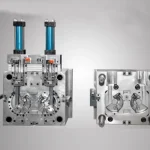
HXC Bending Tube Core-Pulling Mold
2024-10-15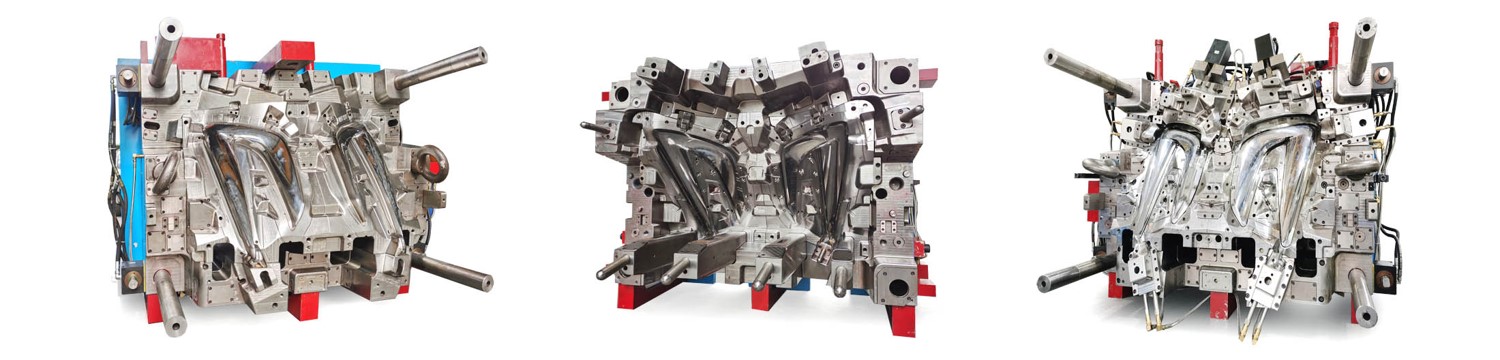
Tooling & Injection Molding
With over two decades of industry leadership, HXC specializes in advanced tooling solutions including two-color, multi-material, overmolding, and insert molding (plastic/metal hybrid). Our vertically integrated workflow covers design, precision tooling, high-volume molding, and quality assurance, supported by state-of-the-art metrology systems.
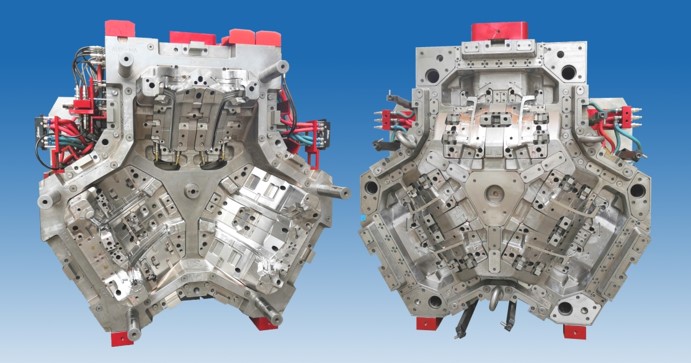
Cases of Multi-color Automotive Molds
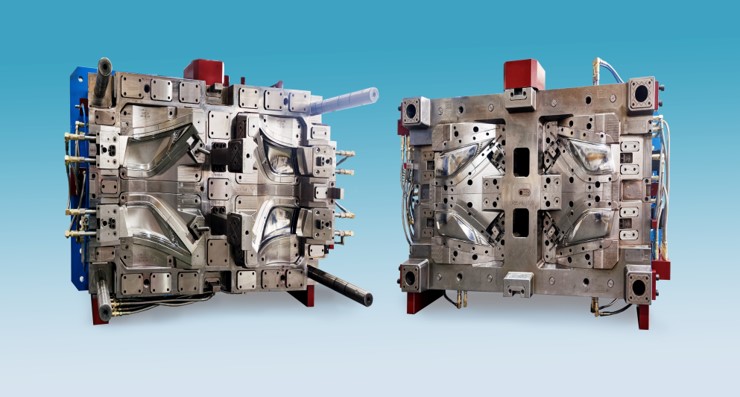
Mold type:Automotive HL Lamp
Mold name:Rear Combo Lamp Housing Mould
Mold life:Five Hundred Thousand Sets
Mold type:Automotive HL Lamp
Mold name:2K Flat Light Guide Mould
Mold life:Five Hundred Thousand Sets
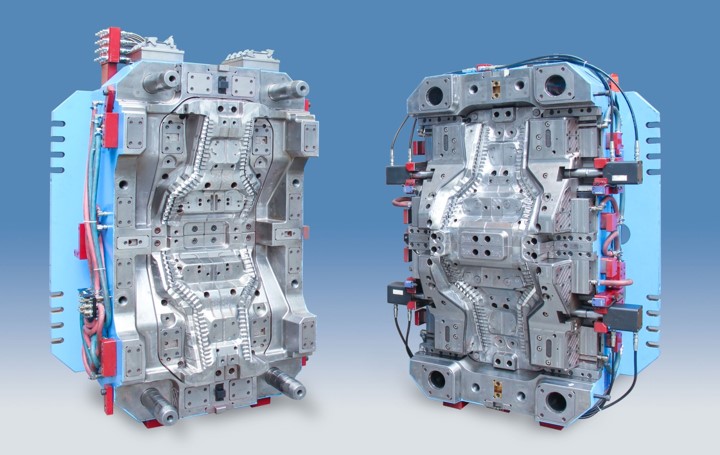
Mold type:Automotive HL Lamp
Mold name:3-Color 3-Position Mould
Mold life:Five Hundred Thousand Sets
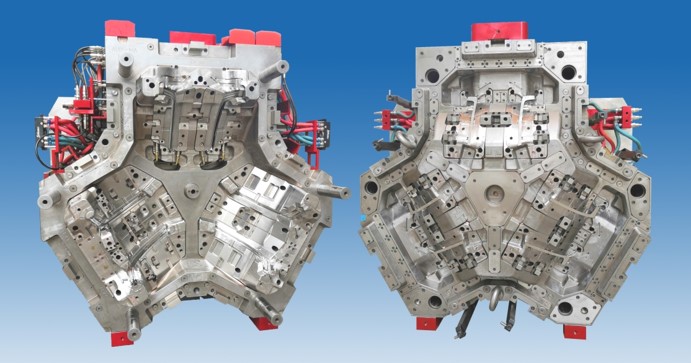
Cases of Multi-color Automotive Products
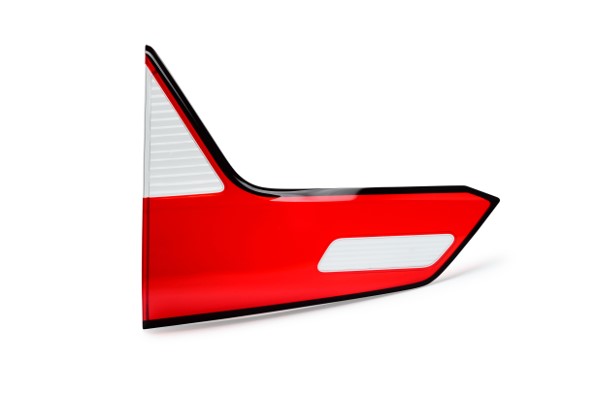
Lamp:RCL Lens
Name:Automotive Lighting
Color:3-Color
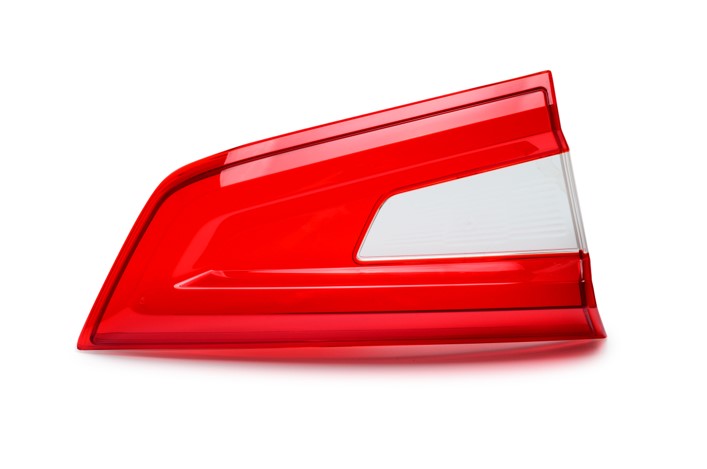
Lamp:RCL Lens
Name:Automotive Lighting
Color:Bi-Color
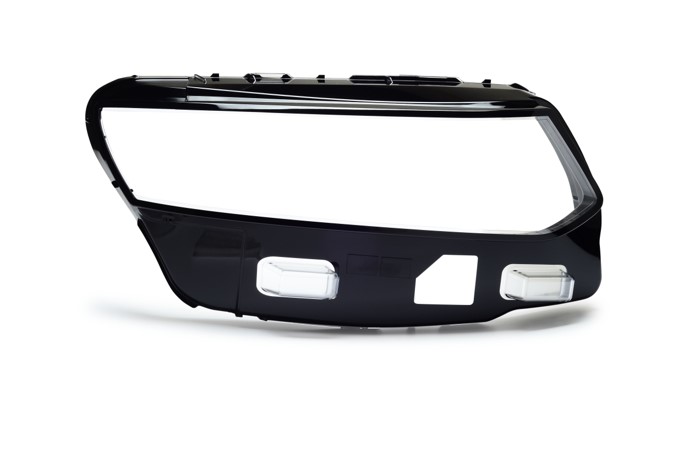
Lamp:HL Lens
Name:Automotive Lighting
Color:Bi-Color
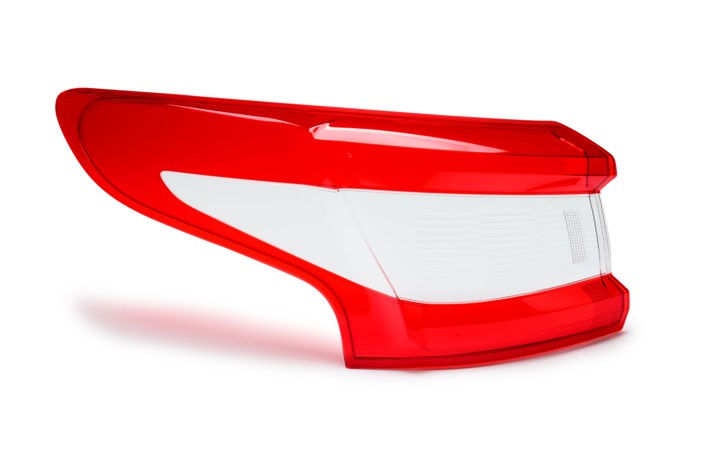
Lamp:RCL Lens
Name:Automotive Lighting
Color:Bi-Color
Special production equipment for two-color processes
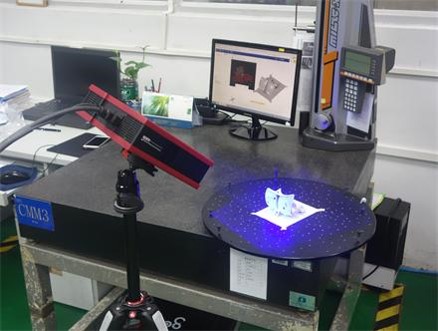
Blue light scanner
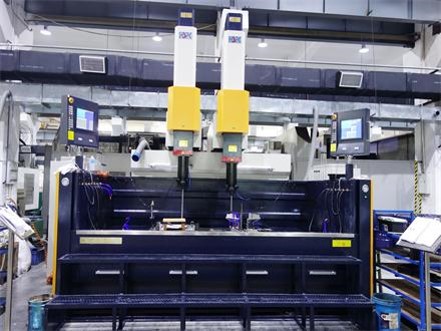
Double-head EDM Machine
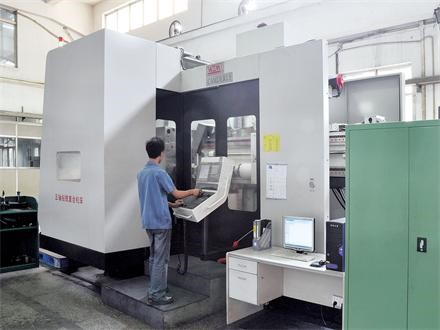
CNC Drilling and Milling Composite Machine Tool
Unique production equipment for multi-color products
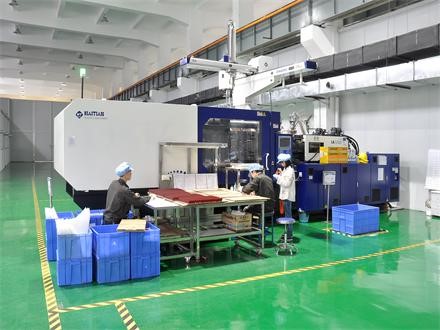
530T 2K Injection Molding Machine
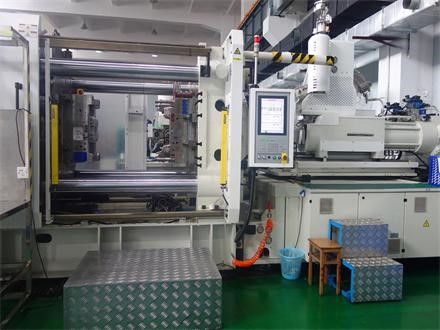
Thick-walled 2K Injection Molding Machine
Exhibition of Other Industrial Multi-color Products of HXC
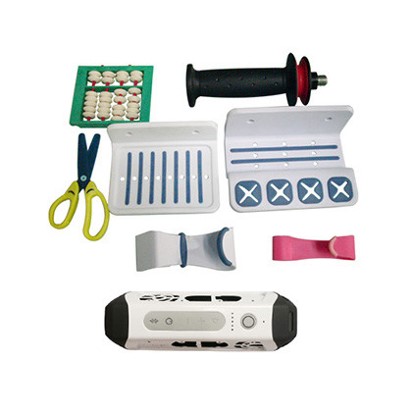
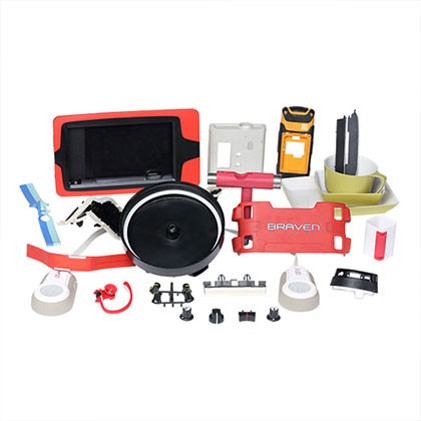

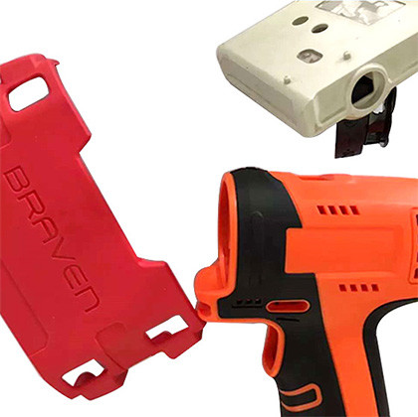
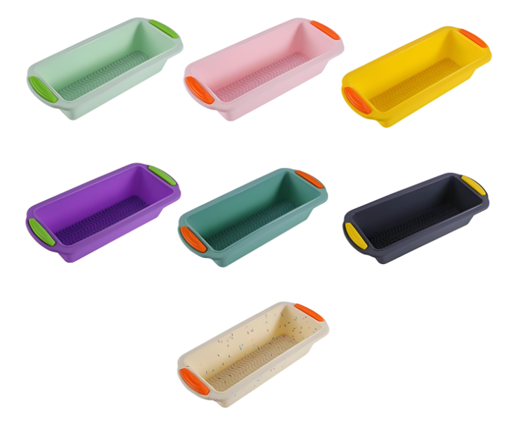
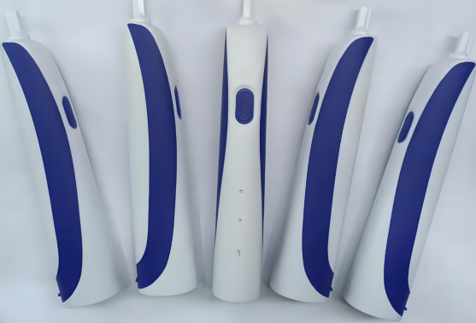
Ten Critical Injection Molding Considerations for 2K Mold Design
Two distinct cavity inserts form individual product components, while the two core inserts maintain identical geometry.
The cavity side must rotate 180 degrees concentrically and achieve precise alignment with the core.
Verify machine specifications including maximum/minimum mold height, ejector pin spacing, and clamping force during design.
Three-plate tooling requires self-ejecting nozzle systems, with special attention to reliable ejection of flexible material nozzles.
Design clearance reliefs in the second-shot cavity to prevent damage to the first-shot component. Rigorously evaluate shutoff area integrity to avoid flash risks under high injection pressure.
Slightly oversize the first-shot component to ensure tight cavity registration during the second injection, enhancing sealing effectiveness.
Prevent melt flow from displacing the first-shot component during the second injection, which could cause dimensional distortion.
Implement balanced and uniform cooling channel layouts for both cavities and cores.
Given the deformation risks of flexible materials, 99% of applications involve molding rigid components first followed by flexible overmolding.
Optimize material adhesion through compatible resin selection (e.g., specialized TPU grades) and controlled mold surface finishes - smoother surfaces enhance bond strength.