Engineering Design Team
The company's engineering design team has more than 35 people, including veteran designers with more than ten years of experience and high-level talents from Bao'an District, Shenzhen. HXC has obtained more than 20 national patents. After 18 years of development, it has obvious technical advantages in the following aspects.
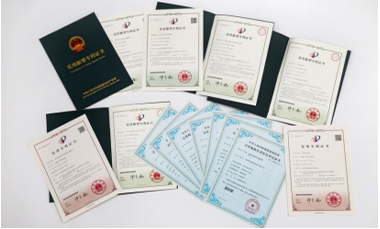
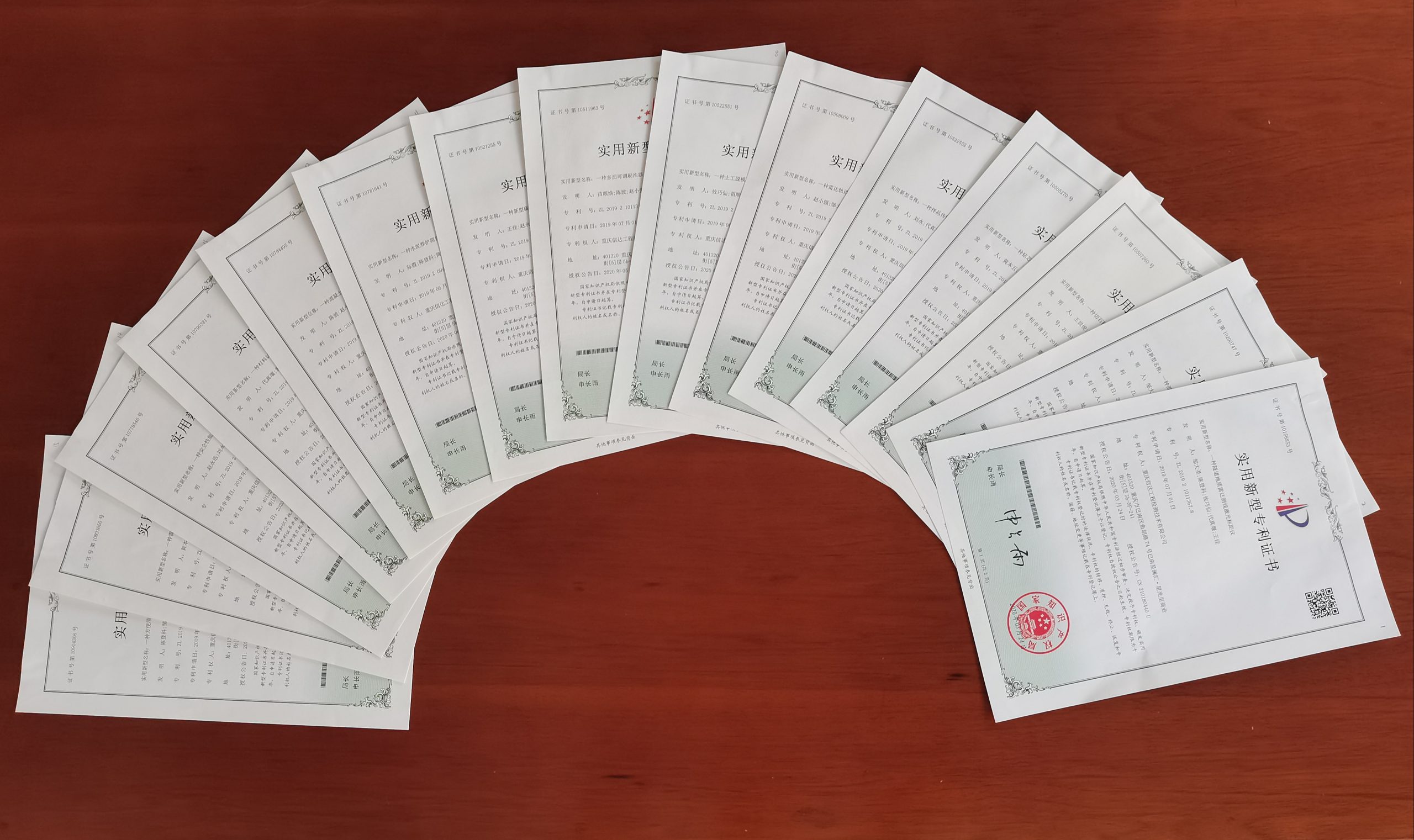
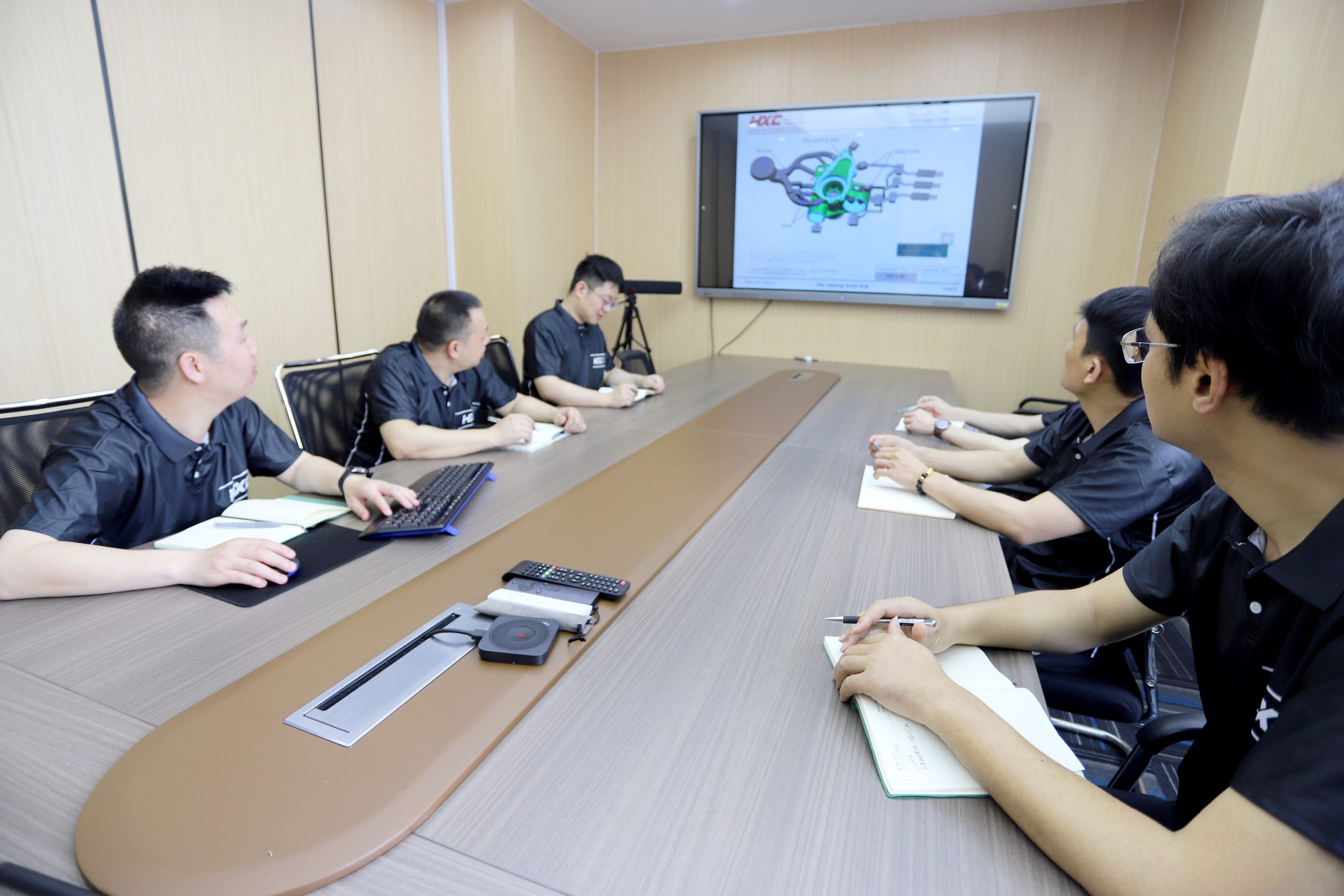
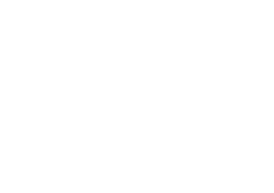
Complex moldstructure
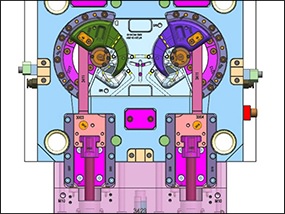
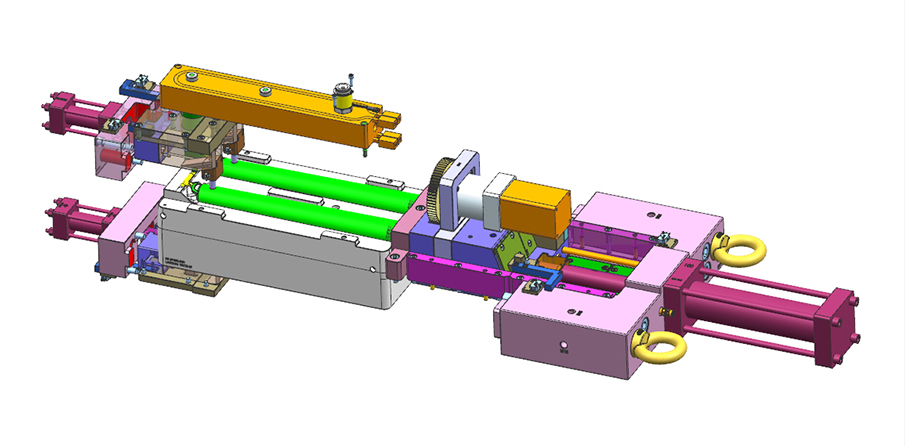
We can process various molds with complex structures to meet the production needs of different customers.
In this example: the product length is 600mm, and the middle core is sealed. The difficulty lies in ensuring that the product core cannot be eccentric and that the end of the core needs to be screwed. In terms of mold structure, the front end is supported by a cylinder to support the core. Before filling the rubber, the cylinder is withdrawn and filled again, and then the core is made into a servo motor to rotate the screw.
High-precision mold design and processing
In this case, we designed and manufactured a 10ml high-precision injection mold for virus collection tubes for Daan Gene, which is used for nucleic acid testing of the new coronavirus. We have delivered 5 sets. The 30ml high-precision injection mold for virus collection tubes has also been launched, and 6 sets have been delivered so far.
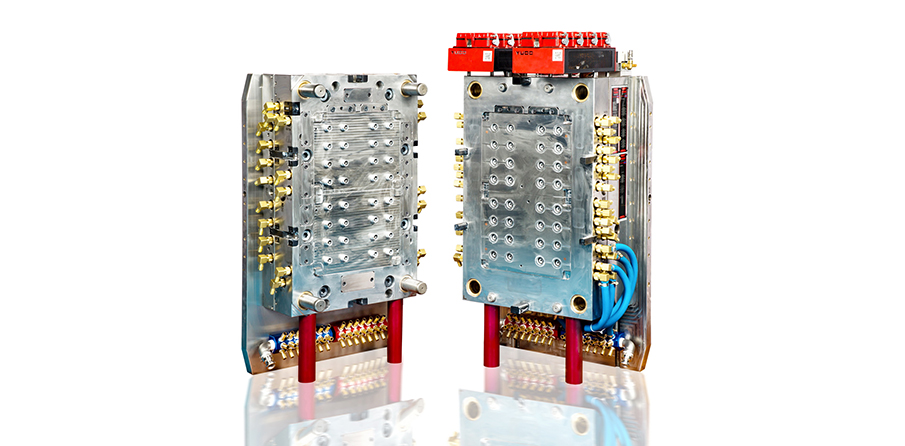
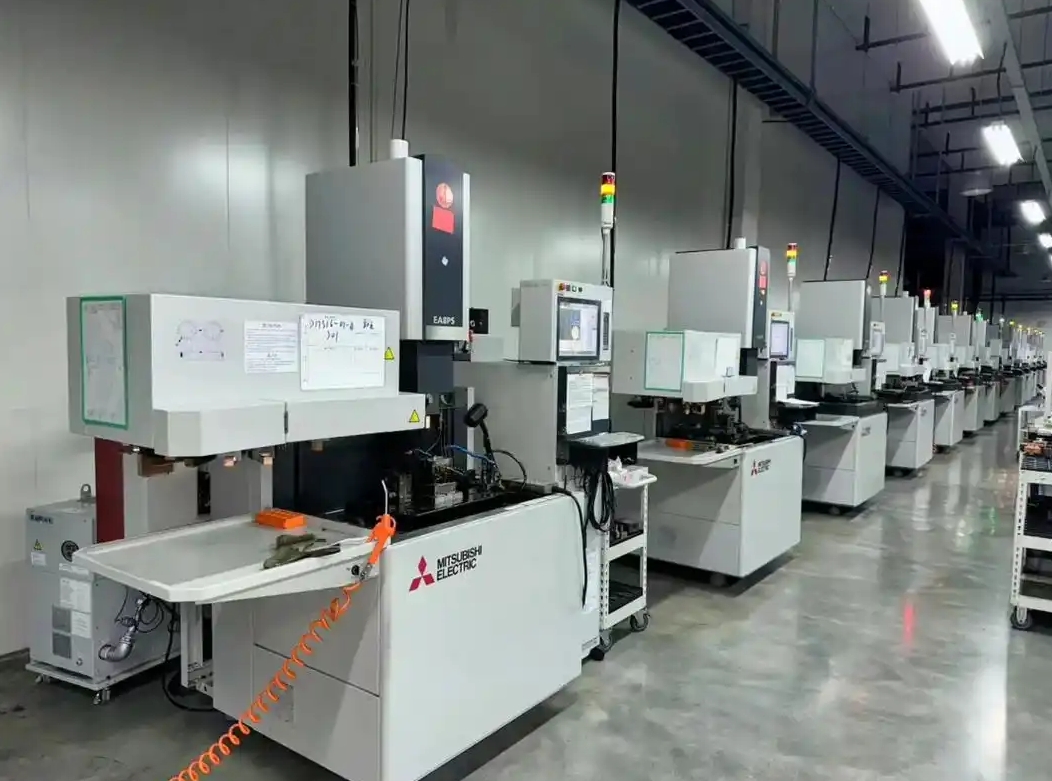
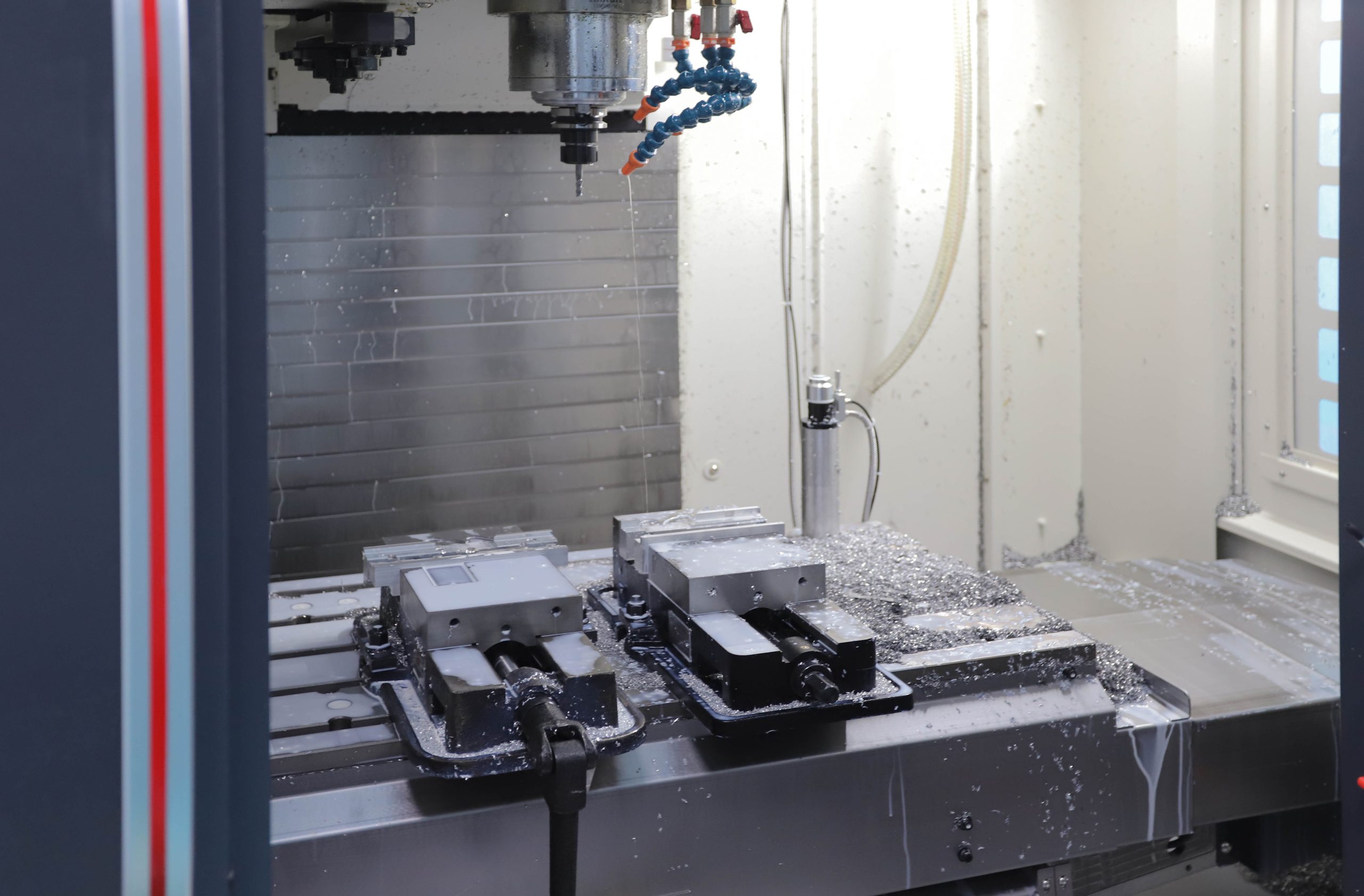
High-precision mold dimensional accuracy reaches 0.002mm
In terms of equipment, we have HERMLE 5-axis CNC machining center, AGIE spark machine, Sodick spark machine, Okuma, FANUC and other precision mold processing equipment to ensure the processing accuracy of the mold.
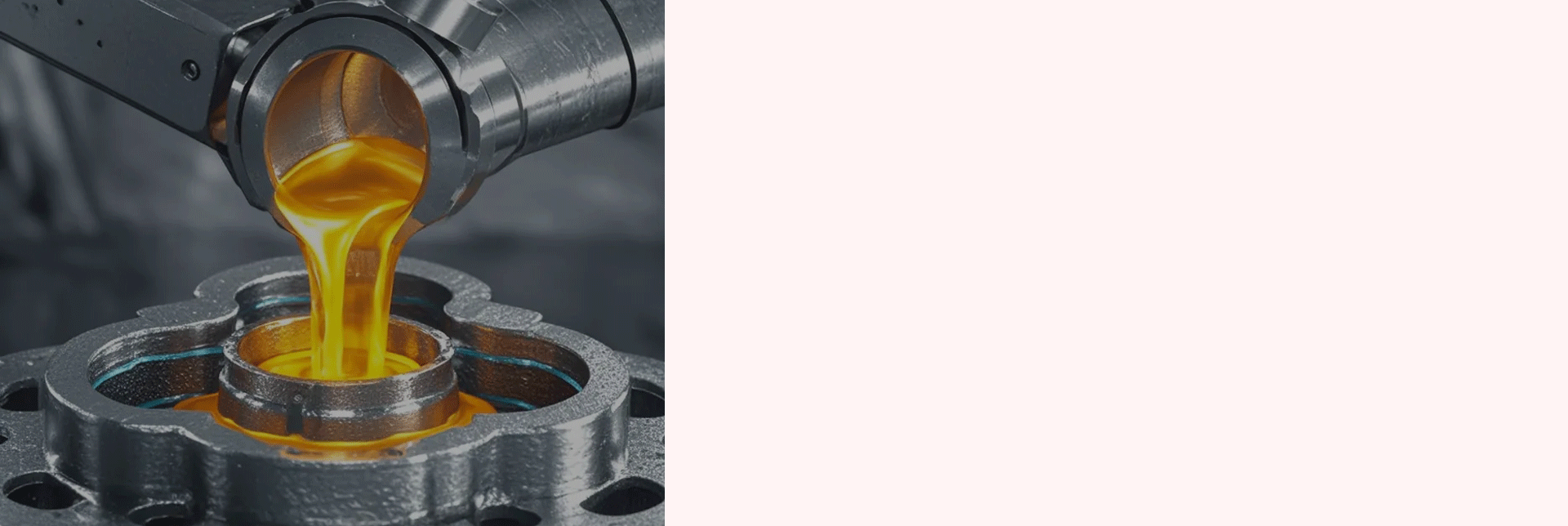
Conformal Cooling Technology
The traditional cooling method in mold manufacturing can only add straight water channels in the thicker area at the bottom of the mold, and the thin-walled position cannot be cooled, resulting in local sink marks and long cooling time. The mold casting surface is a thin-walled structure, and the traditional cooling water channel processing method cannot achieve the addition of water channels inside the thin-walled structure, so metal 3D printing is required to meet the full cooling of each part. Metal 3D printing is used to realize the conformal cooling flow channel processing of the thin-walled position of the mold insert; through this adjustment method, various cores and special channels inside the insert are produced with the help of 3D printing technology, and their structure and form perfectly adapt to the geometry of the special insert and its function in the mold. In order to achieve higher adjustment efficiency, the flow channel must be close to the outer surface of the component. After preliminary analysis and optimization design, the internal water channel of the mold has a better cooling effect.
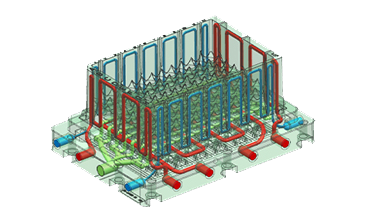
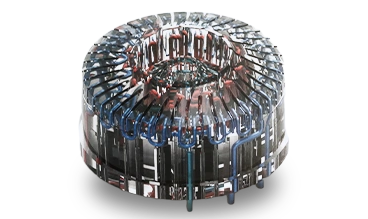
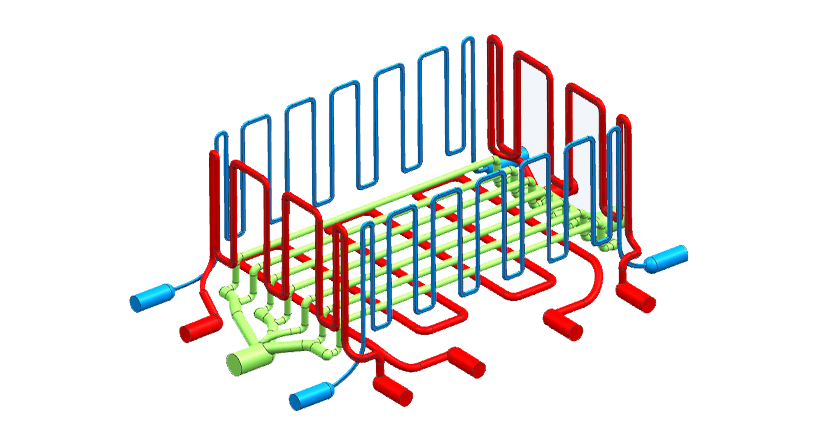
Thermal deformation management during processing
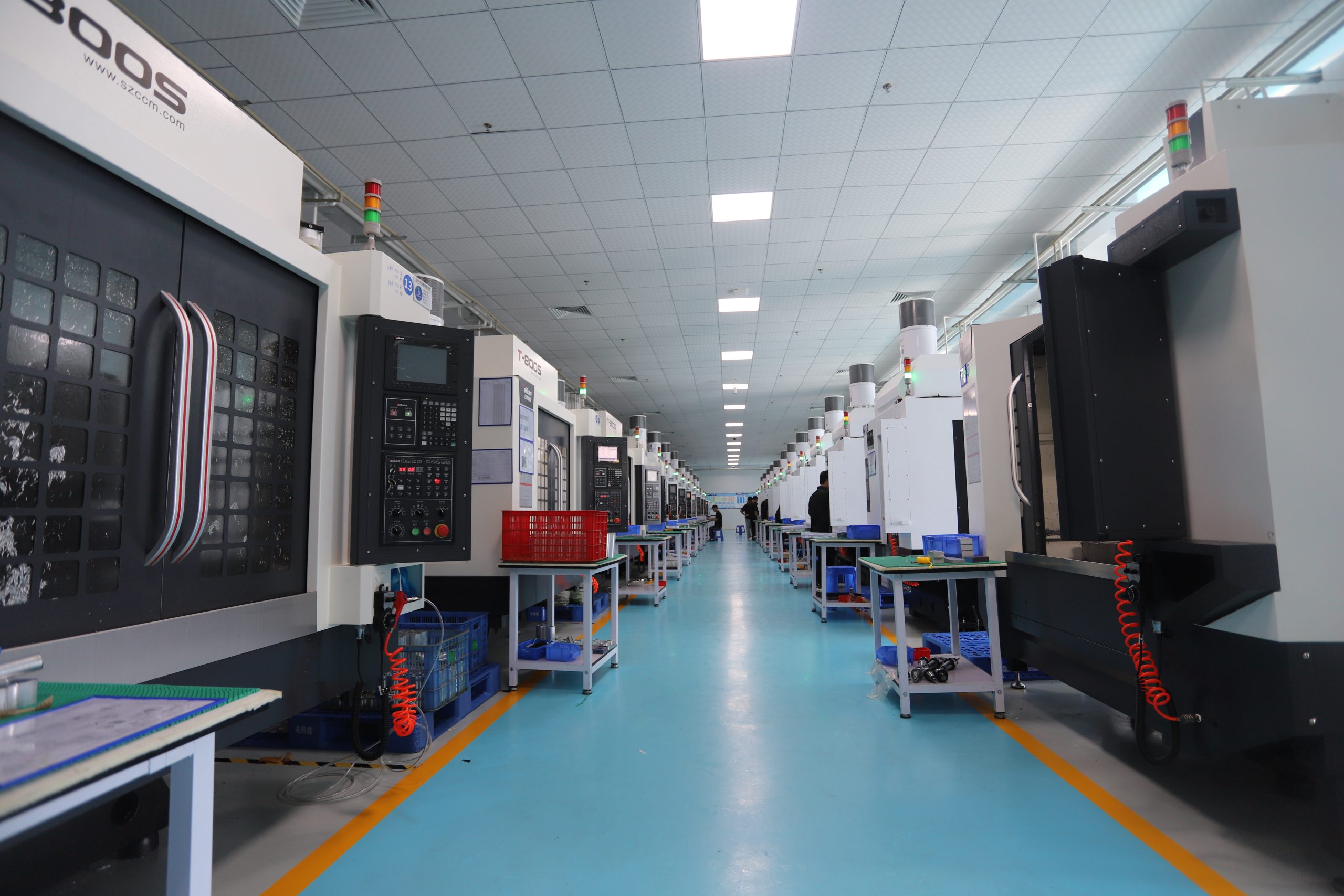
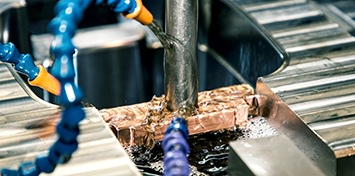
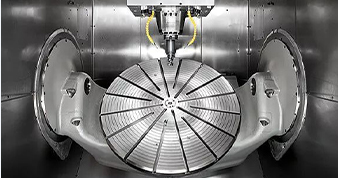
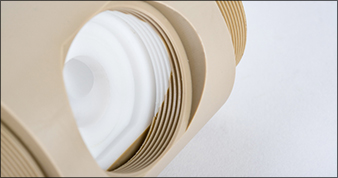