The molding process utilizes the characteristics of silicone rubber, such as high elasticity and high temperature resistance, to accurately and quickly replicate prototypes. It is widely used in fields like automobiles, healthcare, aerospace, electronics and digital products, lighting, etc. Its main advantages include a fast manufacturing cycle, low cost, and performance close to that of injection-molded products. It is suitable for small-batch production, reverse engineering, mold verification, etc., which can shorten the research and development cycle and reduce the R&D costs
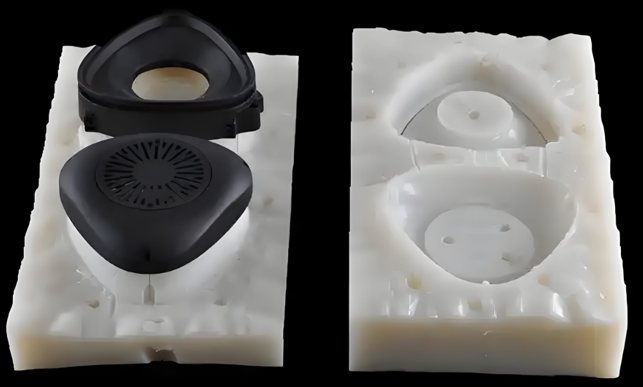
Vacuum Casting
Vacuum casting, also known as vacuum molding. It is a process of degassing, stirring, preheating and casting the casting material under vacuum conditions, and then carrying out a secondary curing and molding process for 2 to 3 hours in a constant temperature oven at 60℃ to 80℃. It is suitable for small-batch trial production during the product development process, and for trial sample parts with relatively complex structures, uniform wall thicknesses and that meet certain functional requirements
this process, a pump or similar device will pull all the air out of the mold.
It offers many advantages over traditional manufacturing methods, including lower costs, faster production times, and the ability to produce complex parts with complex details.
Product Materials:
The casting materials are similar to molding materials such as ABS, ABS+PP, PP, PMMA, etc.
Machining Precision:
The standard replication precision is ±0.20mm/100mm.
Thickness of the Cast Sample:
The optimal thickness is 4-6mm, and the maximum casting thickness is 10mm.
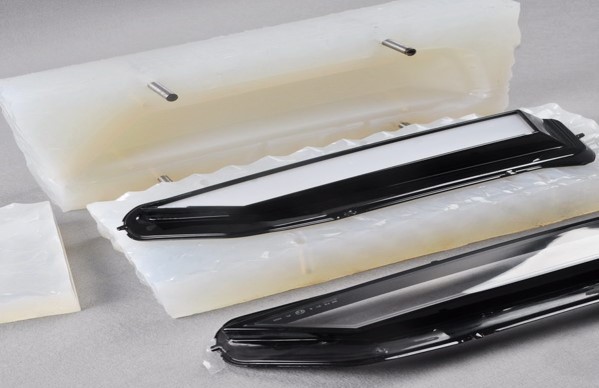
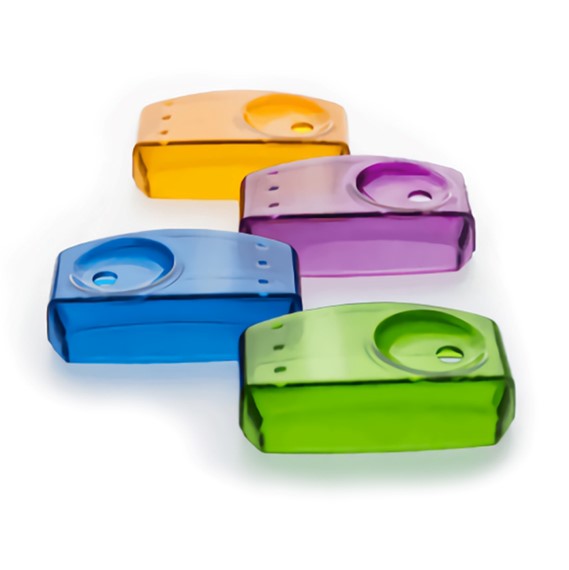
How to Select Vacuum Casting
Product developers should choose to use vacuum casting only when they need to produce a small batch of 10 to 20 pieces with a quality close to that of plastic parts. This can effectively avoid the long lead time and high processing costs associated with manufacturing injection molds. It is well-suited for applications such as reverse engineering and mold verification.
Time Efficiency:
With a prototype available: Sample can be produced within 48 hours.
Without a prototype: Sample can be produced within 72 hours
Advantages of Vacuum Casting
Low mold cost
The mold can be completed within a few days.
Many types of polyurethane resins can be used for casting, including overmolding.
The cast replicas are highly accurate and have excellent surface texture.
The mold is durable and can be used to make 20 copies or more.
It is highly suitable for engineering models, samples, and rapid prototyping
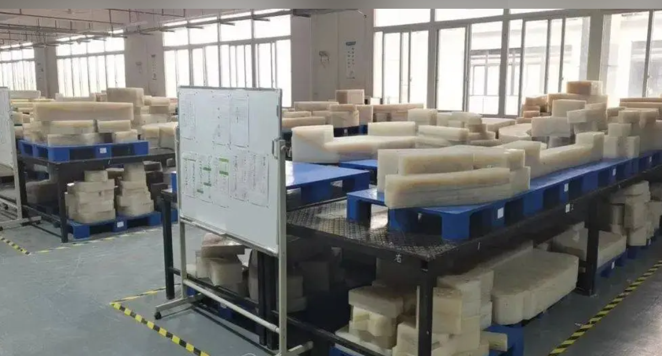
Title: Vacuum Casting Processing Procedure
The production process is divided into four steps in total: preheating of the silicone mold, pre-degassing of the casting material, casting, and curing.
Step 1. Silicone Mold Manufacturing
Preheat the silicone mold to 60-70℃ in advance. When the mold temperature is too low, incomplete curing will occur, resulting in poor physical properties. The mold temperature is directly related to the dimensional accuracy of the trial-manufactured parts.
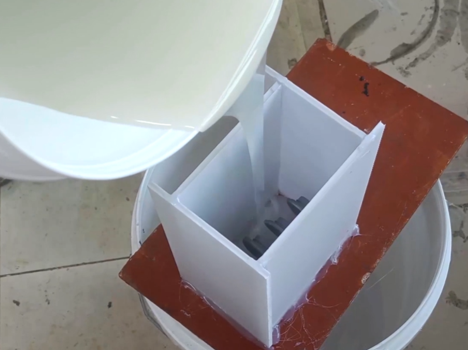
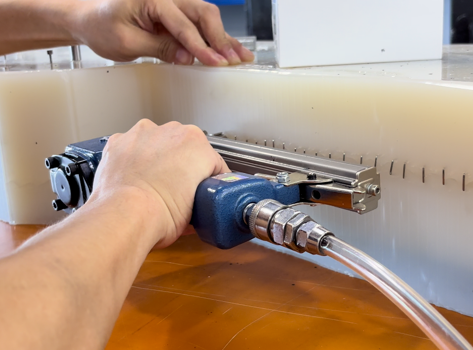
Step 2. Pre-degassing of the Casting Material
Conduct vacuum degassing treatment for more than 30 minutes respectively for the two liquids, A and B, in a vacuum chamber.
Step 3. Casting
Place the containers filled with liquid A and liquid B respectively in the working chamber. After evacuating the working chamber to a vacuum state, stir liquid B from time to time to make it degassed for 5-10 minutes. Pour liquid A into liquid B and stir for 30-40 minutes, then quickly pour the mixture into the silicone rubber mold. And carry out the operation of restoring the atmospheric pressure within 1 minute to 1 minute and 30 seconds starting from the beginning of the mixing.
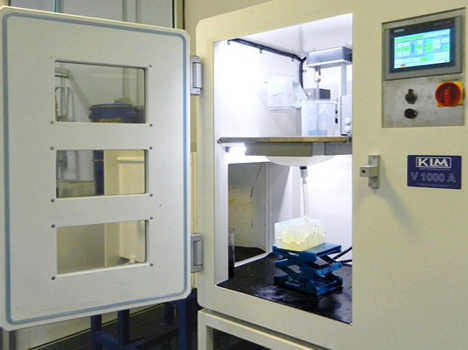
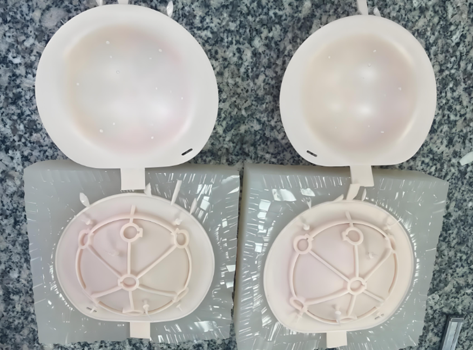
Step 4. Curing
After curing for 30-60 minutes in a constant temperature oven at 60-70℃, the mold can be demolded. If necessary, conduct a secondary curing for 2-3 hours in a constant temperature oven at 70-80℃。
Technical Parameters:
Silicone mold (with a service life of 10 to 100 pieces).
Casting material: Two-component polyurethane PU. Currently used materials: AXSON polyurethane resin, Hei-cast polyurethane resin.
Physical properties: Similar to ABS, PP-like, nylon-like, PMMA/PC-like transparent parts, soft rubber parts (40-90 shore D), high-temperature resistant parts (150℃), fireproof materials, etc.
General working time: 1-4 hours per piece.
Standard replication accuracy: ±0.20mm/100mm.
Thickness of the cast sample: The minimum is 0.5mm, and the optimal range is 1.5mm-5mm.
Maximum cast workpiece: 2000mmX1200mmX1000mm
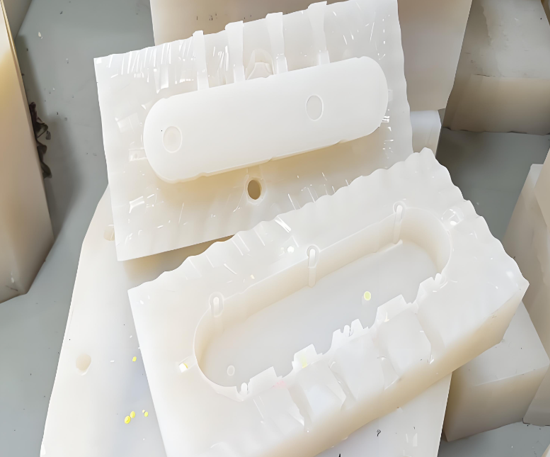
Display of Molding Products
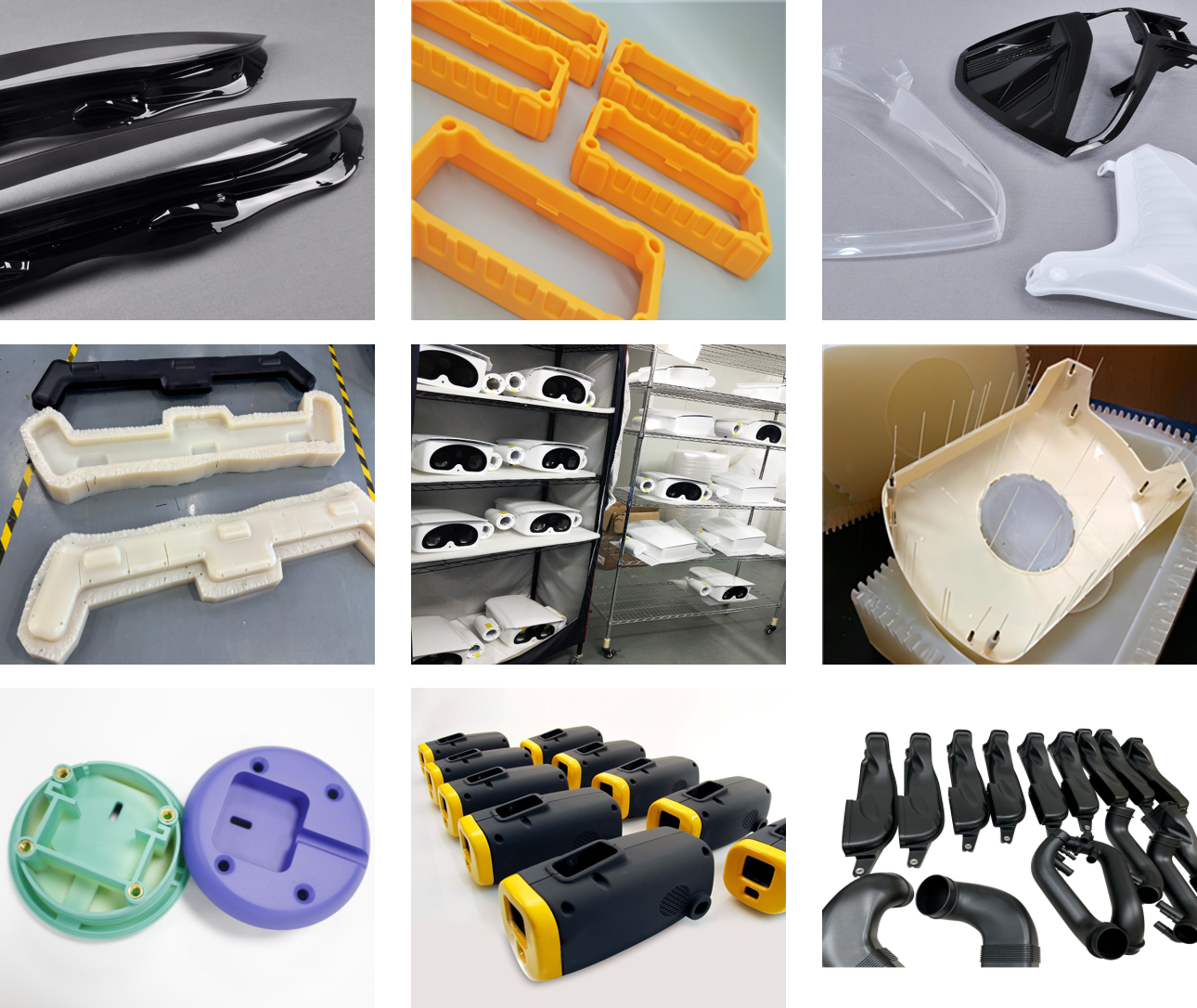
Low-pressure RIM (Reaction Injection Molding)
It refers to a technological process in which two-component materials with high chemical activity and low relative molecular mass are impact-mixed and then injected into a closed mold under normal temperature and low pressure. Chemical reactions such as polymerization, cross-linking, and curing are completed to form the product. This new process that combines the polymerization reaction with injection molding has the characteristics of high material mixing efficiency, good fluidity, flexible raw material preparation, short production cycle, and low cost. It is suitable for the production of large thick-walled products.
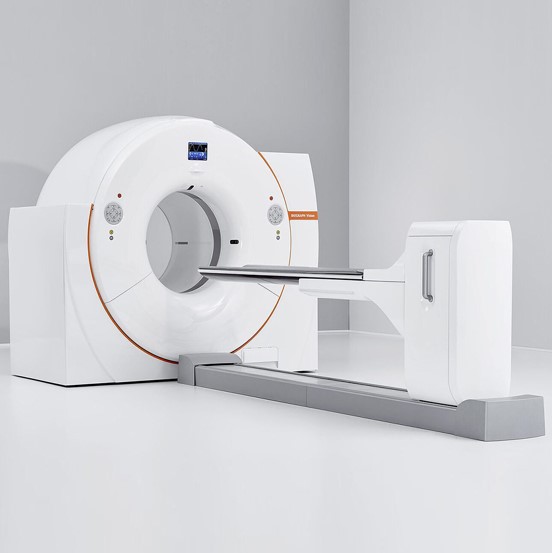
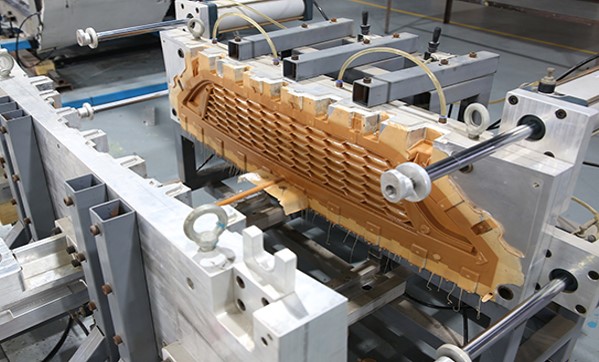
Advantages of Low-pressure Casting
Low-pressure casting has many advantages. These include the ability to rapidly manufacture a large number of parts, high surface quality, a wide variety of resins available for selection, color flexibility, and durable tools that can be used for many years
Common Materials Used in the Molding Process
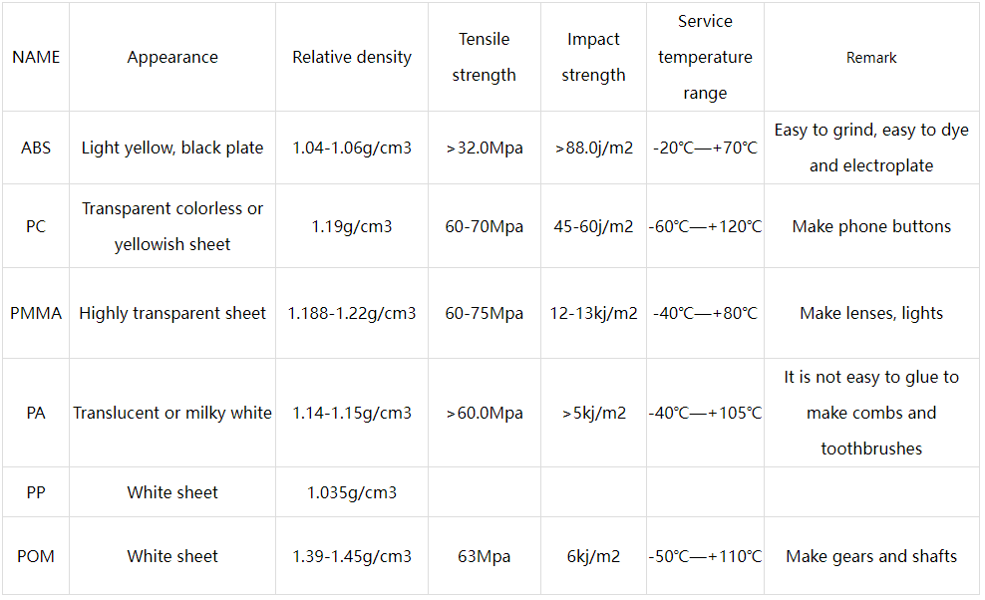
Process Procedure
The RIM (Reaction Injection Molding) process is as follows: Monomers or prepolymers enter the mixing head in a liquid state through metering pumps in a certain ratio for mixing. After the mixture is injected into the mold, it reacts rapidly and crosslinks and cures within the mold. After demolding, it becomes an RIM product.
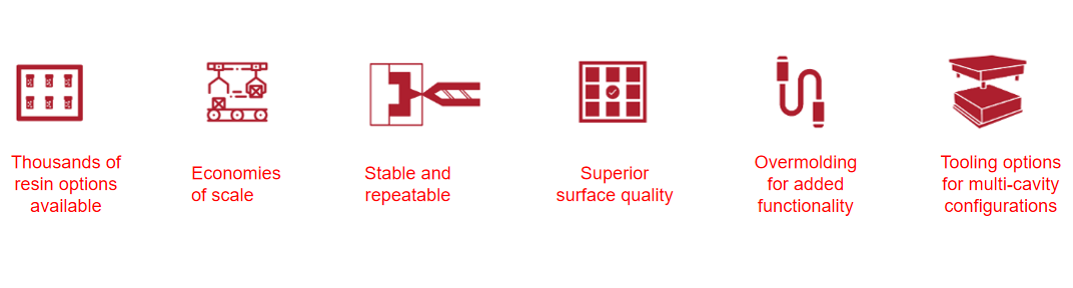
(1) Storage. The two-component stock solutions used in the RIM process are usually stored separately in two storage containers at a certain temperature. The storage containers are generally pressure vessels. When not in the molding process, the stock solutions usually circulate continuously in the storage containers, heat exchangers, and mixing heads under a low pressure of 0.2 to 0.3 MPa. For polyurethane, the temperature of the stock solution is generally 20 to 40°C, and the temperature control accuracy is ±1°C.
(2) Metering. The metering of the two-component stock solutions is generally completed by a hydraulic system. The hydraulic system is composed of pumps, valves, and auxiliary components. During injection, the pressure also needs to be converted to the pressure required for injection through a high-low pressure conversion device. The stock solutions are metered and output by a hydraulic quantitative pump, and the metering accuracy is required to be at least ±1.5%, and it is preferably controlled within ±1%.
(3) Mixing. In the molding of RIM products, the quality of the products depends largely on the mixing quality of the mixing head, and the production capacity completely depends on the mixing quality of the mixing head.
(4) Mold Filling. The characteristic of the reaction injection material filling the mold is that the flow rate of the material is very high. For this reason, the viscosity of the stock solution is required not to be too high. For example, the viscosity of the polyurethane mixture during mold filling is about 0.1 Pa.s. Flow control: 600g/s.
(5) Curing. The two-component polyurethane mixture has high reactivity after being injected into the mold cavity and can complete the curing and shaping in a very short time. However, due to the poor thermal conductivity of plastics, a large amount of reaction heat cannot be dissipated in a timely manner. Therefore, the internal temperature of the molded product is much higher than the surface temperature, causing the curing of the molded product to proceed from the inside to the outside. ,the heat exchange function of the mold should be fully utilized to dissipate heat. The curing time in the reaction injection mold is mainly determined by the formulation of the molding material and the size of the product. In addition, the reaction injection products need to undergo secondary thermal curing after being demolded from the mold
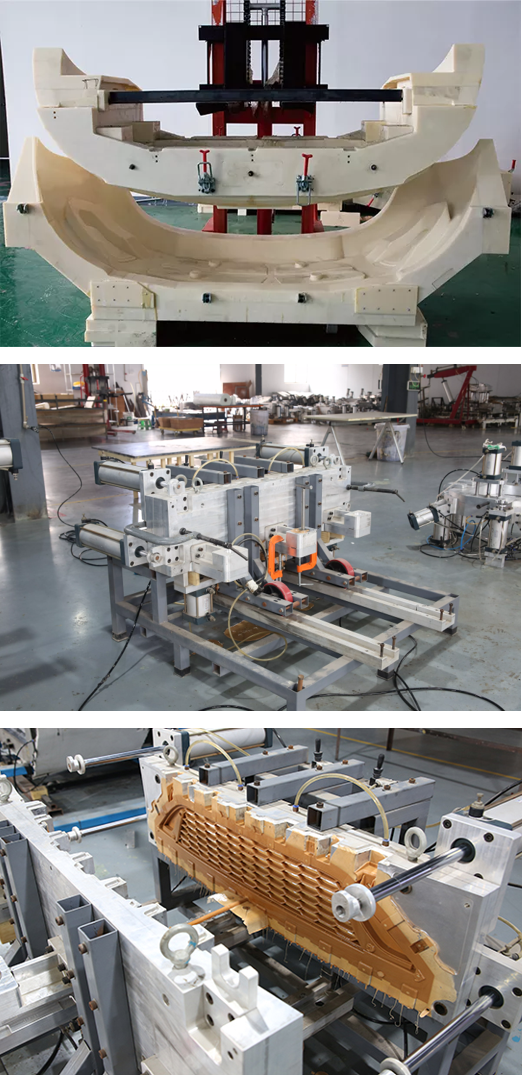
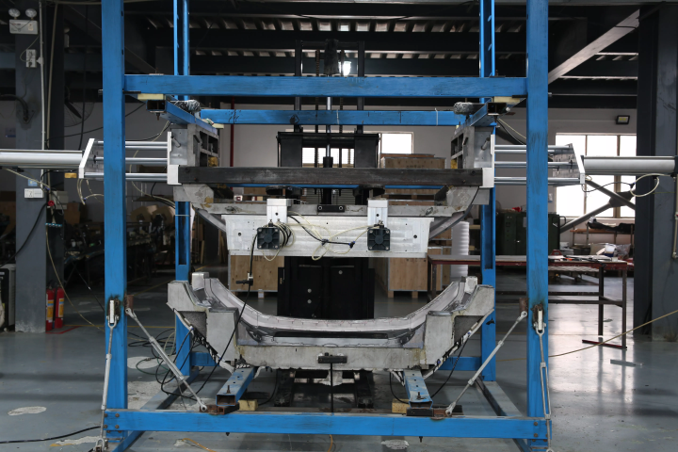
Technical Parameters:
Applicable Molds: Resin molds (more than 100 pieces); ABS molds (more than 300 pieces); Aluminum alloy molds (more than 1,000 pieces).
Casting Material: Two-component polyurethane PU. Currently used materials: HD-PU4210, DCP-RIM, AXSON-RIM 875.
Physical Properties: Similar to PP/ABS. The products have the characteristics of aging resistance, strong impact resistance, high fitting degree, easy loading and unloading, etc.
Injection Pressure: Approximately 10MPa. Flow Control: 600g/s.
General Working Time: 15-30 minutes per piece. The demolding temperature can be controlled below 40°C. After demolding, the parts can achieve the best performance when cured in an environment of 80°C for 2-4 hours
Display of RIM Automotive Products
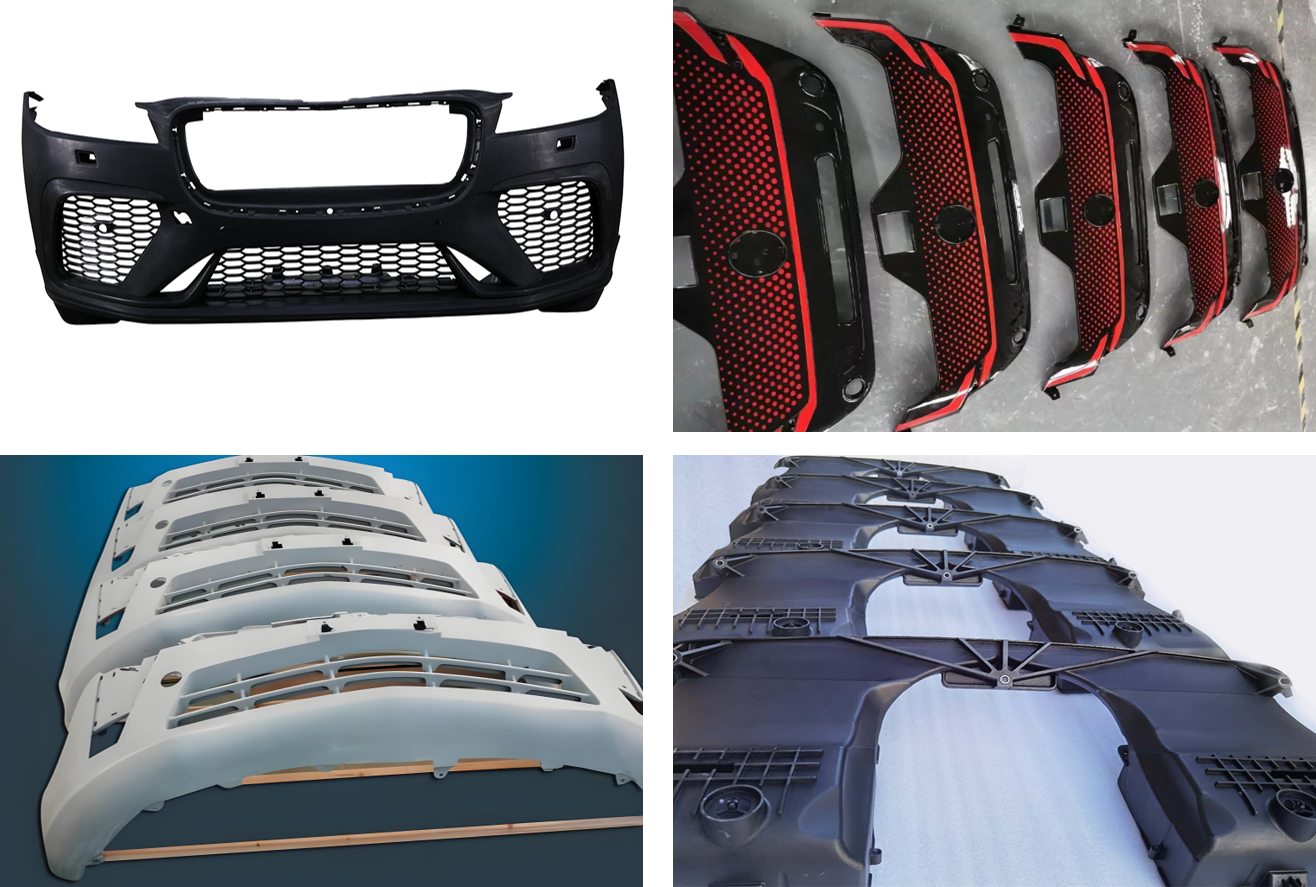
Display of RIM Other Products
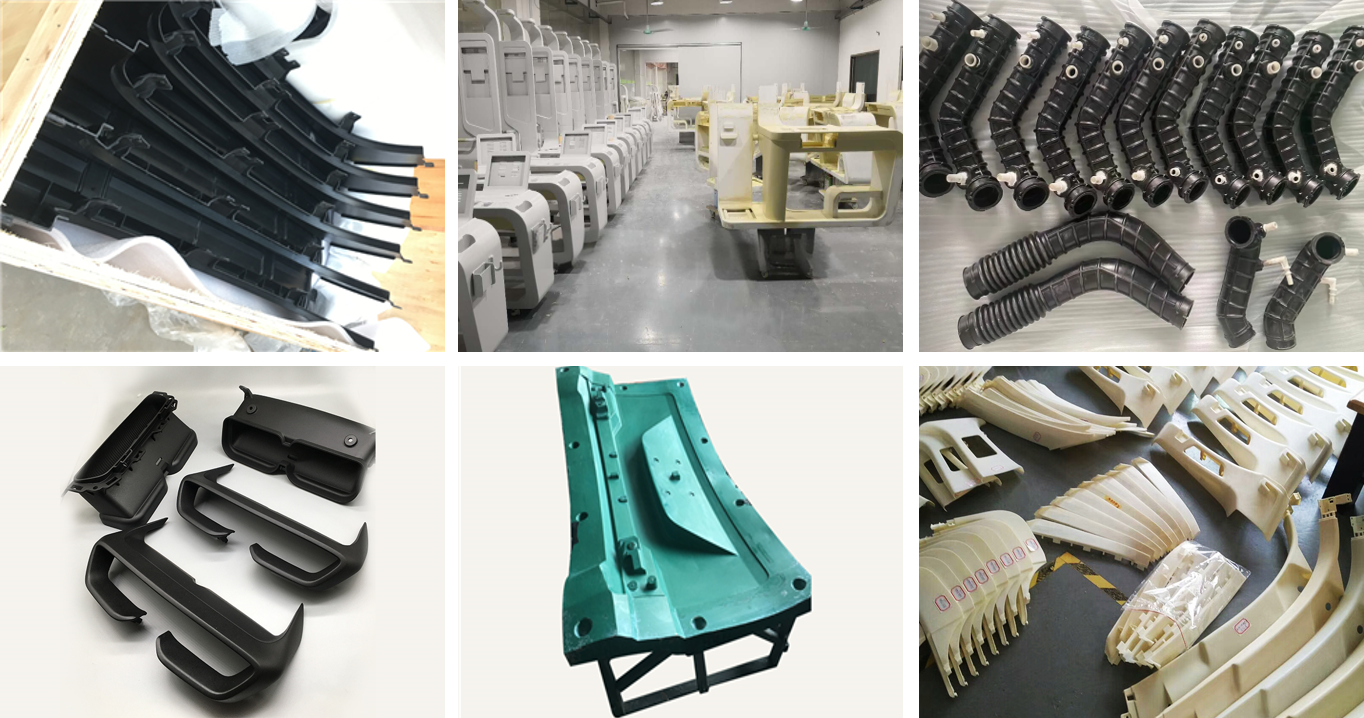
Detection Equipment
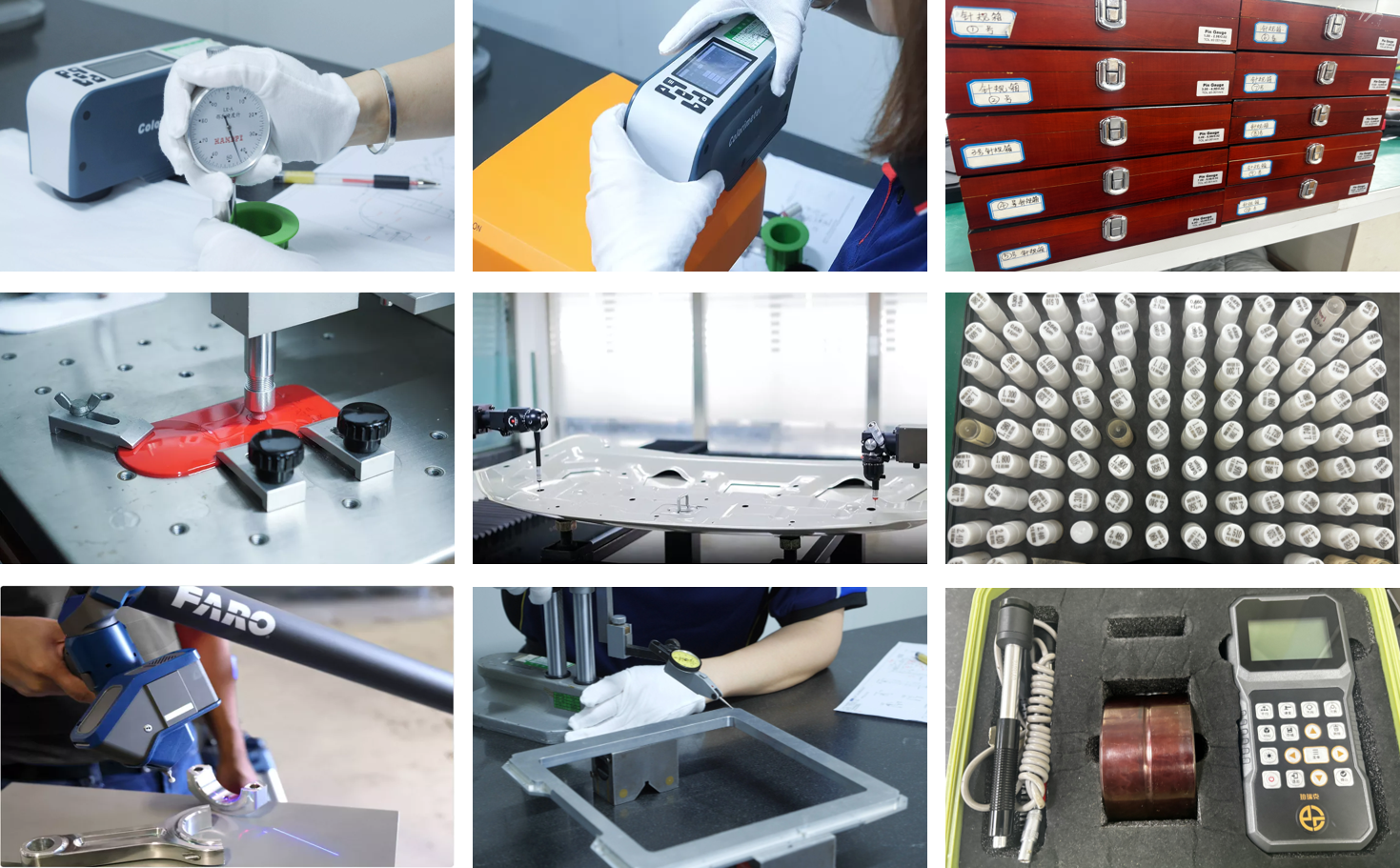
How to Choose between Vacuum Casting and Low-pressure Casting (RIM)
When choosing between vacuum casting and low-pressure casting (RIM), it is necessary to comprehensively consider factors such as product requirements, production scale, and cost budget. The following are the core differences between the two and their applicable scenarios:
1:Vacuum Casting
Process Features:
Using a silicone mold, degassing and casting are carried out in a vacuum environment, and secondary curing is performed for molding.
The mold cost is low and the production cycle is short (completed within a few days), but the service life is limited (about 20-30 pieces).
It is suitable for small-batch trial production of parts with complex structures and uniform wall thickness.
Applicable Scenarios:
Small-batch production (such as 10-20 pieces), used for product development verification or short-term needs.
Complex structural parts (such as automotive interior components, medical device housings, and robot parts).
Parts that require soft rubber or special surface treatment (such as painting and electroplating).
Manufacturing Cycle:
Generally, when there is a prototype, we will provide qualified samples within 48 hours. When there is no prototype, the time to provide samples will not exceed 72 hours.
Advantages:
Quickly respond to design changes and reduce the cost of trial and error.
It can replicate high-precision prototypes, and the surface quality is close to that of injection-molded products.
2:Low-pressure Casting (RIM)
Process Features:
Using resin, ABS, or aluminum alloy molds, two-component polyurethane materials are mixed and cured under low pressure.
The mold has a long service life (more than 100 pieces for resin molds and more than 1,000 pieces for aluminum alloy molds), making it suitable for medium-batch production.
It has high production efficiency, excellent surface quality, and can realize the molding of large thick-walled products.
Applicable Scenarios:
Medium-batch production (100-1,000 pieces), such as automotive parts, home appliance casings, fitness equipment, etc.
Simple-structured but high-strength cover parts or large parts (such as medical device housings).
Materials that require special properties (such as high-temperature resistance, fire resistance, and impact resistance).
Advantages:
The cost is lower than injection molding, making it suitable for the production of large parts when the mold opening quantity has not been reached.
It supports the selection of a variety of resins, and the product has stable dimensions and small deformation.
Manufacturing Cycle:
This depends on the complexity of the tool design and the type of material used to manufacture the tool. If the product structure is simple and the material is P20, we can control the manufacturing cycle within one week. For hard steel materials or materials that require heat treatment, the cycle usually does not exceed 15 working days. And complex shapes or advanced surface textures may take three weeks