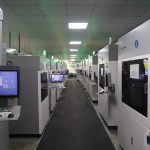
Bently GT3-R solution
2024-11-16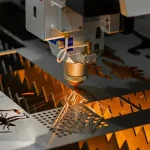
Application Case of HXC Precision Sheet Metal
2025-03-04
The processing advantages of HXC deep cavity molds:
Agricultural deep cavity mold solution
HXC has always provided one-stop industrial manufacturing solutions to customers worldwide, from rapid prototyping design and manufacturing of products to industrial mass production, using multiple processes and entering multiple fields, fully meeting customer requirements and exceeding customer expectations.
How to produce long and thin shallow parts with complex features with plastic mold?
When the depth inside is 441.6mm, the deformality and uneven thickness may occur during injection molding process. Solution:
After analyzing the structure and indication areas, we planned to produce two plug-in componenets to support the steel in middle. When teh material flow reaches to 90%, the blue insert will move backwards from the cylinder and the hole will fill the material.
The bottom of the product has threads,how to ensure demolding is possible? Solution:
We planned to rotate the mold out of the slider after analyzing the structure and indication areas.
Business capacity:
HXC's complete equipment is our greatest advantage in deep cavity mold processing. We possess over 100 CNC machining centers, including 4 German HERMLE five-axis CNC machining centers, as well as precision mold processing equipment such as AGIE EDM machines and Sodick EDM machines. Additionally, we have injection molding machines from brands like Okuma, FANUC, and Sumitomo Sodick. Furthermore, we have established a fully automated measurement laboratory equipped with coordinate measuring machines and a German GOM blue light 3D detection system.
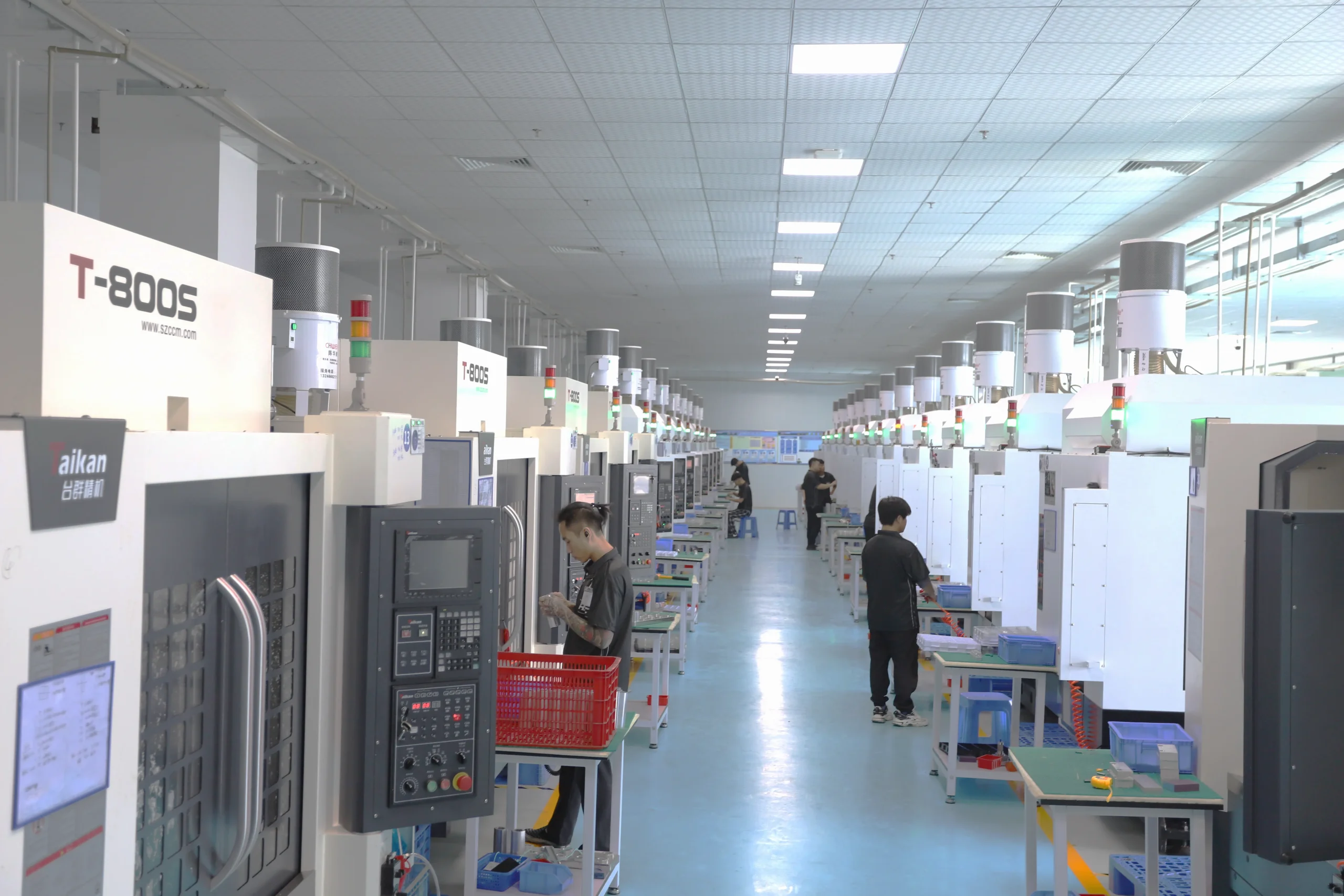
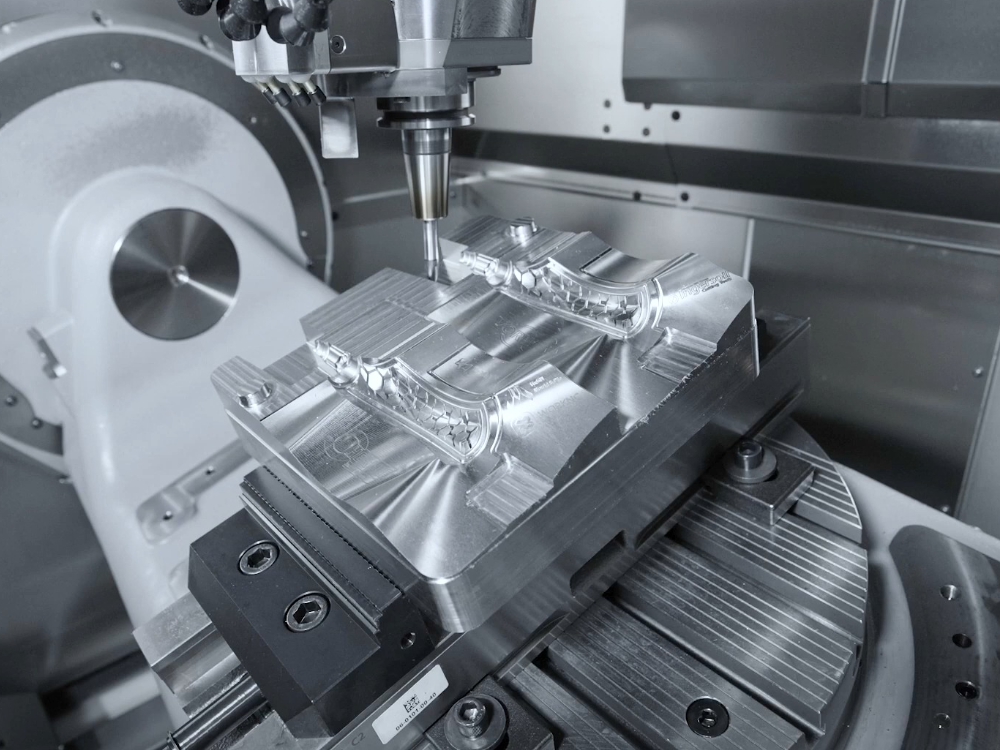
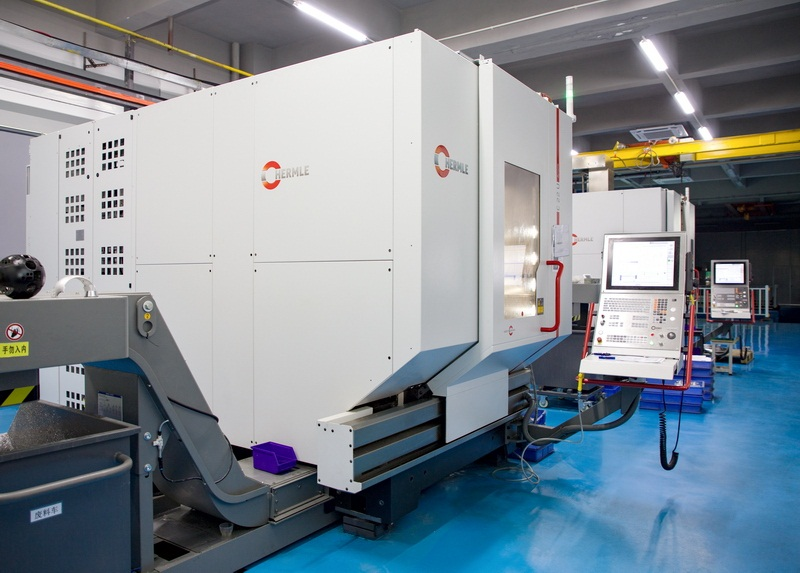
The Advantages of 5-Axis Machining for Deep Cavity Molds
The production cycle of HXC's deep cavity molds is usually controlled within 25 days. Our 4 German HERMLE 5-axis machines provide support for us. Because our 5-axis equipment can ensure the quality of our molds, the machining efficiency, and the manufacturing cycle. This is the core advantage of HXC, enabling HXC to maintain strong competitiveness in the manufacturing of deep cavity molds
1.mprove Machining Precision
2)Reduce Clamping Errors: Multiple surfaces can be machined in a single clamping, avoiding the repeated positioning errors caused by multiple clampings, and ensuring the relative position accuracy between various parts of the mold.
3)Optimize the Tool Path: 5-axis machining enables the tool to approach the complex curved surfaces of deep cavity molds at a more reasonable angle and path. The tool can always maintain the best contact state with the machining surface, achieving more precise cutting and ensuring that the dimensions and shapes of the mold meet the design requirements.
4)Avoid Tool Interference: Through the rotation and swinging of the worktable or spindle, the interference problem between the tool and the deep cavity part of the mold can be effectively avoided, and some narrow, steep or difficult-to-reach areas in the deep cavity mold can be precisely machined.
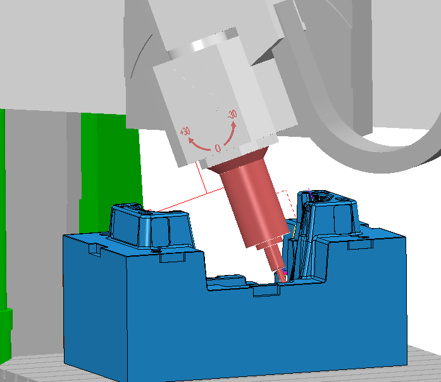
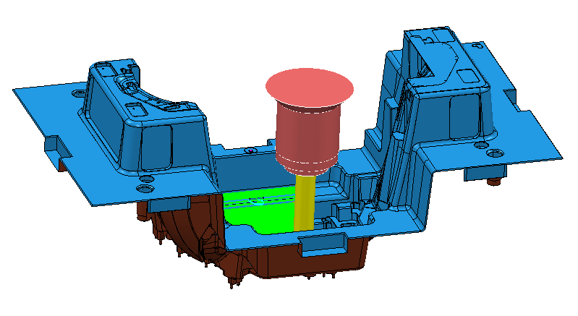
2.Enhance Machining Efficiency
1)Use Short Tools for Machining: When machining deep cavities, the tool angle can be adjusted through the rotation and swinging axes, and shorter tools can be used. Short tools have good rigidity, and higher cutting parameters can be adopted, reducing the cutting time.
2)Reduce the Number of Tool Passes: Machining can be carried out with a more optimized tool path. For complex deep cavity curved surfaces, the number of tool passes and the idle travel time can be reduced, shortening the overall machining time.
3)Achieve Simultaneous Machining of Multiple Surfaces: Multiple surfaces can be machined simultaneously. Unlike 3-axis machining, there is no need to change the tool and machining angle multiple times to process different surfaces separately, which improves the machining efficiency.
3.Improve Surface Quality
1)Avoid the Generation of Patterns: When machining the side walls and bottom surfaces of deep cavity molds, the tool can be kept perpendicular or at the best angle to the machining surface, avoiding the generation of rib-like patterns or tool marks caused by improper tool angles, and making the mold surface smoother.
2)Reduce Surface Roughness: The tool path of 5-axis machining is smoother, and the cutting force is more uniform, which can reduce the surface roughness and improve the surface quality of the mold. This is conducive to the flow and demoulding of plastics during injection molding, and improves the appearance quality of injection-molded products.
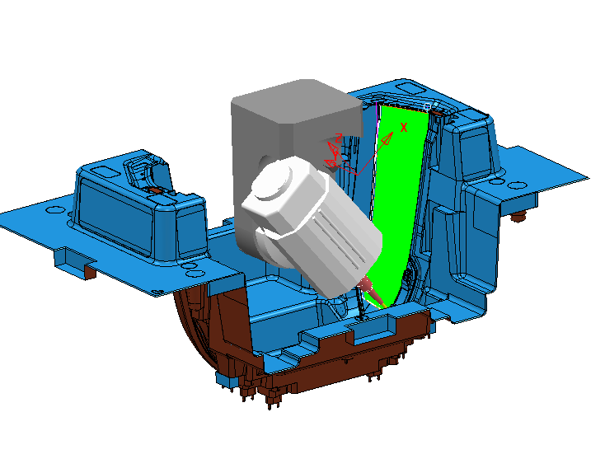
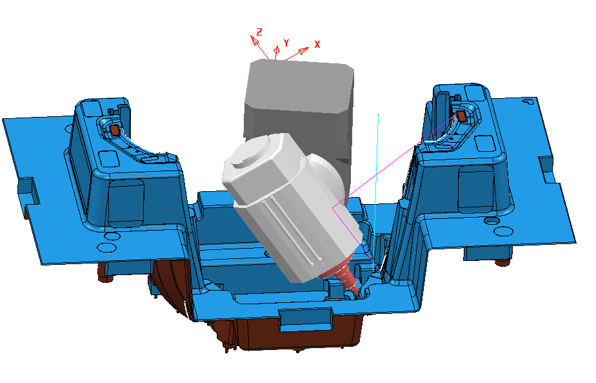
4.Enhance Machining Flexibility
1)Adapt to Complex Shapes: It can easily handle the machining of injection molding deep cavity molds with various complex shapes. Whether the mold has features such as free curved surfaces, inclined surfaces, deep grooves or narrow slits, it can be efficiently machined through 5-axis simultaneous motion.
2)Optimize Machining Strategies: Programmers can flexibly formulate various machining strategies according to the specific shape and machining requirements of the mold, such as side milling, plunge milling, spiral milling, etc., to improve machining efficiency and quality.
5.Reduce Machining Costs
1)Reduce Tool Wear: The tool works under more reasonable cutting conditions, with uniform cutting force. The wear rate of the tool is slowed down, and its service life is extended, reducing the replacement frequency and cost of the tool.
2)Save Fixture Costs: The dependence on fixtures is reduced. Regular workpieces can be directly clamped with a three-jaw or four-jaw chuck, and irregular workpieces can be clamped with one plane and two pins, reducing the design and manufacturing costs of special fixtures.
3)Improve Equipment Utilization Rate: A 5-axis machining center can complete a variety of machining tasks on one piece of equipment, reducing the investment cost and floor space of the equipment, and improving the utilization rate of the equipment and production efficiency.
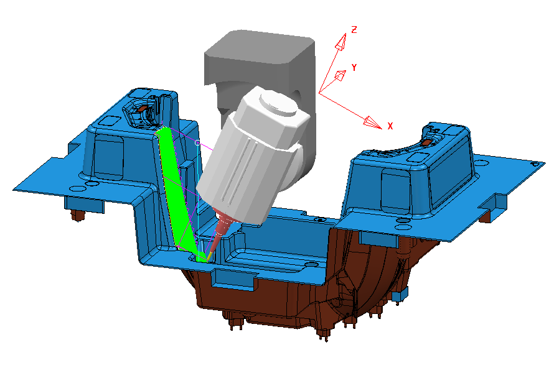
HXC has a precision plastic mold and injection molding processing team with rich theoretical and practical experience. The key members have over 20 years of experience in the mold industry and possess multiple core technologies and national patents in complex mold structures, mold flow analysis, conformal cooling technology, and processing thermal deformation management.
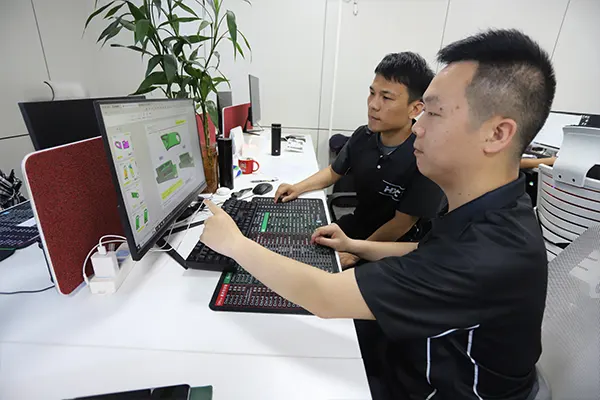
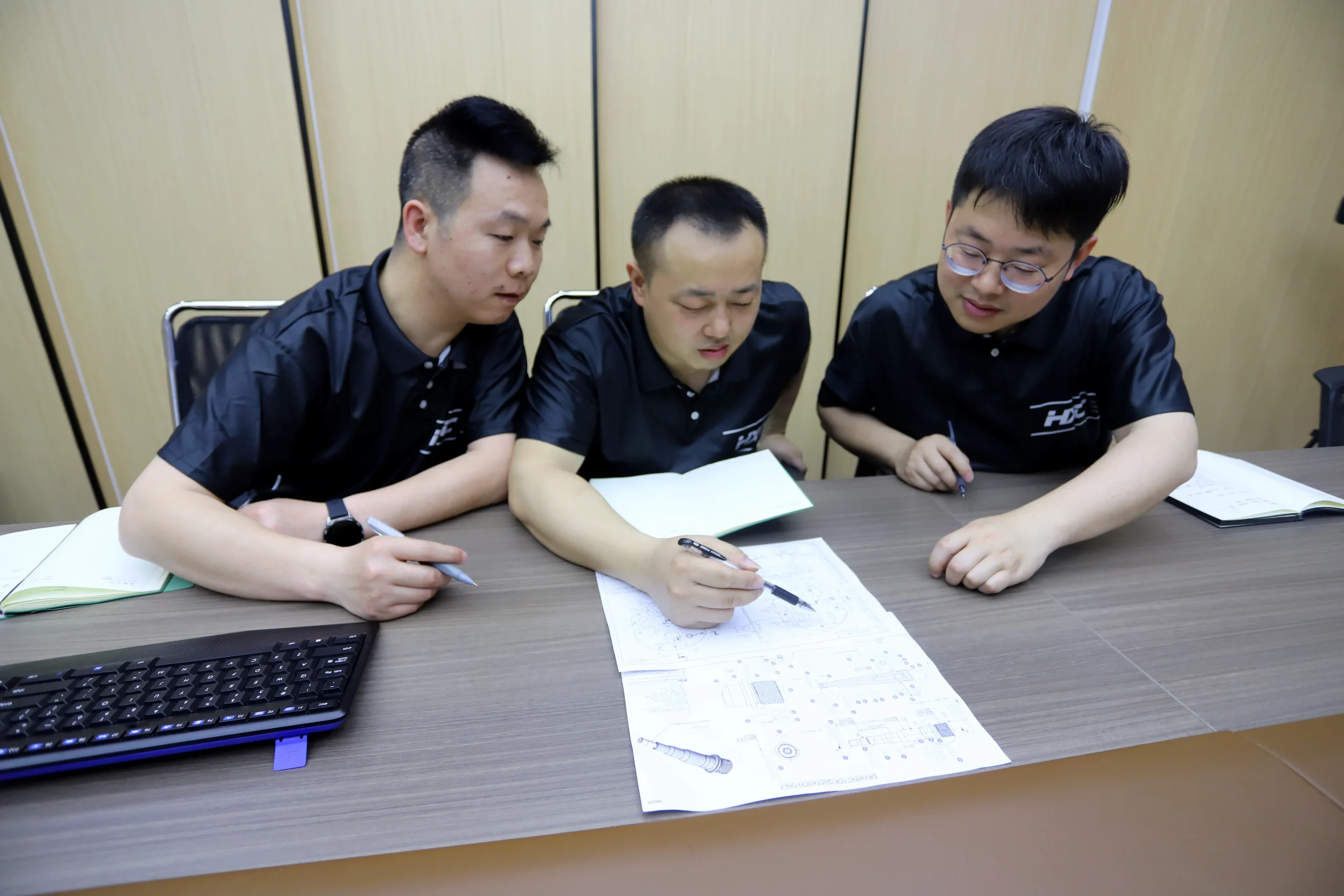
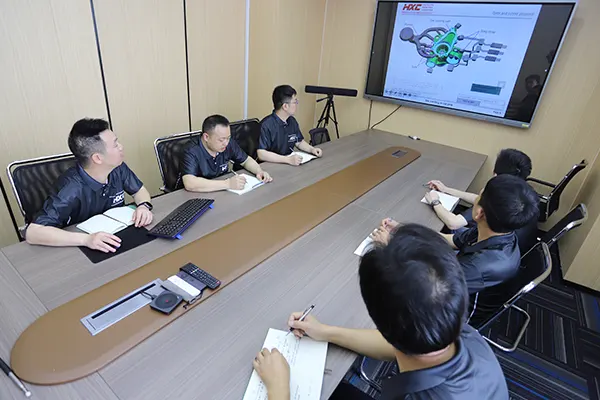
Display of HXC Deep Cavity Molds
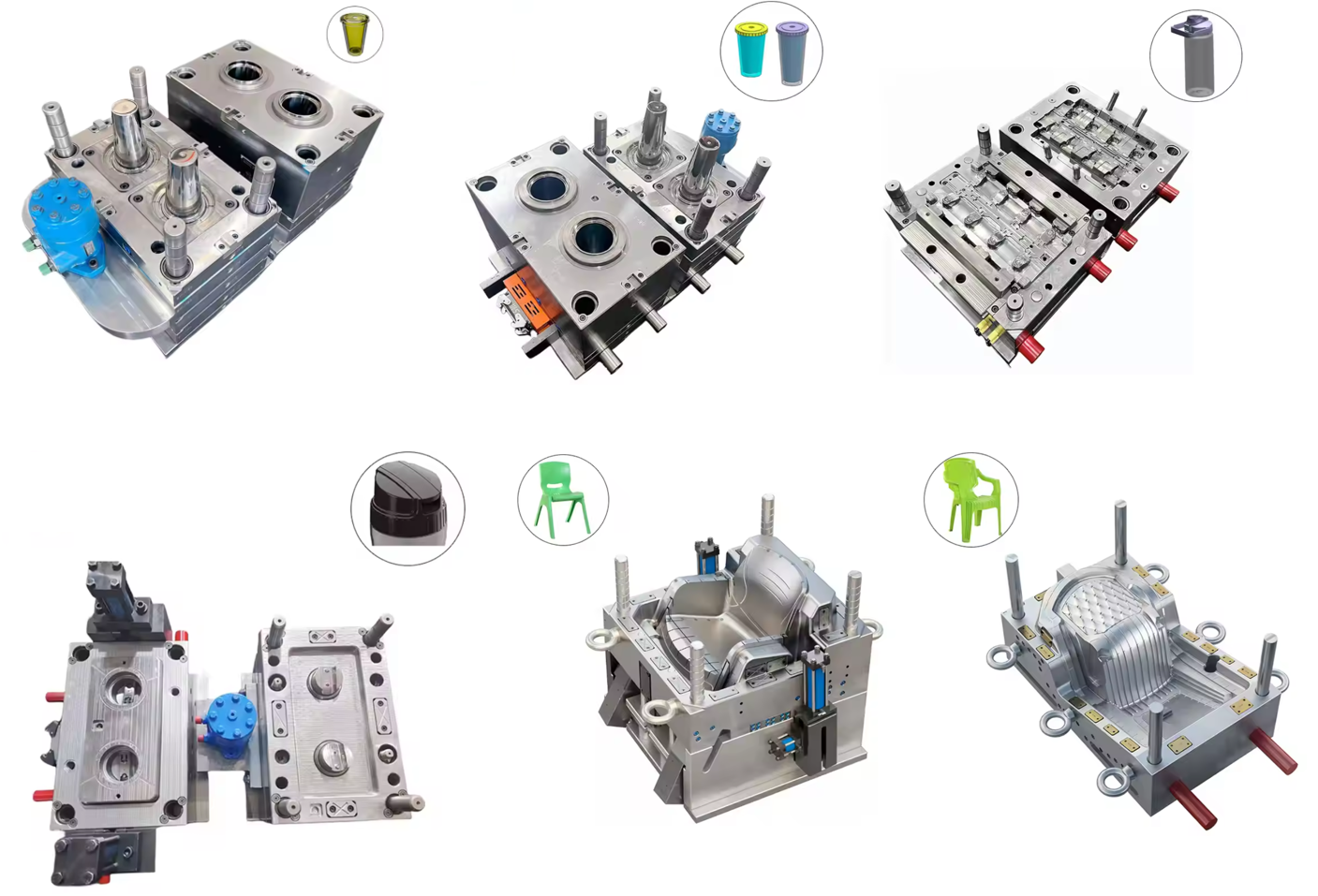