High precision CNC customization
HXC CNC Machining
HXC's CNC machining factory covers an area of 18,000 square meters. We have over 300 state-of-the-art CNC machines imported from trusted brands such as MAKINO, DMG, Hammer, and Mikron, along with a team of over 200 experienced employees. Therefore, our multi-axis milling capabilities are a highly popular choice across many industries.
We are capable of machining large components with dimensions up to 6000x2500x1000mm. We can provide high-quality precision CNC machined parts for industries with strict tolerance requirements.
Our in-house CMM inspection equipment is manufactured by Zeiss, enabling us to guarantee quality through CMM and FAI reports. The minimum machining size and inspection accuracy is ±0.003mm.
We can process a wide range of foreign materials, including titanium, steel, aluminum, copper, plastics, and other materials. With all the extensive capabilities mentioned above, we can also offer OEM and assembly services.
CNC Machining
HXC provides CNC machining services of any complexity for rapid prototypes and production parts. Start a one-hour CNC quote from a real engineer, and get your parts made as fast as one day.
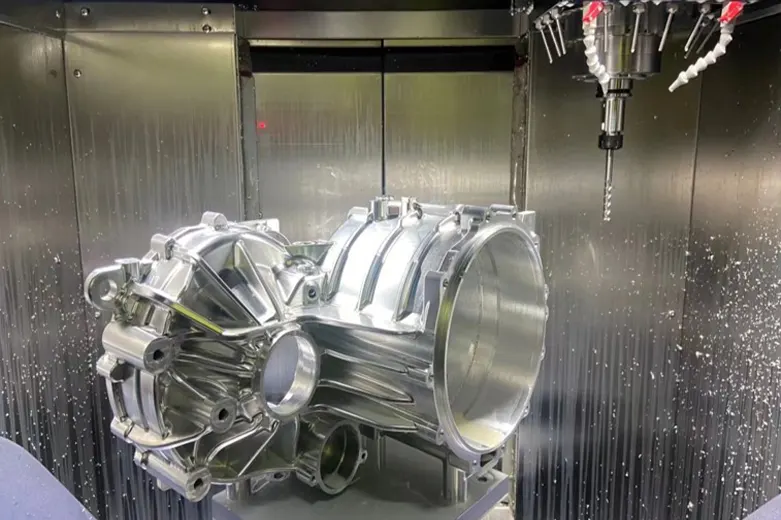
CNC Milling
Our 3-axis, 4-axis, and 5-axis machining is dedicated to producing high-precision products with complex structures. We provide high-quality products for the automotive, aerospace, medical device, robotics, and other industries.
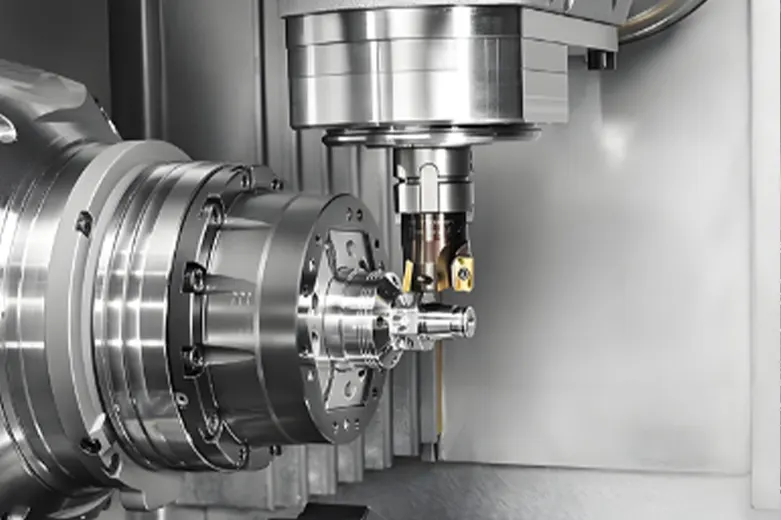
CNC Turning
Using our CNC lathes and turn-mill combo machines, we can manufacture cylindrical, square, or polygonal workpieces. These machines allow for multiple operations to be performed on a single machine, making them ideal for high-precision parts with complex geometries. Prototypes and production parts can be delivered within just a few days.
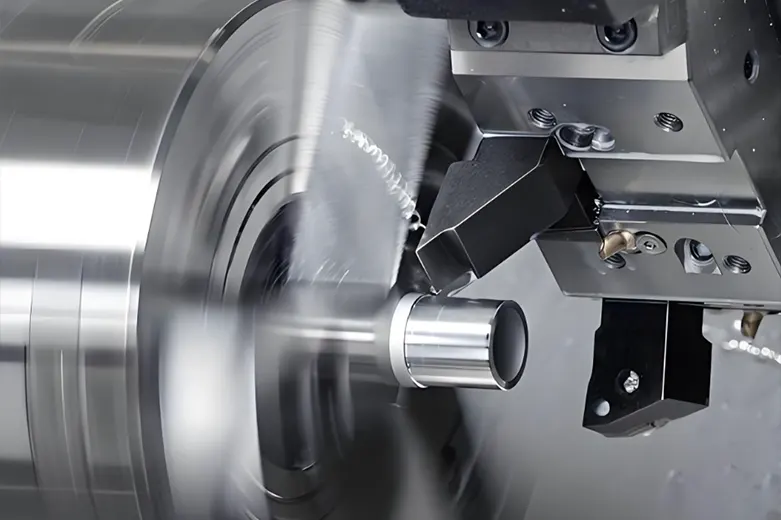
Turning-Milling
Allow multiple operations on a single machine, perfect for high precision parts with complex geometries
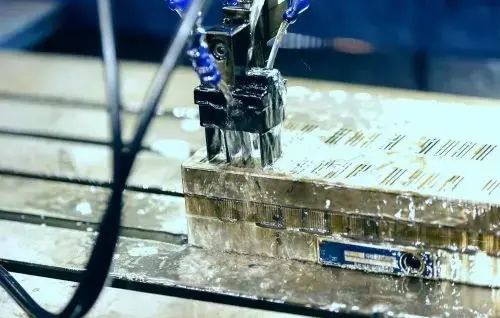
Electrical Discharge
Highly accurate machining service of cutting metal to precise shapes using electricity
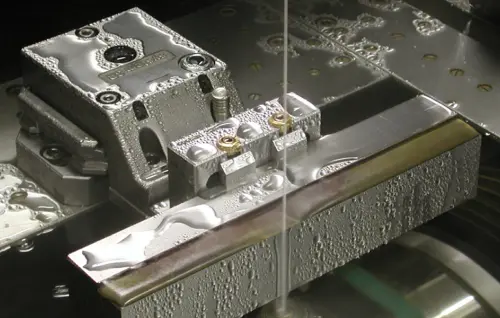
Wire Cut
Our wire cut services can provide high precision tolerances, as tight as ±0.0002″ for an array of industries and applications.
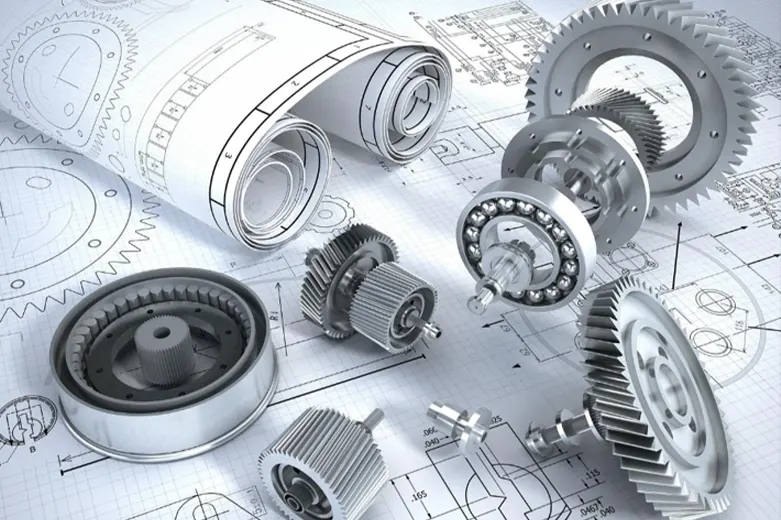
Gear Hobbing
HXC can produce products such as gear hobbing, gear shaping, gear skiving, gear grinding, and gear milling. Our products are widely used in various fields including household appliances, robotics, smart homes, automotive, 5G communications, logistics, printing equipment, and more.
CNC Machining Products
HXC holds the idea that custom-made CNC machining needs consider the product structure design meet the confirm to the rationality and economy of actual manufacturing before CNC machine a new product.
CNC Custom Machining Process
HXC believes that: in the stage of new product development, CNC custom machining is the most considered three points: the economic rationality of the structural design in line with the actual processing, the formulation of the process, the choice of materials and surface treatment, once these three points are effectively confirmed, CNC machining will be no problem, and finally the quality control.
The CNC custom machining process is as follows:
Why did You choose us
Processing Equipment Display
With robust production capacity supported by a scientific production management system, we operate over 300 CNC machines (3-axis, 4-axis, and 5-axis).
Our experienced engineers will combine milling, turning, EDM, wire cutting, surface grinding and many more processes to complete your customized products, parts, small series production. Examples of parts include engine parts, aviation parts, medical instruments, complex machine parts, accessories, etc.
- CNC aviation components
- CNC automotive parts
- CNC molds
- CNC precision parts
- CNC electrical appliances
- CNC robots
- CNC smart furniture
- 5G communication
HXC Processing Advantages
Customer case
- Date
- 2024-11-05
- Date
- 2024-11-05
- Date
- 2024-10-21
- Date
- 2024-10-19