001:2015, ISO 14001:2015 and ISO 45001:2018, ISO 13485:2016 and ISO/IEC 27001: 2013.
To ensure the highest level of appearance and performance, we perform visual quality inspections under controlled lighting and environmental conditions to confirm appearance according to your specifications. In addition, our injection molding services have established visual quality standards to ensure that our parts are consistent with each other and fully meet your appearance requirements.
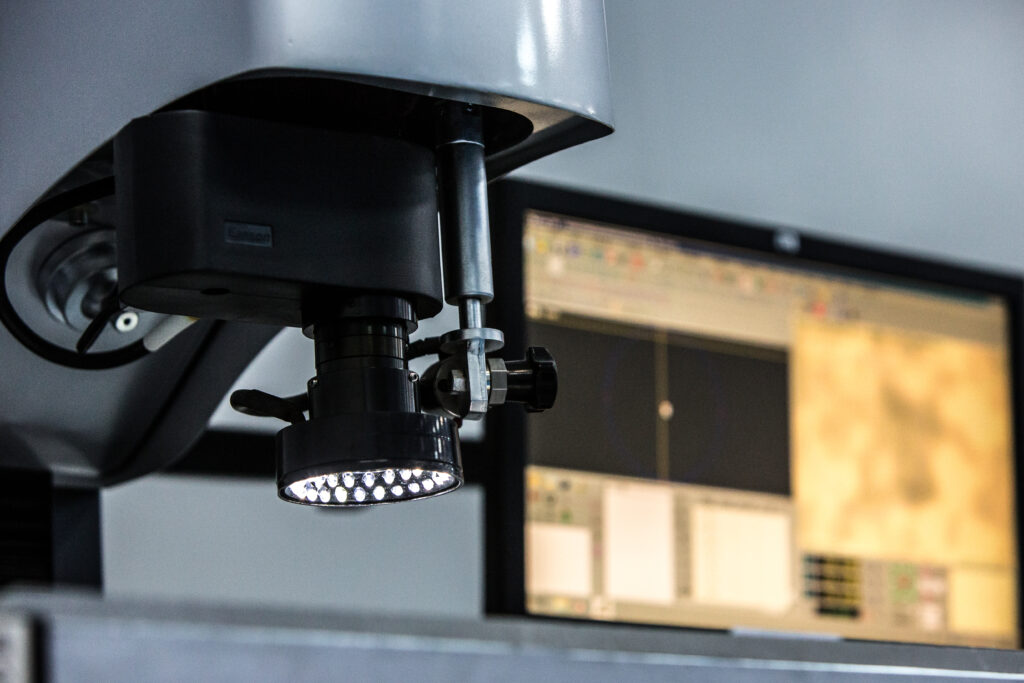
Cutting-edge testing equipment
To carry out our extensive inspections, we use a variety of advanced equipment, including:
- Bruker Alpha II FTIR Spectrometer
- PolyMax Analysis Gun
- Oxford Instruments and Hitachi Optical Emission Spectrometers (OES)
- Oxford Instruments XRF Analyzers
- Zeiss Comet L3D 2 optical scanner
- smart scope zip lite 300
- Nikon Coordinate Measuring Machine (CMM)
- Mitituyo Profilometer
- X-Rite Spectrophotometer
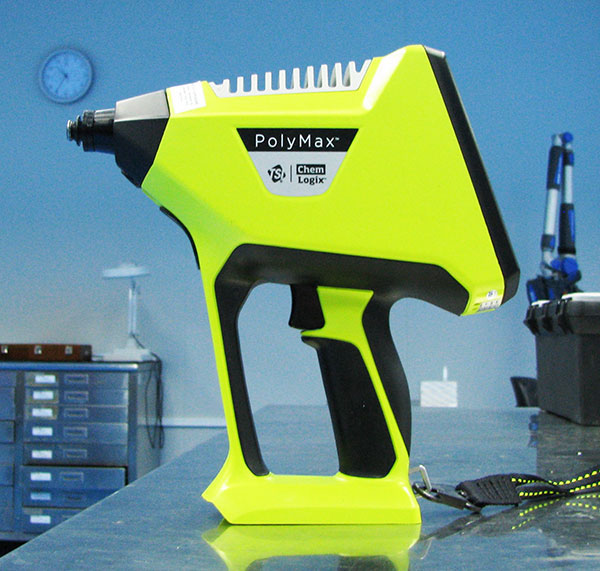
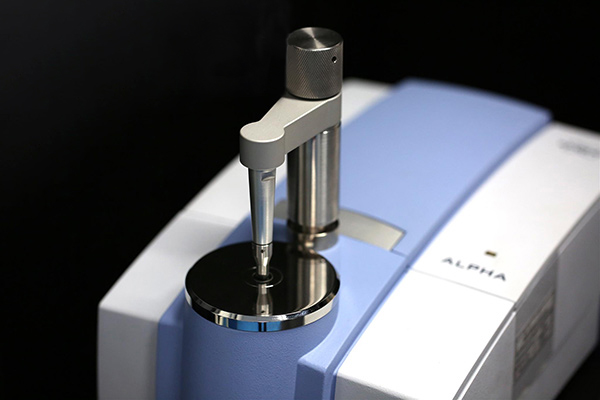
Bruker Alpha II FTIR Spectrometer
The latest addition to our metrology and testing labs, the Bruker Alpha II FTIR spectrometer is used to authenticate incoming materials. With this tester, plastic samples are verified using infrared radiation over a wide spectral band with greater than 97% accuracy. Few other suppliers go to such lengths to ensure that materials meet your exact specifications.
PolyMax Analysis Gun
There are thousands of plastic resins to choose from when making injection molded parts. To ensure we’re using exactly the right resin, we invested in a PolyMax analysis gun. This device sends a laser beam that reflects off the surface of the test sample and reads the unique signature given off by its molecular vibrations. It has a database of hundreds of plastics in its memory and can be programmed with additional plastic types when needed. It’s just another way we stay ahead of the competition by giving you exactly the right material every time.
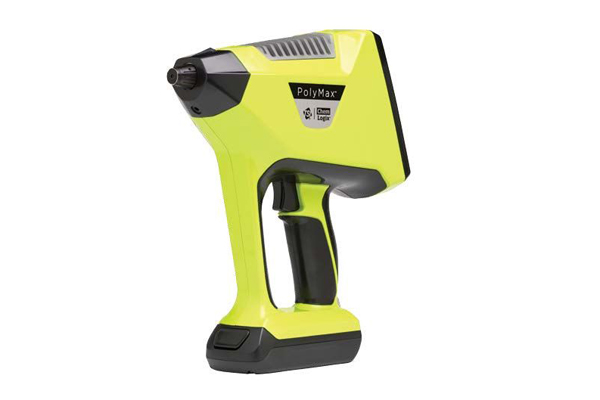
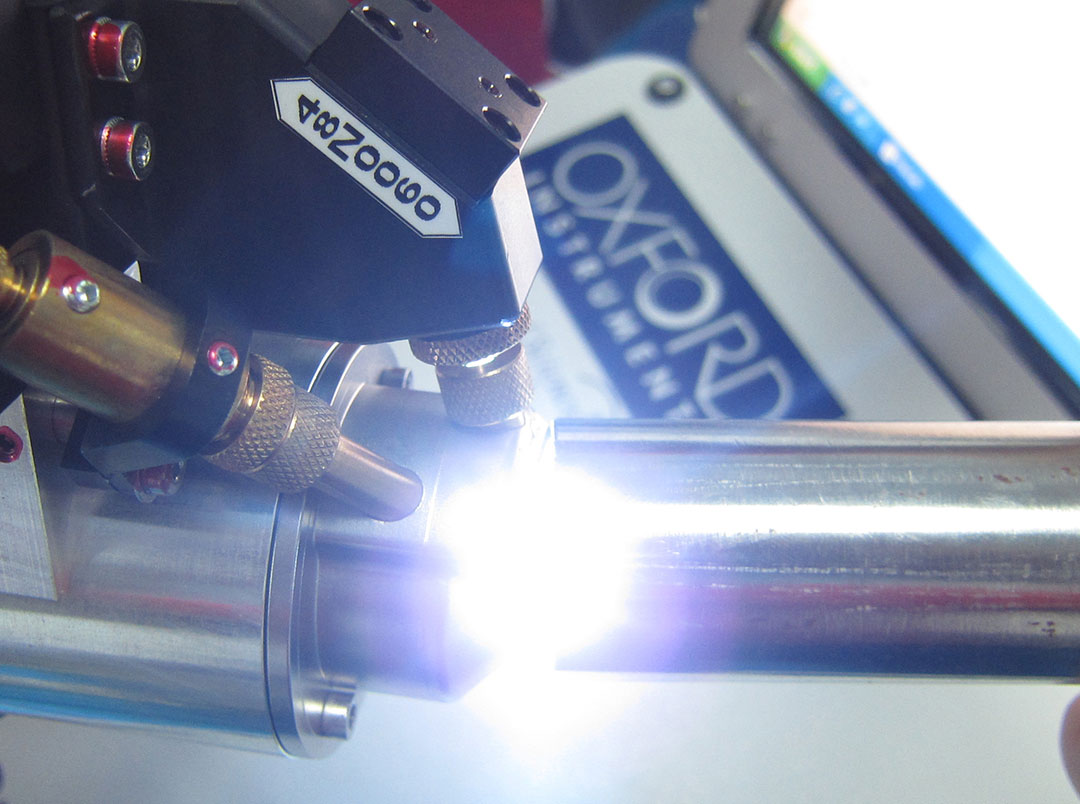
Optical Emission Spectroscopy (OES)
This is a test device that uses an electric current to charge a sample of material. The resulting plasma discharge is unique to each element and this pattern can be read by a spectrometer to determine the complete composition of the metal.
There are many similar alloys and metal grades on the market, some of which are mislabeled or counterfeit. We perform Positive Material Identification (PMI) on all incoming materials, so you can be confident that you are receiving exactly what you ordered. We are one of the few services in China that offers this level of testing.
XRF Analyzers
There are thousands of plastic resins to choose from when making injection molded parts. To ensure we’re using exactly the right resin, we invested in a PolyMax analysis gun. This device sends a laser beam that reflects off the surface of the test sample and reads the unique signature given off by its molecular vibrations. It has a database of hundreds of plastics in its memory and can be programmed with additional plastic types when needed. It’s just another way we stay ahead of the competition by giving you exactly the right material every time.
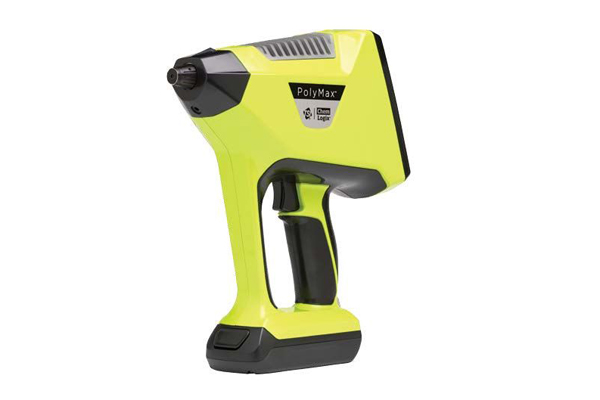
Final product inspection equipment
Using our Zeiss Comet L3D 2 optical scanners, SmartScope ZIP Lite 300, Nikon Ultra CMMs with Renishaw probes, X-Rite spectrophotometers and more, we are able to control manufacturing quality and ensure that the parts we manufacture meet your design specifications. At HXC, the final inspection department is an important part of our ISO certified manufacturing facility. We are committed to continuous quality improvement and respect for our employees and the environment.
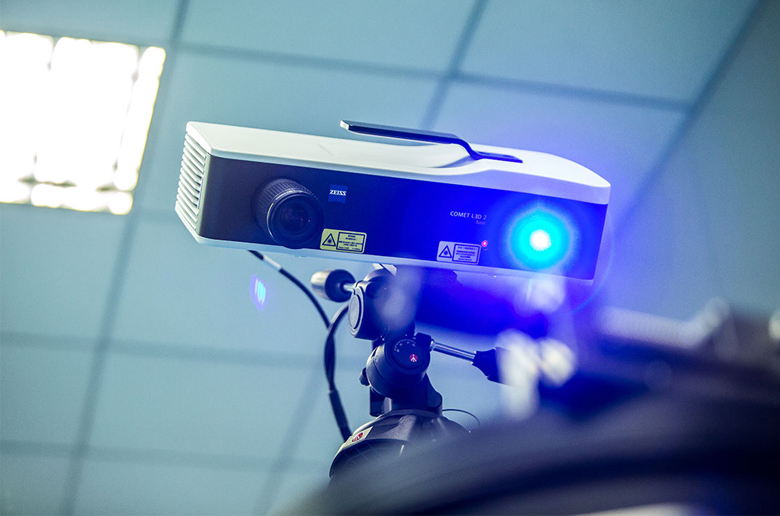
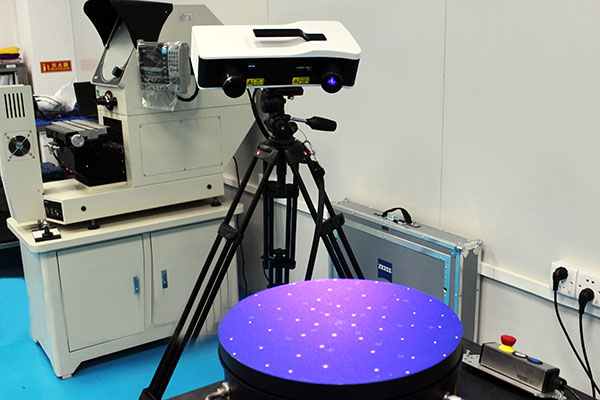
Zeiss Comet L3D 2 optical scanner
The Zeiss Comet L3D 2 optical scanner is a portable, state-of-the-art scanning system for capturing and calculating 3D data quickly and with high accuracy. With easy-to-use software and interchangeable lenses and sensors, the Zeiss Comet can scan up to 5 million data points on workpieces of nearly any size within its wide focal range. It's ideal for verifying part consistency, identifying manufacturing errors, and reverse engineering. It's just part of our commitment to total quality control.
SmartScope ZIP Lite 300
SmartScope ZIP Lite 300 is a non-contact optical measurement system that uses high intensity white LED light to make fast and accurate 2D measurements of parts. High precision mechanical bearings and DC stepper motors mounted on a solid granite base ensure reliable and repeatable accuracy. Combined with sophisticated yet easy to use Measure Mind software, SmartScope can be quickly programmed to run automated measurements of multiple similar shapes.
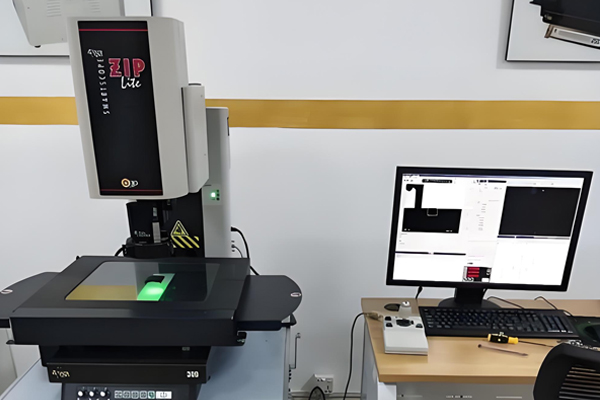
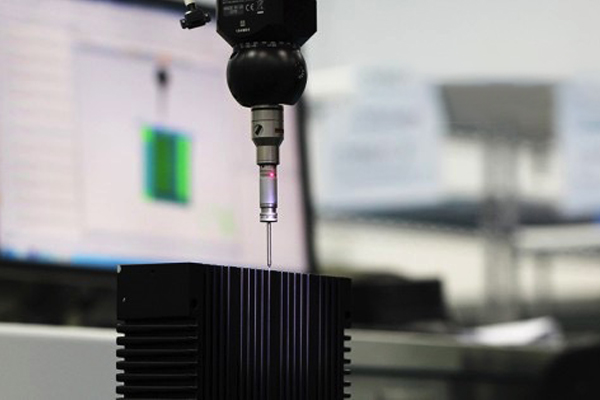
Three-dimensional coordinate measuring machine
At its most basic, a coordinate is a point, a fixed singular position in three-dimensional space. A series of points can be used to define the parameters of a complex shape. Therefore, a coordinate measuring machine (CMM) is any device that can collect this series of points for a given object and do so repeatedly with acceptable accuracy and repeatability.
Surface Roughness Measuring Instrument
We use a Mitutoyo surface roughness tester to measure the surface roughness of items, so we can ensure a specific surface finish is achieved. The equipment is also portable, providing greater convenience for customers.
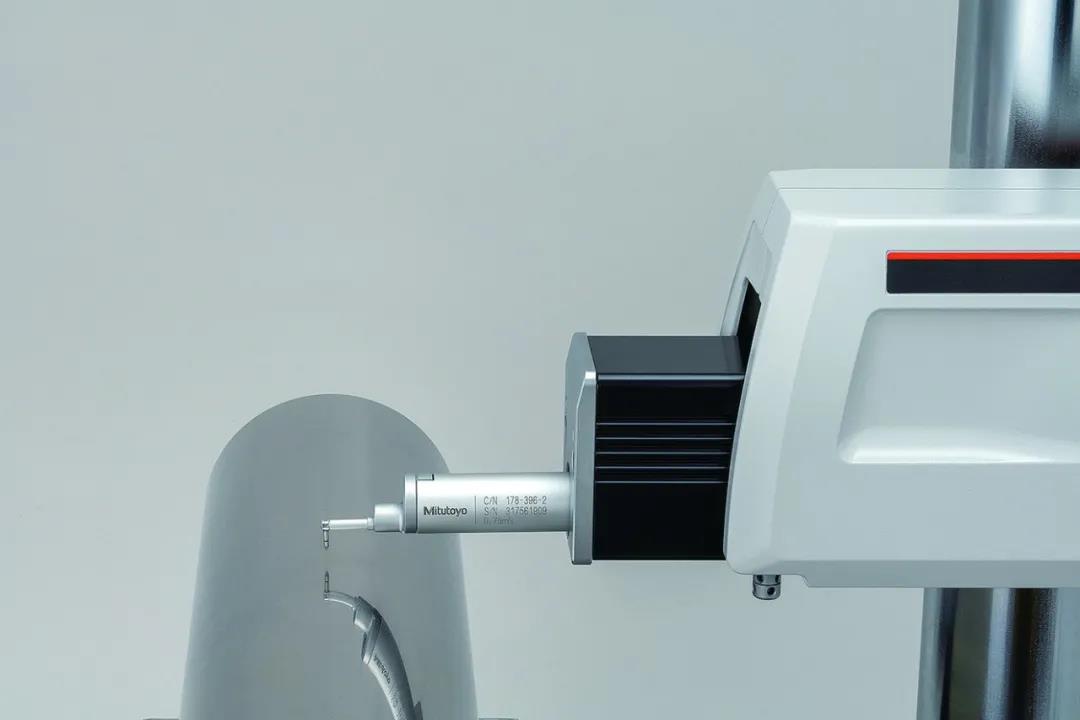
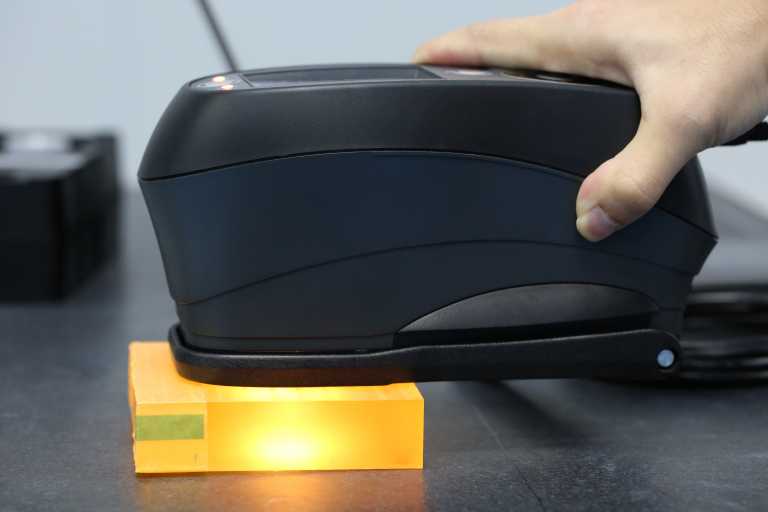
X-Rite Spectrophotometer
An X-Rite spectrophotometer is an analytical device that we use to verify the color of our workpieces. By reflecting a light source off a target surface and comparing it to a standard, we can determine the precise value of your color sample. This information can be sent directly to you for confirmation or used by our production team to monitor and control our manufacturing process to your complete satisfaction.