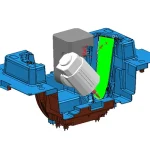
Agricultural deep cavity mold solution
2025-02-25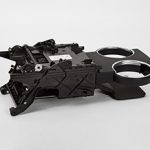
Automobile interior parts mold wholesale case
2025-03-04Sheet metal stamping/bending/drilling
Many products rely on the use of metal sheets to make housings, brackets, mounting plates, and other accessories made of steel and aluminum.
Includes bending, stamping, cutting standard metal for hand plates and small series production, and can be used in series or alone.
Manufacture custom sheet metal parts, such as brackets, plates, frame arms, busbars, jigs, etc.
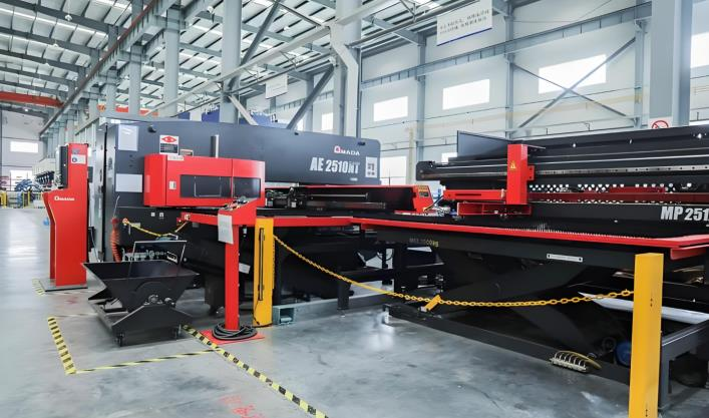
Commonly Used Sheet Metal Materials
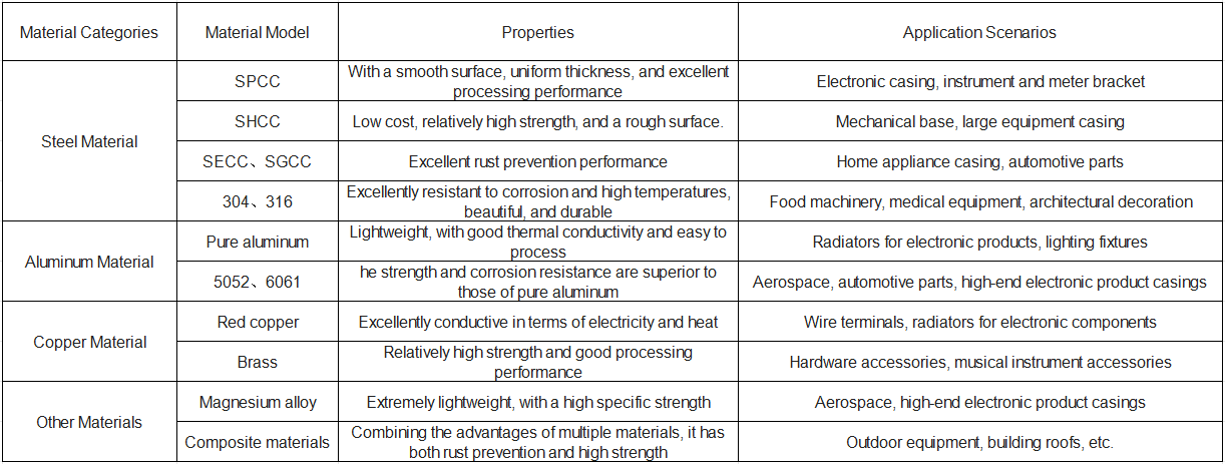
Five Major Advantages of Sheet Metal
Customization
There are various choices of materials, finishes and thicknesses to meet customized requirements, and your orders will be delivered on time.
Durability
Sheet metal can be formed into a variety of shapes. It creates a very durable surface for prototyping or final use.
Economy
Sheet metal is light in weight, high in quality and efficient. It is also very cost-effective because the low installation cost means a lower price, especially for large quantities.
Accuracy
Sheet metal projects can be completed using modern technologies. Sheet metal works well with presses that allow for precise measurements.
Fast Cycle
Fast turnaround with parts delivered within 4 to 10 days.
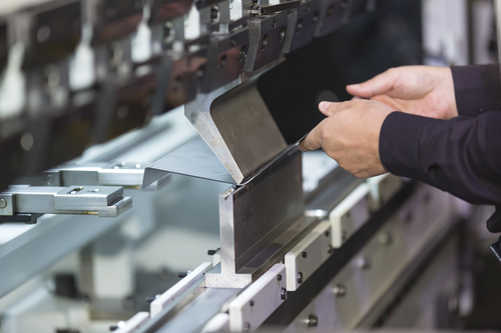
Advantages of HXC Sheet Metal Fabrication
High-precision machining capabilities
HXC is equipped with advanced CNC equipment, including (such as CNC punching machines, laser cutting machines, bending machines, etc.), which can achieve millimeter-level precision machining. It can ensure the dimensional consistency and structural stability of parts, meeting the stringent precision requirements of high-end equipment and precision instruments.
Diverse material compatibility
HXC supports the processing of various metal materials, including carbon steel, stainless steel, aluminum alloy, copper alloy, etc. Materials with different strength, corrosion resistance, or electrical conductivity can be selected according to project requirements. Surface treatments (such as galvanizing, spraying, anodizing, etc.) are also provided to enhance the appearance and performance of products.
Efficient production and flexible customization
HXC's sheet metal processing technology is suitable for mass production. The automated production line can shorten the processing cycle. Meanwhile, it has the ability to quickly make samples, meeting the full - process needs of customers from prototype development to large - scale production.
Cost optimization and high cost - effectiveness
Sheet metal processing has a high material utilization rate, and automated equipment reduces labor costs, which is particularly advantageous in mass production. The lightweight design combined with high - strength materials can reduce material consumption while ensuring performance, further enhancing economic efficiency.
Strict quality control system
HXC has passed the ISO quality management system certification and implements strict monitoring throughout the production process (from material warehousing to finished product inspection). A three - coordinate measuring instrument is used to detect dimensional accuracy, and salt spray tests, adhesion tests, etc. are conducted to ensure the quality of surface treatments, guaranteeing the reliability and service life of products.
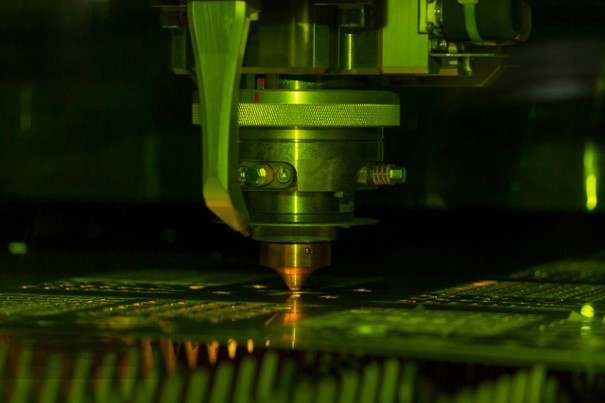

Common surface treatments for HXC sheet metal
Fine machining
The machining marks on the surface of the parts are not visible, and the periphery of the parts is smooth without burrs.
Standard
The sheet metal fabricated parts remain as fabricated parts. There will be visible mold marks on the parts.
Sandblasting
It is a surface smoothing operation, which involves directing fine glass beads at the surface of the parts under high pressure. Sandblasting produces a smooth and uniform surface finish on the parts.
Galvanization
Galvanization is a type of zinc plating, which involves applying a thin layer of zinc metal onto the surface of another metal through a process called electrodeposition.
Powder Coating
Conductive metal parts can be coated with colored powder coating after fabrication to provide a surface finish that dries, melts and hardens. It is very suitable for workpieces that require textures that may not be achievable with wet coating.
Chrome Plating
This involves depositing a thin layer of chromium onto the metal component through an electroplating process. The chromium layer can serve a decorative purpose, make the parts corrosion-resistant or improve the surface hardness. Depending on the material and application of the end-use component, a range of customized finishes can also be provided for your parts.
Customization
Depending on the material and application of the end-use parts, you can also provide a range of customized finishes for your parts
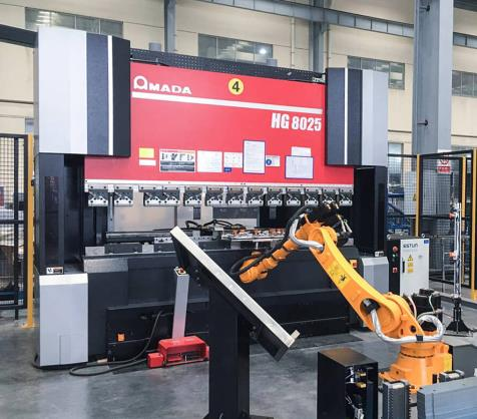
Exhibition of Commonly Used Surface Treatment Products
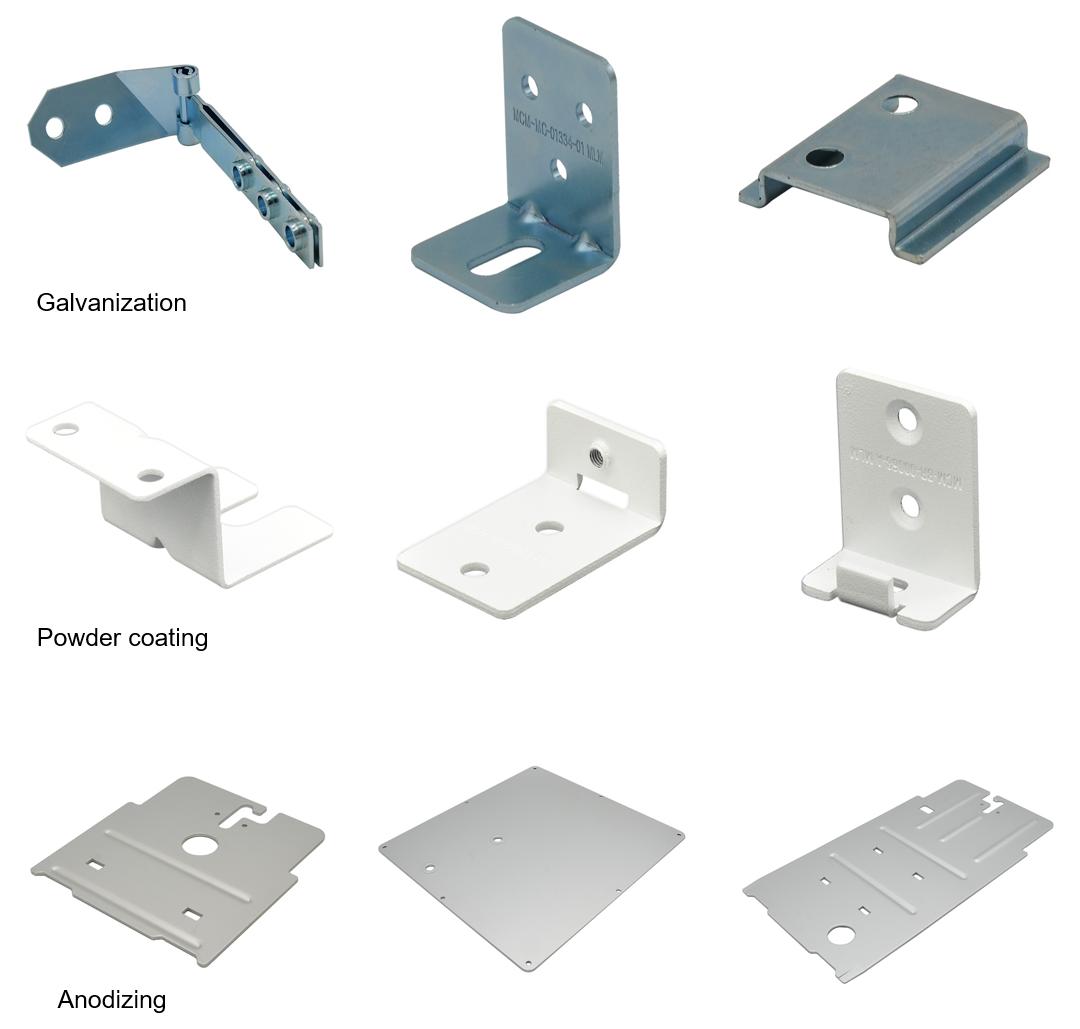
Sheet Metal Products for Home Appliances
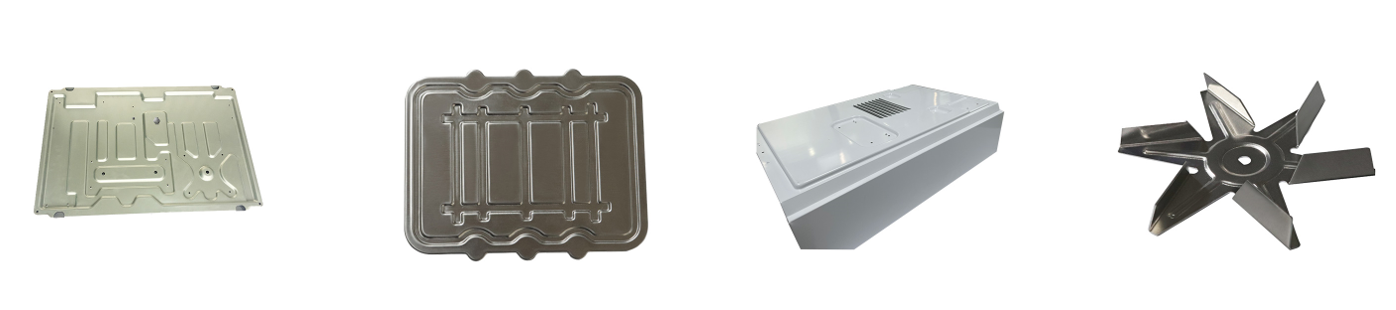
Automotive Sheet Metal Products
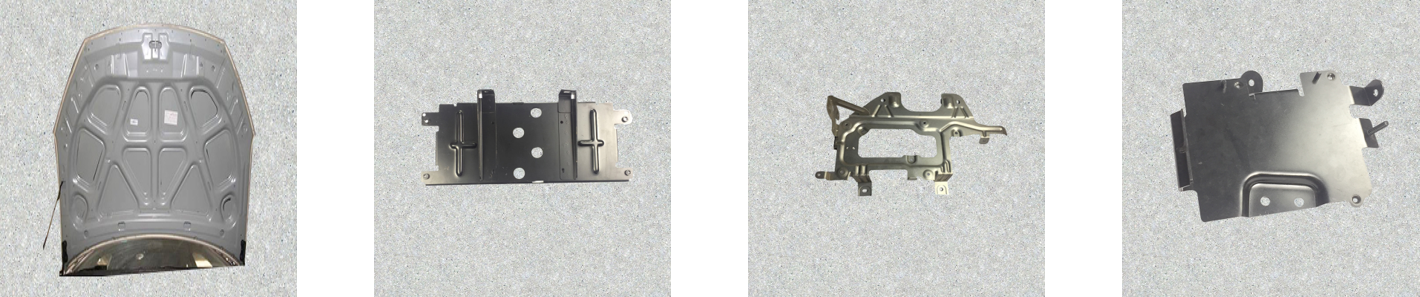
Sheet Metal Products for the Telecommunication Industry
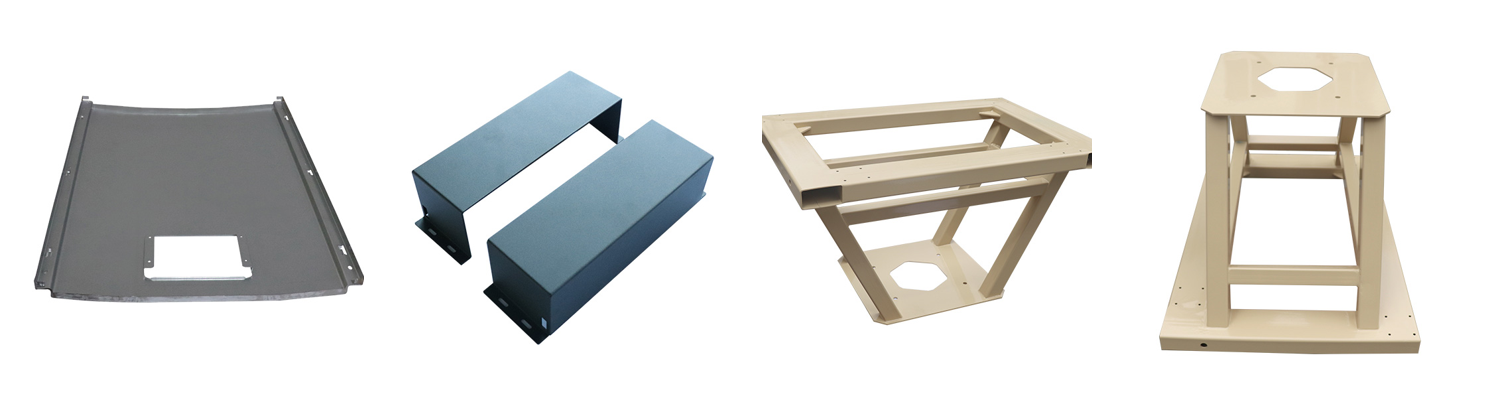
Sheet Metal Products for the Telecommunication Industry
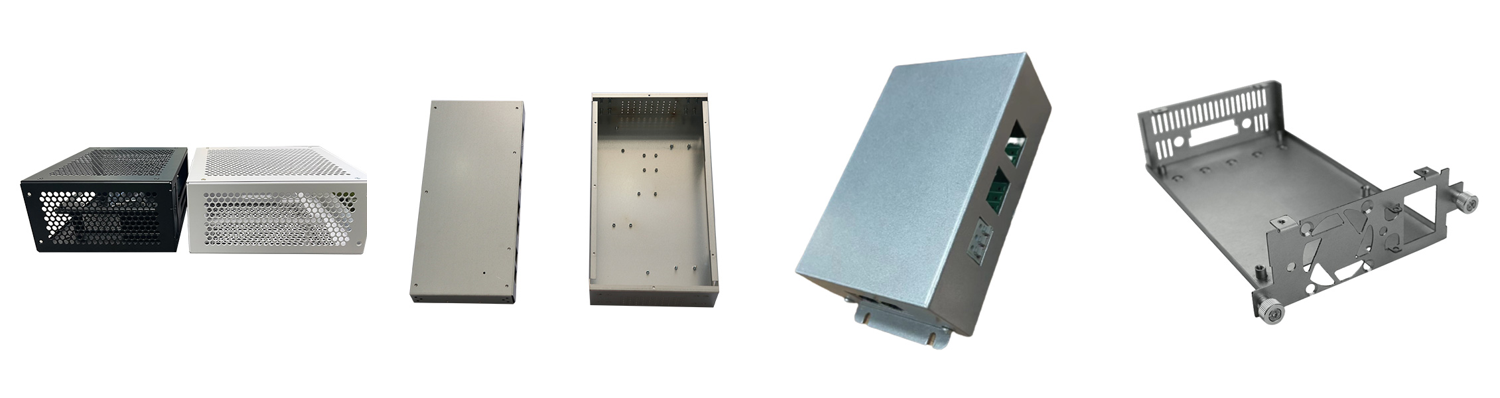
Sheet Metal Products for the New Energy Industry
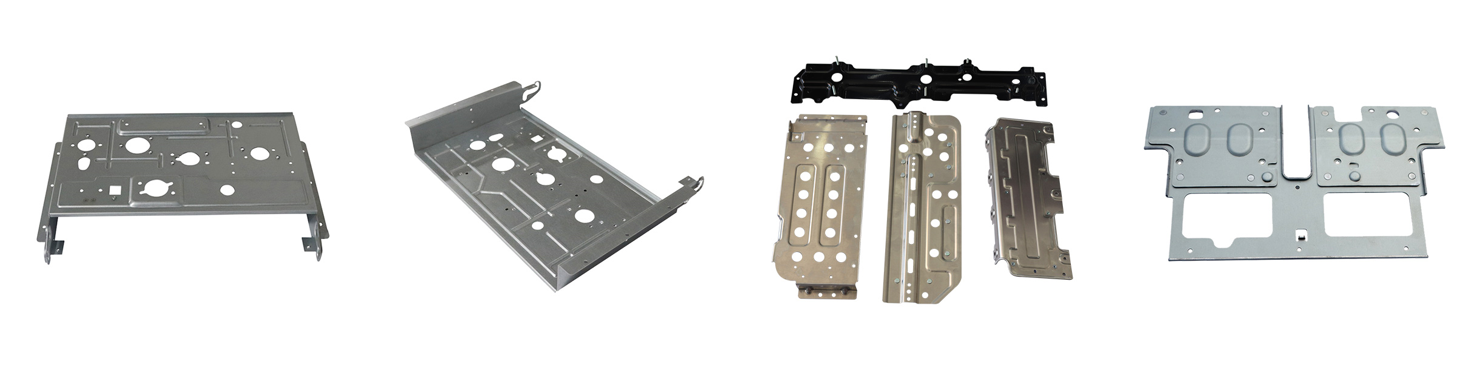