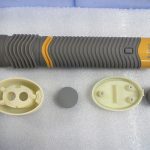
Prototype Case-Medical Cleaner
2025-04-15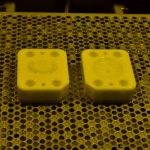
3D Printed Rapid Mold
2025-04-16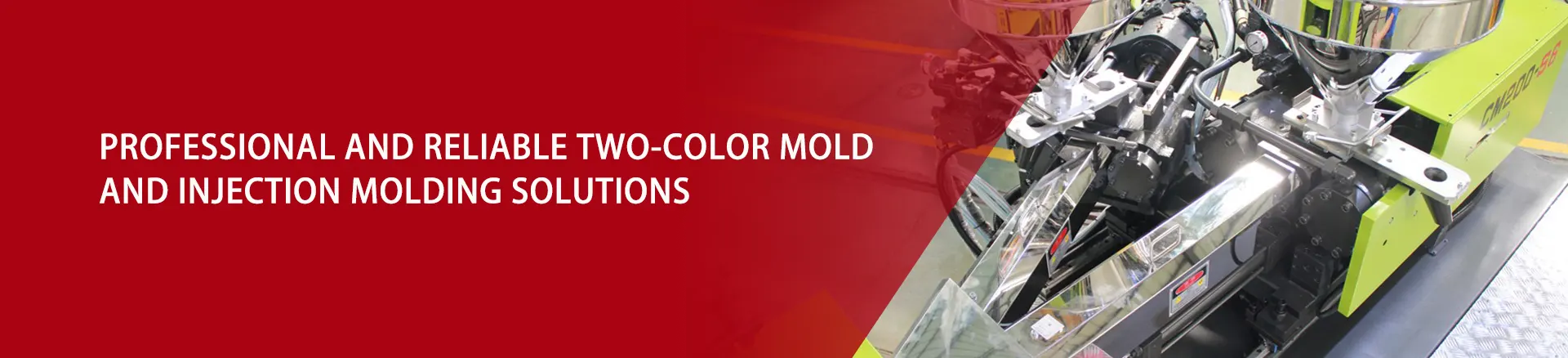
HXC - Expert in Two-color Injection Molding
Two-color injection molding is an efficient and cost-effective technology used to mold plastic parts with two or more types of rubber materials or colors in a single injection molding process, achieving a faster injection molding cycle.
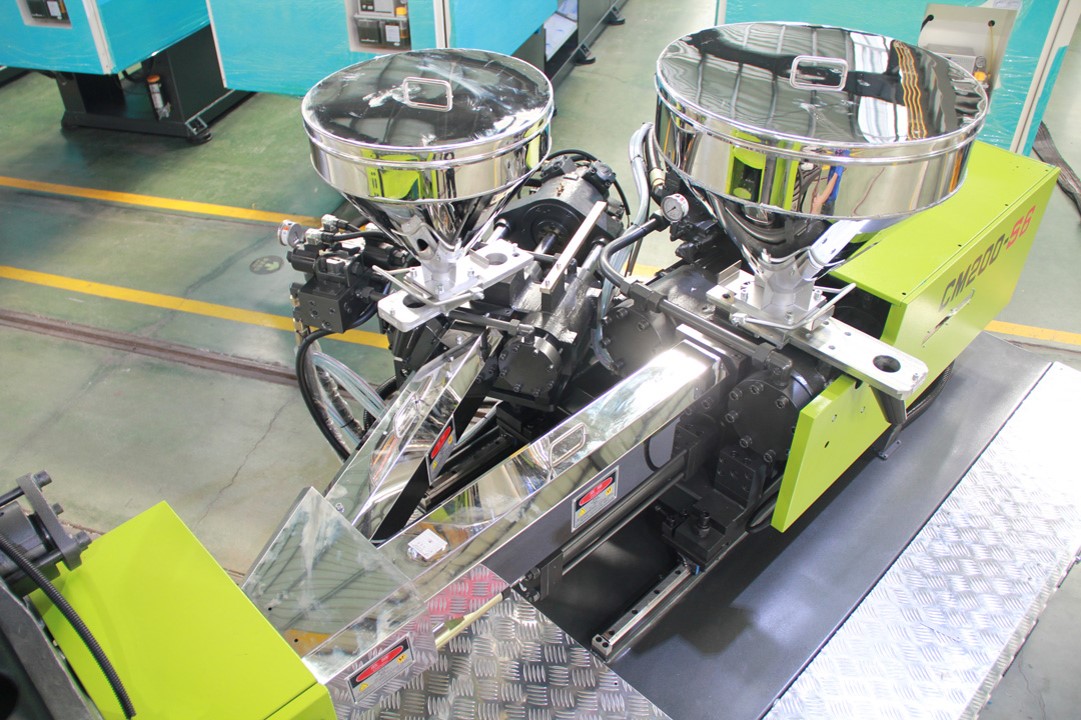
HXC has accumulated years of experience in the field of two-color injection molding and has completed numerous technically challenging projects. We possess mature two-color injection molding technology and have established core competitiveness in this field.
Introduction to Two-color Molds:
A two-color mold refers to a mold in which two types of plastic materials are injected and molded in the same injection molding machine. The molding process is carried out in two injection steps, while the product is only ejected from the mold once. Two different types of plastics are used, and these two plastics can be clearly distinguished on the product. This can make the appearance of the product more beautiful, and it is easy to change the color without the need for spraying. However, two-color injection molding requires specialized injection molding equipment.
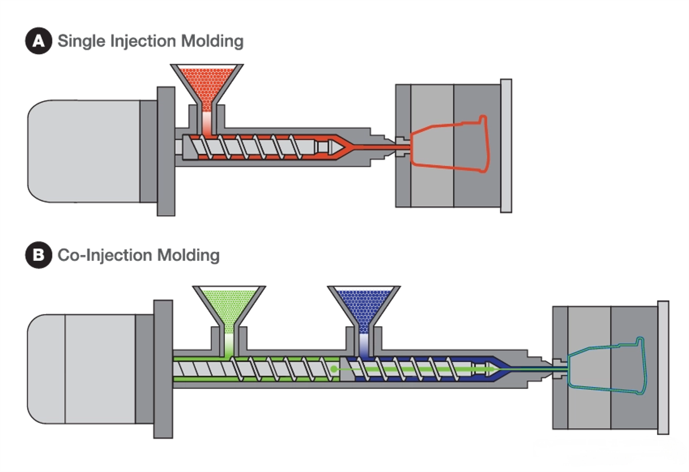
Two-color Injection Molding Machine
According to the different structures of the molds, different two-color injection molding machines can be selected. A two-color injection molding machine has two sets of injection systems, which can respectively plasticize and inject two types of plastics with different colors or different materials. These two sets of injection molding systems can be independent, or they can be installed on the injection molding machine in a superimposed or side-by-side manner.
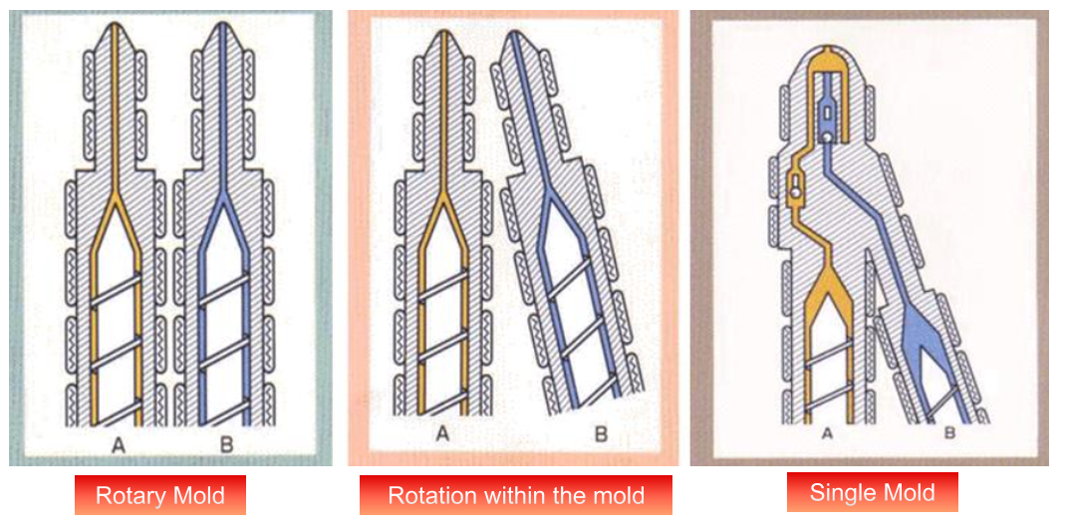
Structure: There are two commonly used structural forms of two-color molds, namely the core rotation type and the push plate rotation type.
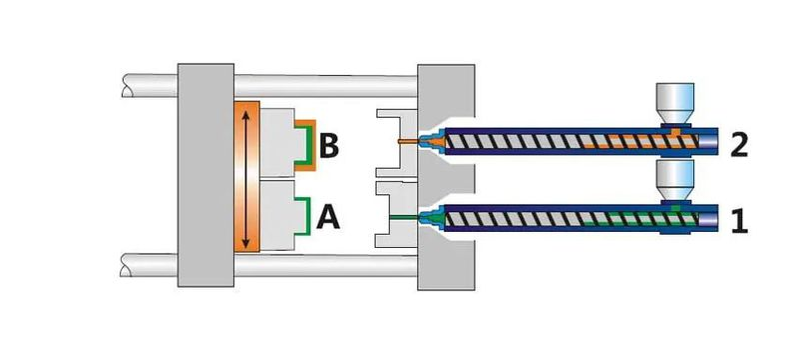
Core rotation type: The molds of this structure can be divided into integrated two-color molds and separated two-color molds. The biggest difference between them lies in the mold base structure. An integrated two-color mold only requires one set of mold base, while a separated two-color mold can be regarded as two complete sets of molds. This is the structure of this type of two-color mold.
Push plate rotation type: The principle of this structure is to use the rotation of the push plate part to realize the switching of the cavity, so as to achieve two-color injection molding. The structure of the push plate part of this type of mold is relatively complex. It is usually used for two-color products with high requirements for the appearance surface or extremely high precision requirements.

Push plate rotation type: The principle of this structure is to use the rotation of the push plate part to realize the switching of the cavity, so as to achieve two-color injection molding. The structure of the push plate part of this type of mold is relatively complex. It is usually used for two-color products with high requirements for the appearance surface or extremely high precision requirements.
Design Key Points:
The design of two-color molds is basically the same as that of general injection molds. However, what needs to be considered is the matching of the front and rear mold cores. Therefore, the total height of the two sets of molds and the center of the molds should be consistent. It is necessary to ensure that the two sets of molds achieve height matching after rotation.
Ten Critical Injection Molding Considerations for 2K Mold Design
Two distinct cavity inserts form individual product components, while the two core inserts maintain identical geometry.
The cavity side must rotate 180 degrees concentrically and achieve precise alignment with the core.
Verify machine specifications including maximum/minimum mold height, ejector pin spacing, and clamping force during design.
Three-plate tooling requires self-ejecting nozzle systems, with special attention to reliable ejection of flexible material nozzles.
Design clearance reliefs in the second-shot cavity to prevent damage to the first-shot component. Rigorously evaluate shutoff area integrity to avoid flash risks under high injection pressure.
Slightly oversize the first-shot component to ensure tight cavity registration during the second injection, enhancing sealing effectiveness.
Prevent melt flow from displacing the first-shot component during the second injection, which could cause dimensional distortion.
Implement balanced and uniform cooling channel layouts for both cavities and cores.
Given the deformation risks of flexible materials, 99% of applications involve molding rigid components first followed by flexible overmolding.
Optimize material adhesion through compatible resin selection (e.g., specialized TPU grades) and controlled mold surface finishes - smoother surfaces enhance bond strength.
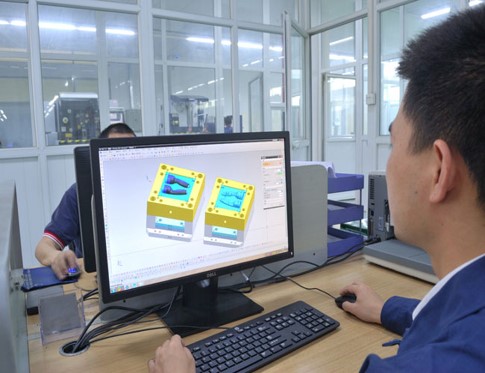
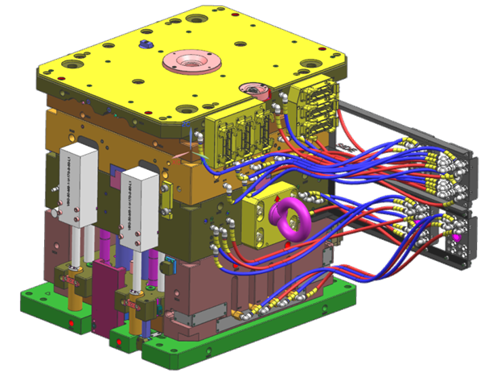
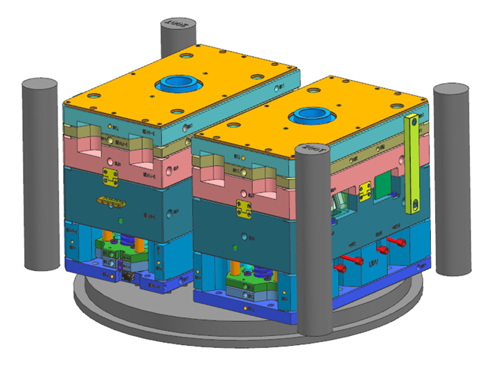
Advantages:
1:Improve product performance. When combining two materials, such as hard plastic and soft rubber, it can enhance the durability, comfort, and functionality of the product. At the same time, according to the characteristics of different materials, in addition to the color difference, the product can also have unique surface properties.
2:Optimize the appearance design. The application of two-color molds provides greater room for imagination in product appearance design. For example, when different colors and textures of the product are combined into one, it can create a more unique visual effect, which can meet the needs of both personalization and aesthetics, enhance the attractiveness of the product, and thus improve the product's competitiveness.
3:Increase production efficiency. Compared with the traditional process from injection molding to assembly, two-color injection molding can effectively reduce production processes, save production time, improve production efficiency, and reduce labor costs.
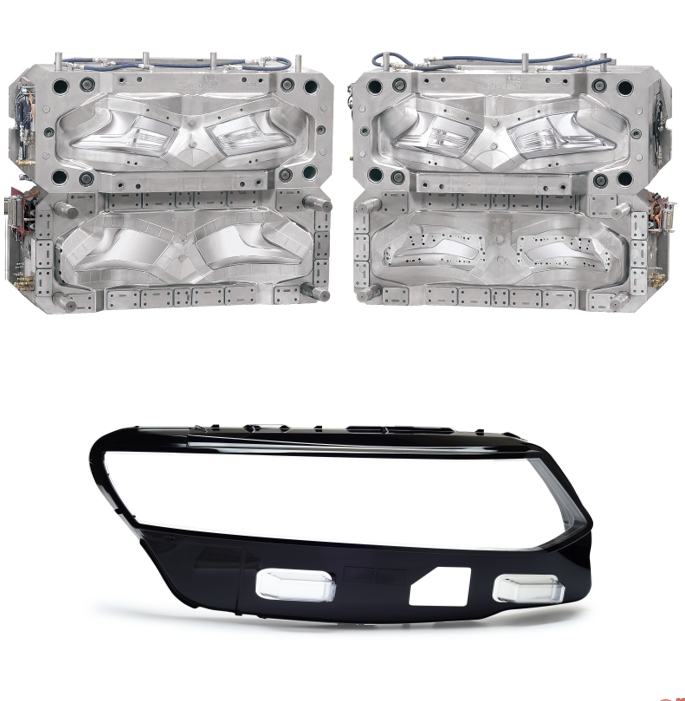
Application Areas:
Electronics Products: Such as mobile phone buttons, mobile phone casings, headphone casings, etc. Through two-color injection molding, the combination of different colors and textures can be achieved, enhancing the aesthetics and tactile feel of the products.
Power Tools: The handle parts of power tools usually adopt two-color injection molding, combining hard plastics with soft rubber or silicone to provide a better grip and anti-slip performance.
Home Appliances: Components such as buttons, knobs, and handles of home appliances are often manufactured using two-color molds to achieve different colors and tactile sensations, improving the overall quality of the products.
New Energy Field: For example, the battery casings of new energy vehicles, the casings of charging piles, and the casings of photovoltaic inverters, etc. Through two-color injection molding, high-strength protective plastics can be combined with materials with special markings or heat dissipation properties. This not only gives the products a unique visual effect on the appearance, highlighting a sense of technology, but also makes use of the characteristics of different materials to enhance the protective ability and heat dissipation efficiency of the casings, improving the practicality and durability of the products.
Automotive Products: Such as front headlights, taillights, turn signals, etc. The application of two-color injection molding technology can perfectly combine transparent and colored plastics to create unique and eye-catching lighting effects. The ingenious combination of the lamp cover parts in different colors and the internal lighting components not only enhances the recognition of the vehicle lights, but also makes the vehicle lights look more exquisite and high-end in terms of texture, adding unique charm to the appearance of the vehicle. At the same time, it optimizes the light penetration and scattering effects, ensuring driving safety at night.
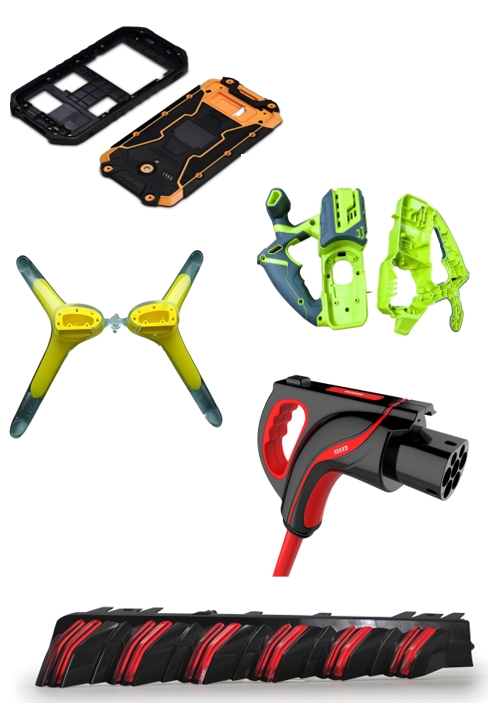
The Manufacturing Process of Two-color Molds
Mold manufacturing and injection molding production, providing one-stop service. With more than 20 years of experience in mold manufacturing and rich experience in the design of two-color molds, the quality is guaranteed
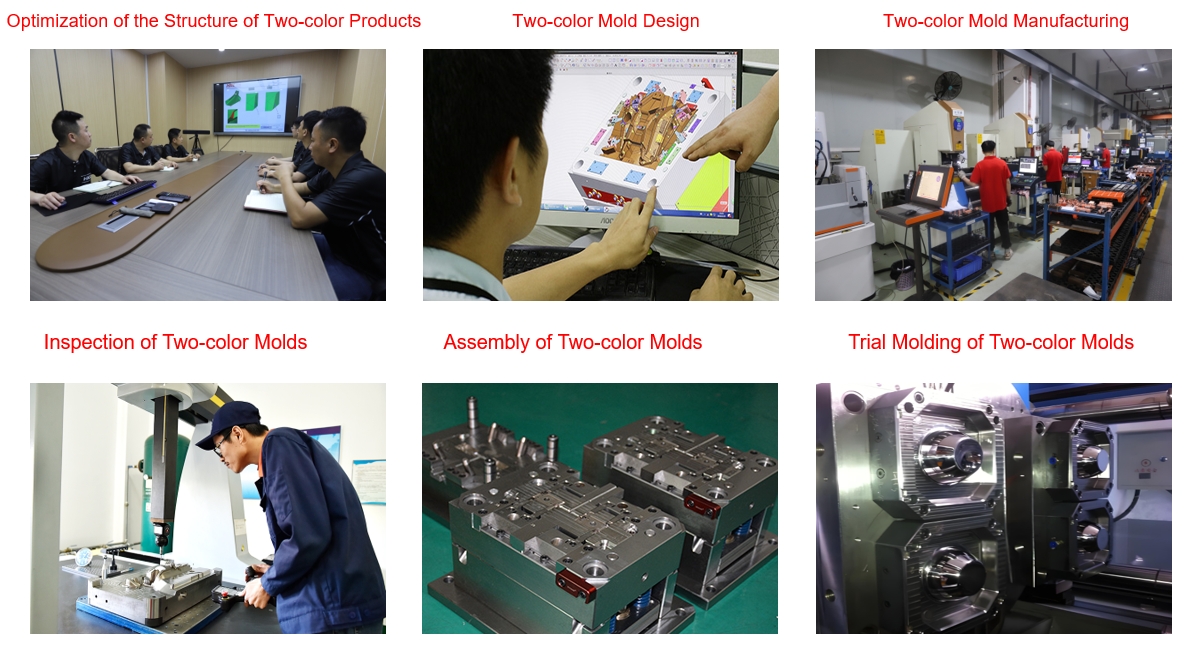